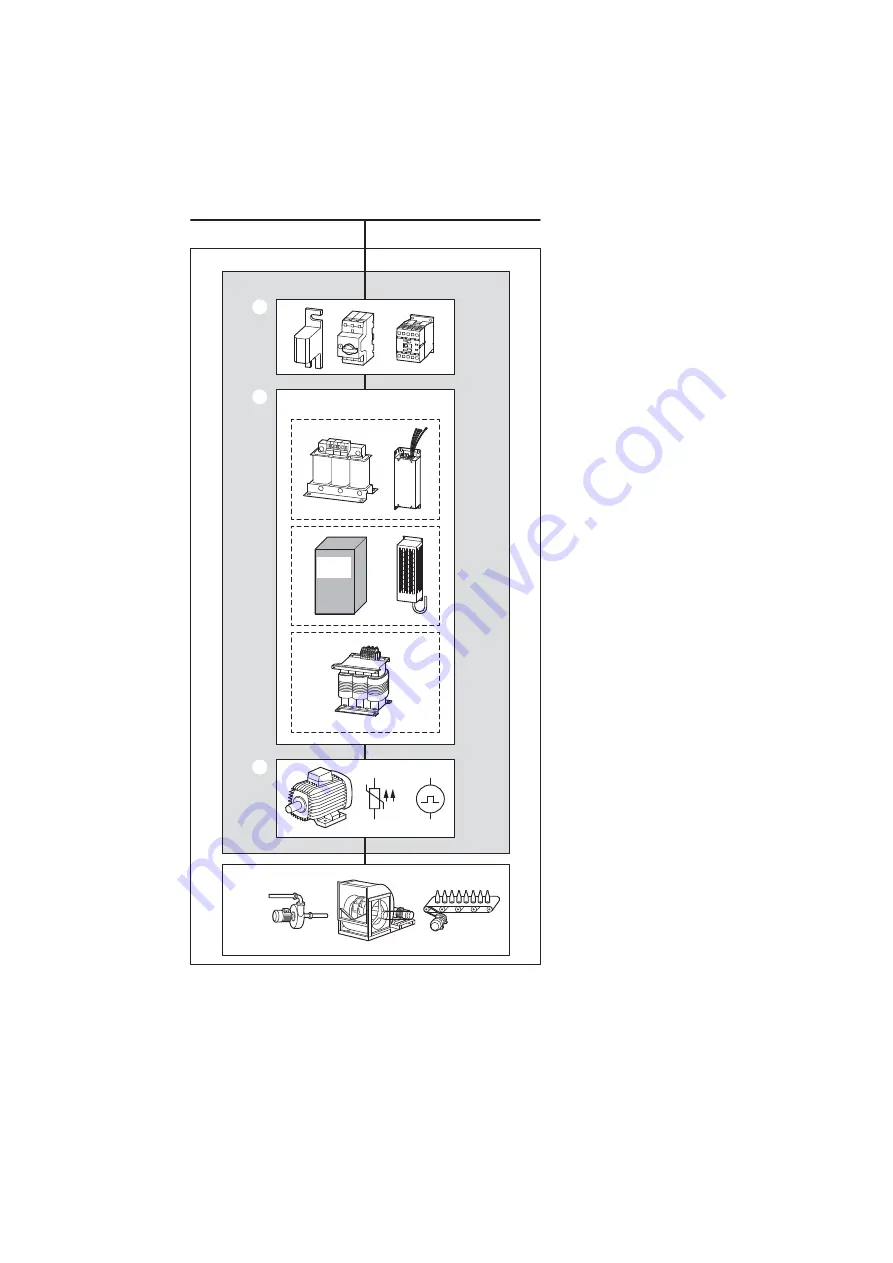
2 Engineering
2.1 Introduction
46
DA1 Variable Frequency Drives
08/18 MN04020005Z-EN
www.eaton.com
An example of adrive system
a
Electrical supply system
(mains connection, grounding system
configuration, mains voltage, frequency,
voltage balance, THD, compensation
systems)
b
Overall system – consisting of motor and
load systems
c
PDS = Power drive system
d
Safety and switching
(disconnecting devices, fuses, cable cross-
sectional areas, residual current circuit-
breakers, mains contactors)
e
CDM = Complete drive module:
Variable frequency drive with auxiliary
equipment (mains and motor chokes,
radio interference suppression filter,
brake resistor, sine wave filter)
BDM = Basic drive module:
DA1 Variable frequency drive
f
Motor and sensor
(Temperature, motor speed)
g
Load system:
Driven system equipment
Figure 30: Drive system example (overall system as its own system or as part of a larger system)
ϑ
n
BDM
M, n
PDS
CDM
⑥
⑦
⑤
④
③
②
①