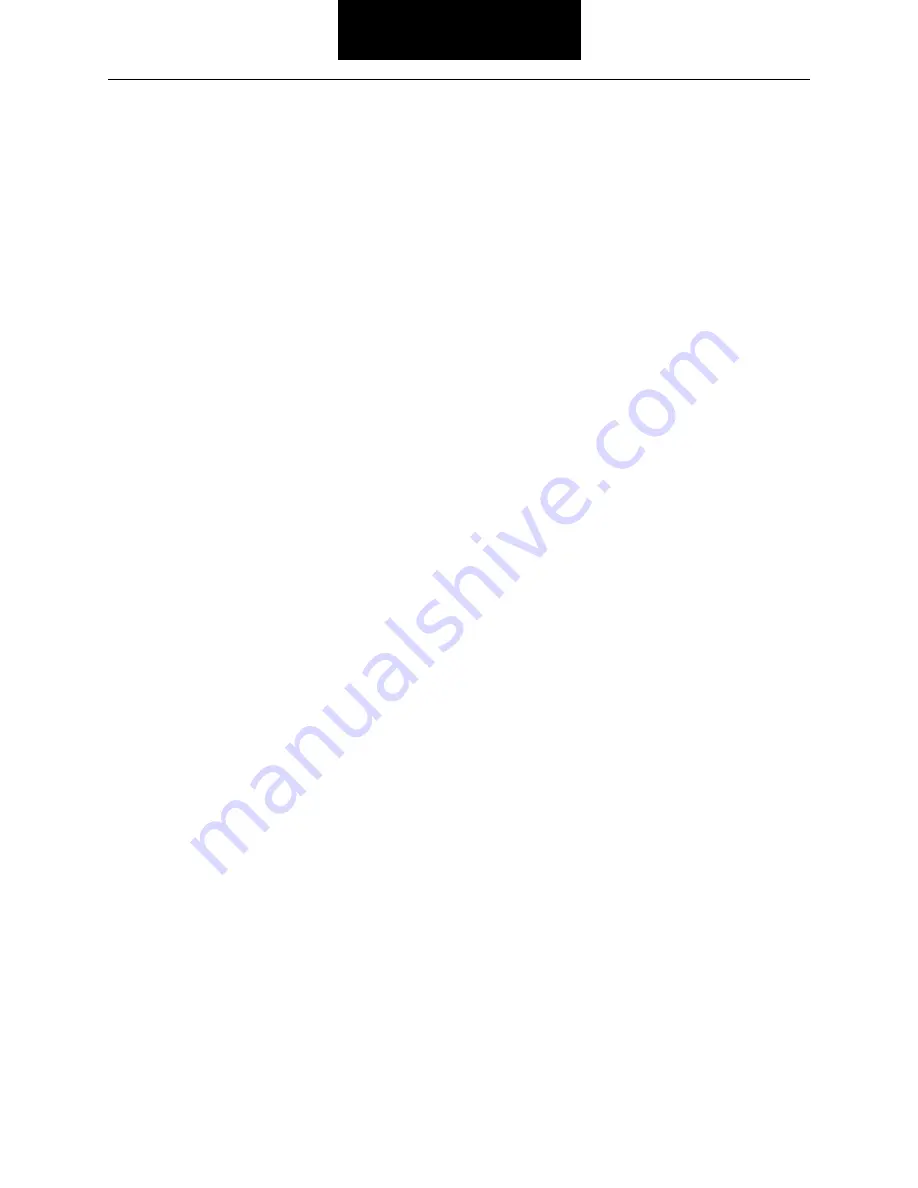
25
Electrical
Requirements
Cable
Soldering
No terminals shall be soldered unless specifically indicated on the individual print. The function of solder is to join two
or more metals at temperatures below their melting point. This provides metal and electrical continuity resulting in low
resistance connections. It also precludes corrosive affects from the junction. A solder point also allows for temperature
induced torsional stress without rupture of the joint. Solder connections shall conform to Eaton’s workmanship specifi-
cations. Flux shall clean the metal but not attack, corrode or oxidize the metal. Acid type flux shall not be used.
Splice
Splice clips are allowed. The splice clip shall be crimped and variac-soldered with 60/40 solder. Resistive weld is also an
approved method for splicing. Splices shall be insulated with 2-inch long, heat-shrinkable tubing.
Circuit Identification
Circuit identification shall be by either numbers/letters or color-coding. When numbers/letters are used, coding shall be
applied continuously along the length in approximately two to three inch increments. Code shall be visible at breakouts.
When color-coding is used, the color identification shall consist of a color stripe. If greater color combinations are
required, the cable shall have a color dash with stripe on opposite sides. Stripe and numbers shall be resistant to oil,
grease, dirt, and ethylene glycol.
Twisted Cables
2 conductor cables shall have 12 twists/foot. (16 and 18 gage cable only)
All cable lengths to multi-cavity connectors shall be cut and dressed to ensure no undue stress is on an individual wire
after insertion into the connector. After insertion, all terminals shall be checked for retention.