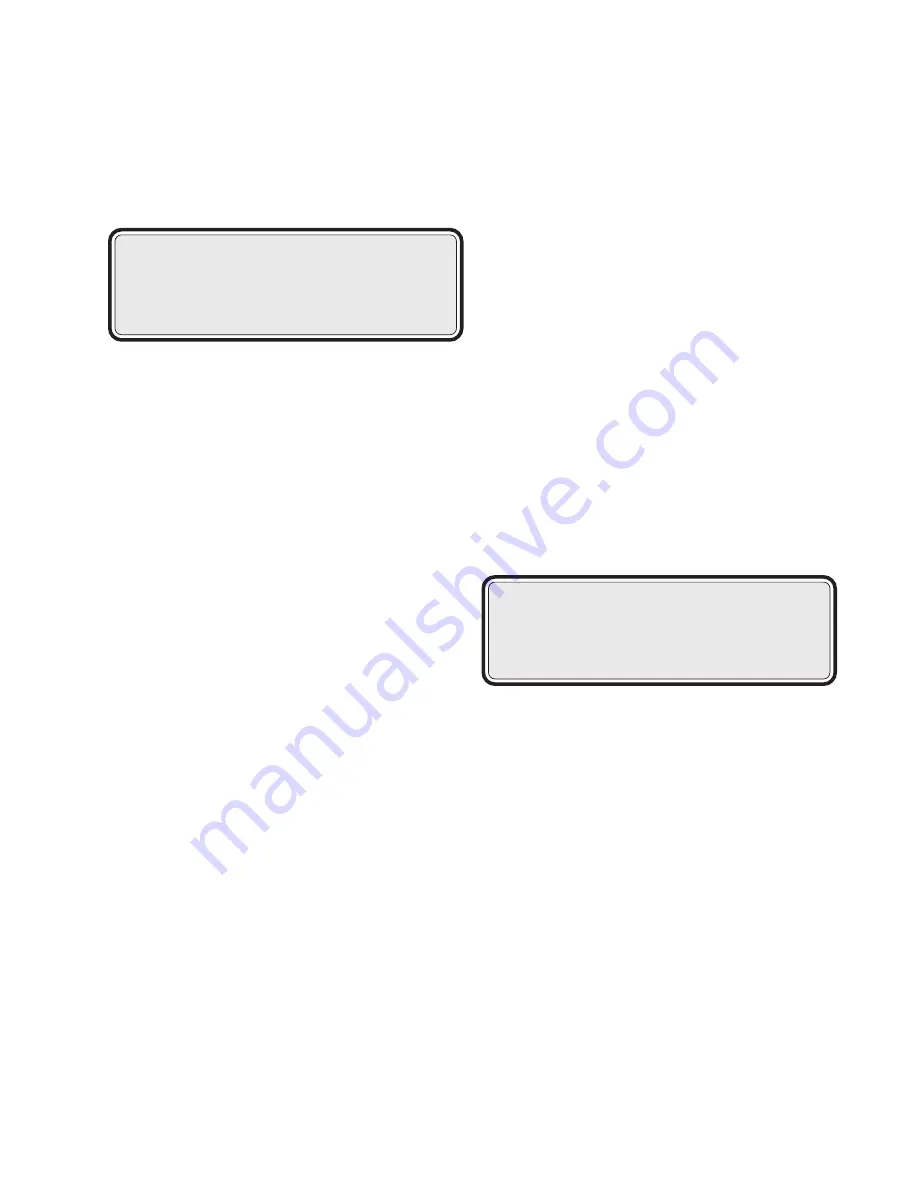
47
R-134a SERVICE INFORMATION
NOTICE:
Instructions given here are furnished as a guide. Persons attempting to use these instructions to make
repairs to the sealed refrigeration system should have a working knowledge of refrigeration and previous training
on sealed system repair.
VERIFY REFRIGERANT TYPE IN THE SYSTEM
CAUTION: R-134a and R-12 are completely
incompatible. Before starting any sealed
system repair, it is extremely important to
check serial plate of product to verify the type
of refrigerant in the system.
Dedicated Equipment
R-134a must not be mixed with other types of refrigerants.
R-134a must be recovered in dedicated and properly
identified recovery bags and tanks.
Check with the manufacturer of your recovery equipment
to determine R-134a compatibility. Some recovery
equipment manufacturers have changeover instructions
for switching between refrigerant types. Protect yourself
and your equipment by following all manufacturer
guidelines.
Also, ensure that your refrigeration hoses are spe-
cifically for use with R-134a refrigerant. Research
has shown that compounds in standard refrigeration
hoses may enter sealed systems and ultimately restrict
the cap tube in an R-134a system.
R-134a REFRIGERATION SYSTEMS
R-134 sealed refrigeration systems consist of the same
basic components utilized in the R-12 systems.
There is a 10% to 15% discharge pressure increase
using R-134a, with a 5% to 10% decrease in suction
pressure when compared to the same product with an
R-12 system operating at 90°F (32°C) ambient
temperature. Lower suction pressures result from the
lower density of R-134a refrigerant which effects refrigerant
flow rate. R-134a systems commonly operate in a 1”-2”
vacuum on the suction side.
Products using R-134a refrigerant will generally have a
longer capillary tube to maintain a similar flow rate.Some
models have a larger condenser to reduce the discharge
pressures and lower start-up sound transmission.
MISCIBILITY OF R-134a AND ESTER OIL
A special synthetic oil known as Ester oil is used as a
lubricant in refrigeration systems operating on R-134a.
Ester oils are produced from alcohols and fatty acids
and are available in several different variants. Ester oils
have a pleasant aroma reminiscent of fruit.
Ester oils generally include various types of additives for
improving certain properties such as viscosity,
temperature sensitivity, etc. These additives are often
aggressive, so skin contact with Ester oils should be
avoided.
One of the most important demands made on a refrigerant
system is that the oil mix with the refrigerant. Since
mineral oil and ordinary synthetic oil DO NOT mix with R-
134a, Ester oil is used for lubrication. Ester oil dissolves
in R-134a.
Ester oil is broken down by chlorine and cannot be used
with R-12 (R-12 contains chlorine) or any other compound
containing chlorine. Therefore, R-134a refrigeration
systems have virtually no tolerance for chlorine molecules
from CFC refrigerants (R-134a is an HFC refrigerant and
contains no chlorine).
CAUTION: During R-134a service, it is
extremely important to avoid using
equipment that may contain residual amounts
of mineral oil, CFC’s or HCFC’s which could
enter and contaminate the sealed system.
For example, hoses that were used in a refrigeration
system operating on R-12 may contain small quantities
of mineral oil which can block the capillary tube in a
system operating on R-134a. As little as one milligram
may be sufficient to cause a blockage. In addition,
sealed system components that have been used with
CFC systems must not be used with R-134a systems.
These components may contain residual amounts of
refrigerant and oil which could damage an R-134a
system.
At the earliest stage of developing R-134a, tests were
carried out on a different type of synthetic oil known as
Poly-Alkaline Glycol (PAG). This oil is also used in
certain air conditioning systems for cars. PAG and Ester
oil DO NOT mix with one another. Service equipment
used for R-134a / Ester oil must not come into contact
with PAG.
Summary of Contents for BEVERAGE CENTER II
Page 22: ......
Page 33: ...32 COMPRESSORWIRING Induction Run Compressor with Relay LADDER SCHEMATIC ...
Page 34: ...33 WIRING DIAGRAM ...
Page 61: ...60 ...
Page 62: ...61 ...
Page 63: ...62 ...
Page 64: ...63 ...
Page 65: ...64 ...
Page 66: ...65 ...
Page 68: ...67 Step 3 Step 4 Step 5 Step 6 ...
Page 69: ...68 Step 8 Step 7 Step 9 Step 10 ...
Page 70: ...69 Ice Maker Exploded View ...
Page 71: ...70 Ice Maker Wiring Diagrams Enlarged view ...
Page 77: ......