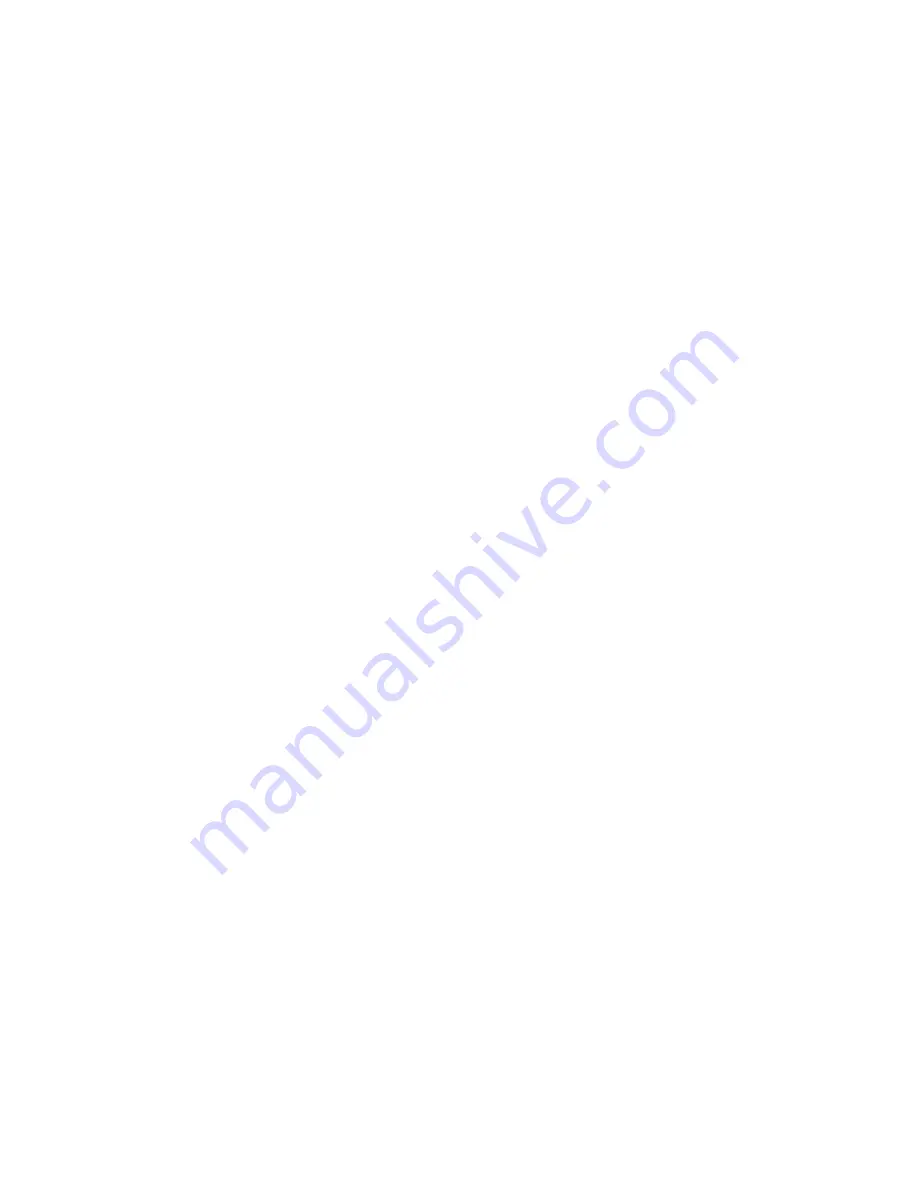
B 5
Conveyors (Material transfer):
The paver is equipped with two conveyors driven sepa-
rately with pressure from a single pump. The system consists of a single, pressure compen-
sated, load sense style, variable displacement, open loop pump driving two fixed volume
hydraulic motors. This pump supplies hydraulic power for both conveyors of the machine and
provides power for the cylinders on the machine.
These conveyors transfer the material from the hopper to the augers. By using sensors to
monitor the filling height during the paving proceedure, the transfer amount or speed regula-
tion is completely automatic.
Augers:
The augers are driven and controlled independently from the conveyors.
The auger hydraulics consist of two high pressure, variable displacement, closed loop
pumps driving two fixed volume motors. The left-hand and the right-hand half of the
auger can be controlled separately.
The conveying direction can be changed towards the center or the outside ensuring
that there is always a sufficient supply of material even if an excessive amount of ma-
terial is required at one side. The auger speed is controlled by sensors that monitor
the material flow leaving the conveyor.
Height adjustment and extension of augers:
Height adjustment and extension of
augers ensure an optimum variety of a wide range of paving thicknesses and widths.
Auger height is regulated at the operating panel and moved by means of hydraulic
cylinders.
Auger segments of different lengths can be attached to easily adapt to the different
paving widths.
Levelling/slope control system (option):
The slope control system allows the pav-
ing thickness to be regulated at the left-hand or the right-hand side with a defined dif-
ference to the opposite side.
To determine the actual value, the two screed lifting arms are linked with a slope con-
trol rod.
The slope control system always operates in conjunction with the screed height ad-
justment of the opposite side.
By adjusting the height of the screed lifing arms, the paving thickness of the material
or the laying height of the screed can be controlled.
Activation occurs electro-hydraulically on both sides and can be controlled manually
by means of toggle switches or automatically by means of an electronic grade control
system.
Screed lifting arms:
The screed lifting arms are used to lift the screed during trans-
portation. Lifting occurs electro-hydraulically on both sides by actuating the hydraulic
cylinders on the screed lifting arms and is controlled by means of toggle switches on
the operating panel.
Truck hitch (option):
The truck hitch holds the transport vehicle for paving material
in contact with the paver. They are located on the front of the hopper.
Summary of Contents for F1000W T4f
Page 2: ...www G QDSDF com...
Page 18: ...V 10...
Page 20: ......
Page 39: ...B 19...
Page 43: ...4 Transport on Low Bed Trailers 7 4 1 10 12 8 2 9 5 11...
Page 48: ...9 Transport Preparation 7 4 1 10 12 8 2 9 5 11...
Page 50: ...11 3 2 Driving mode 3 1 2...
Page 67: ...D 1 1 12 PANEL C 46 45 47 48 43 44 41 42 40 49...
Page 69: ...D 1 1 14 PANEL C 46 45 47 48 43 44 41 42 40 49...
Page 71: ...D 1 1 16 PANEL C 46 45 47 48 43 44 41 42 40 49...
Page 73: ...D 1 1 18 PANEL D 53 54 55 51 50 52 53 52 51 50...
Page 75: ...D 1 1 20 PANEL D 53 54 55 51 50 52 53 52 51 50...
Page 77: ...D 1 1 22 PANEL D 53 54 55 51 50 52 53 52 51 50...
Page 79: ...D 1 1 24 PANEL E 59 56 57 58...
Page 81: ...D 1 1 26 PANEL E 59 56 57 58...
Page 83: ...D 1 1 28 3 Auxiliary functions 61 63 62...
Page 96: ...D 1 1 41 Left right handset 100 102 104 106 101 103 105 107...
Page 98: ...D 1 1 43 100 102 104 106 101 103 105 107...
Page 117: ...D2 0 18 1 2 Engine Error messages...
Page 118: ...D2 0 19...
Page 119: ...D2 0 20...
Page 120: ...D2 0 21...
Page 121: ...D2 0 22...
Page 122: ...D2 0 23...
Page 123: ...D2 0 24...
Page 124: ...D2 0 25...
Page 125: ...D2 0 26...
Page 126: ...D2 0 27...
Page 127: ...D2 0 28...
Page 128: ...D2 0 29...
Page 129: ...D2 0 30...
Page 130: ...D2 0 31...
Page 131: ...D2 0 32...
Page 132: ...D2 0 33...
Page 133: ...D2 0 34...
Page 134: ...D2 0 35...
Page 135: ...D2 0 36...
Page 136: ...D2 0 37...
Page 137: ...D2 0 38...
Page 138: ...D2 0 39...
Page 139: ...D2 0 40...
Page 140: ...D2 0 41...
Page 141: ...D2 0 42...
Page 142: ...D2 0 43...
Page 143: ...D2 0 44...
Page 144: ...D2 0 45...
Page 145: ...D2 0 46...
Page 146: ...D2 0 47...
Page 147: ...D2 0 48...
Page 148: ...D2 0 49...
Page 149: ...D2 0 50...
Page 150: ...D2 0 51...
Page 151: ...D2 0 52...
Page 152: ...D2 0 53...
Page 153: ...D2 0 54...
Page 154: ...D2 0 55...
Page 155: ...D2 0 56...
Page 156: ...D2 0 57...
Page 157: ...D2 0 58...
Page 169: ...D 4 0 4 40 40 20 21 12 20 21 10 12...
Page 171: ...D 4 0 6 40 40 20 21 12 20 21 10 12...
Page 173: ...D 4 0 8 40 40 20 21 12 20 21 10 12...
Page 175: ...D 4 0 10 40 40 20 21 12 20 21 10 12 47 48 52 54 55 47 48 52...
Page 178: ...D 4 0 13 46 20 21 15 45 20 21 15 46 45...
Page 180: ...D 4 0 15 46 20 21 12 45 20 21 12 46 45 53 24 27 53...
Page 183: ...D 4 0 18 20 21 12 45 20 21 12 45 28 27 10 25...
Page 185: ...D 4 0 20 20 21 12 45 20 21 12 45 28 27 10 25 48 47 54 52 50 51 55 48 47 52 50 51...
Page 201: ...E 01 10 4 6 Auger Chart...
Page 203: ...F 1 0 2...
Page 204: ...1 F 2 1 Maintenance Overview 1 Maintenance overview 7 1 9 0 10 0 3 0 5 0 8 1 6 0 4...
Page 214: ...F 4 0 1 F 4 0 Maintenance Auger 1 Maintenance Auger sub unit I 1 2 3 4 5...
Page 235: ...F 5 0 16...
Page 247: ...F 6 0 12...
Page 248: ...1 F 7 1 Maintenance Travel Drive Steering 1 Maintenance travel drive steering 4 2 1 3...
Page 256: ...1 F 8 1 Maintenance Electronic System 1 Maintenance Electronic system 1 3...
Page 263: ...8...
Page 267: ......
Page 268: ...F10 0 1 F10 0 Checks Decommissioning 1 Tests check up cleaning stopping...