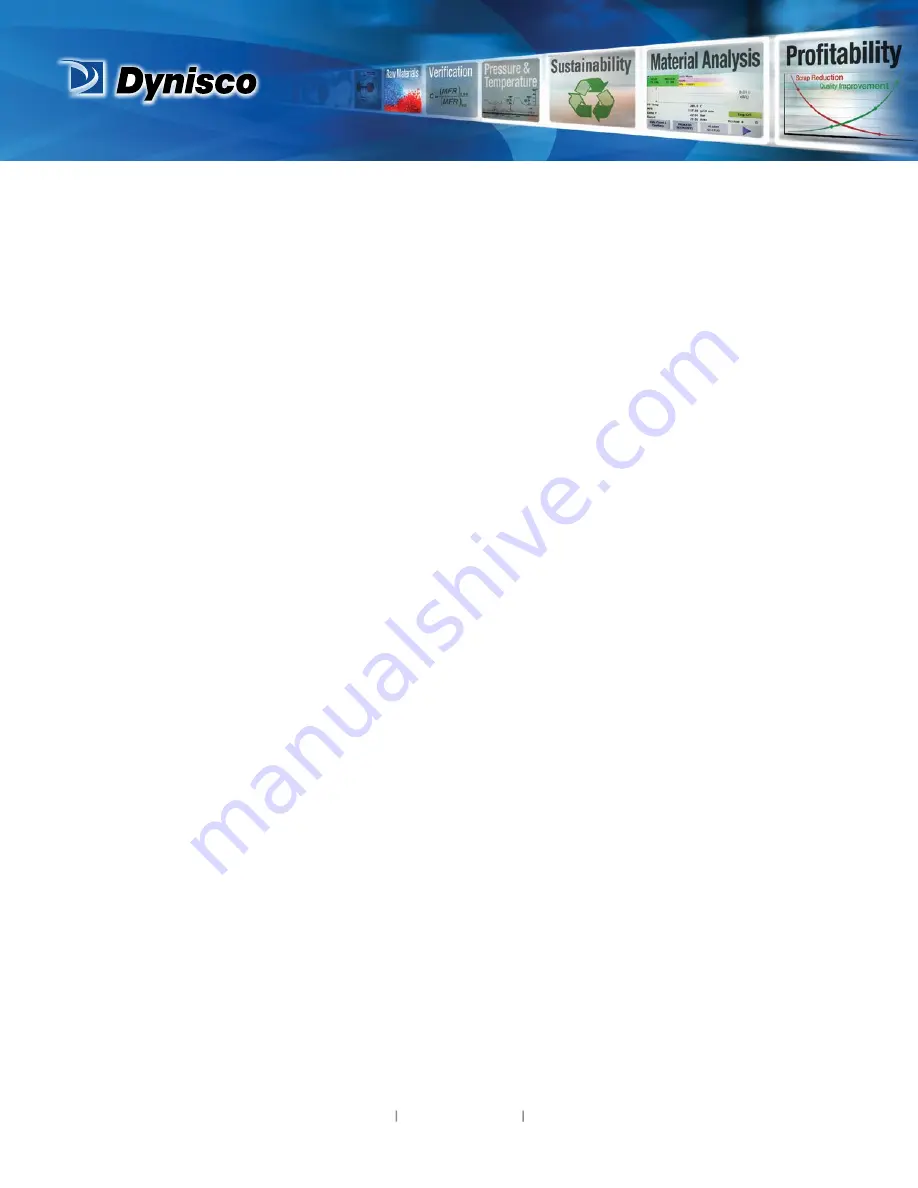
From lab to production,
providing a window into the process
-17-
www.dynisco.com
Rev: n/a
P/N: n/a
ECO: n/a
Manual to Automatic transfer:
When transferring from manual control to Automatic control there are two methods:
Bumpless Mode (without modification of set point) and Set Point mode (when the
current Set Point is modified it will be set to the actual measured input value). If in
Manual mode runs as open loop i.e SP is really the percentage output power, hence
how the transfer can be bumpless or SP change.
Input n Calibration
Set the percentage of range the calibration shunt resistor needs to be set at between
40%and 100%. Default 80%
Start Input n Low Point Calibration Press +keys to begin calibration procedure
Start Input n HIgh Point Calibration Press +keys to begin calibration procedure (Can only be accessed once a
successful low calibration has been completed)
Error Messages
Count Fail
means the low calibration will fail if the offset is less than -10mV or
greater than +10mV. This signifies potential faulty sensors or the high
calibration will fail if the count value is less than +20mV or greater than +50mV. This
signifies potential faulty sensors RCal Fail means the high calibration will fail if the
mV value is within 10mV of the low calibration value. This is a potential RCAL failure.
Control Configuration
Control Type
w Select From Pressure or Single/Dual**
Power Up Control State
Select From Automatic Control or Manual control on start up Default: Manual
Caution:
Use with care!
Control Input Source
Select from Universal Input 1 or Differential Input (only applicable if Input2 card
fitted and set to non temperature
Primary Control Action**
Reverse or Direct acting
Primary/Secondary**
proportional band
Integral Time
Enter Value of required integral time from Off to 99mins 59secs
Derivative Time**
Enter Value of required derivative time from Off to 99mins 59secs
Manual Reset/Bias**
Enter Value of required bias to apply to Proportional band from -100 to 100%
Default: 25%
Differential for On-Off Control** Enter Value of required ON-Off differential (a band centred about Setpoint to stop
excessive on-off switch when output control is set to be on-off) 0-300 units of span
Prop band Overlap and Deadband**
Enter value of required Overlap (+ive) or Deadband (-ive) of primary and seconday
control ouputs. -20to +20% of Span (Overlap both output on at same time dead
band both output never on at the same time).
Scaled Power
Enables or Disables Display of Manual Power in RPM
Scaled Power lower and Upper
Limit Enter value to be displayed at 0% power and 100% power (must be a minimum
of 100 units between upper and lower value)
Set point Upper and Lower
Limits Enter values to limit the maximum or minimum allowable Set point values
Local Set point value
Enter Value of required Local Set point (Constrained by input range and set point
upper and lower limits)
Manual to Auto Power transfer
Select from Bumpless or Set point Mode
Pressure Tune Output Pulse
Enter Value of maximum output pulse to be applied in Pressure tuning mode.
Pressure standby Threshold
Enter Value of required threshold that activates Standby by recover period from OFF
resistor Percentage
Enter Value of required Proportional band ( up to 100 time input span, maximum of
999900 in pressure control, ON-OFF to 9999 in temperature control)