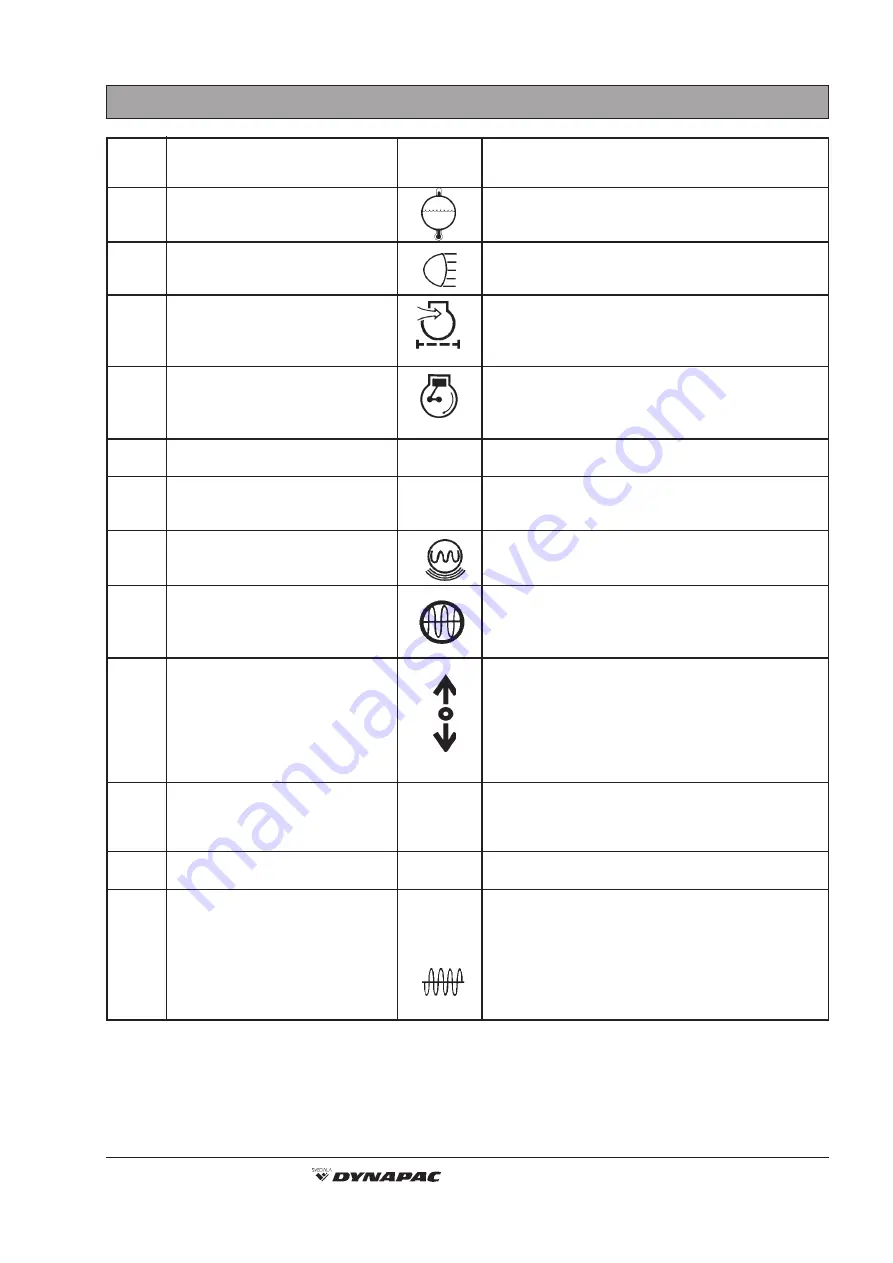
9
CC 501/501C O501EN3
INSTRUMENTS AND CONTROLS, FUNCTIONAL DESCRIPTION, cont’d.
Items
Designation
Symbol
Function
in fig. 4
16
Temperature gauge, coolant
Indicates engine working temperature. Normal
temperature range 82°C–95°C (180°F–203°F)
17
Main/dipped beam, contact/
Turn right for main beam, knob lights.
control lamp (optional)
Turn left for dipped beam, knob light goes out.
18
Warning lamp, air filter
If the warning lamp lights while the engine is
running, the air cleaner needs cleaning or
replacement.
19
Tachometer/Hourmeter
Indicates current engine speed in revs per
minute. Multiply the meter value by 100.
The running time in hours is indicated digitally.
20
Compaction meter (optional)
-
-
21
Speedometer
Indicates roller speed in km/h.
(optional equipment for CC 501)
22
Vibration/Frequency meter
Indicates current frequency of the drum.
(optional equipment for CC 501)
Contact (31) in correct position.
23
Vibration ON/OFF
Press to switch vibration on.
Press again to switch vibration off.
Applies when (27) is in the MAN mode.
24
Forward/Reverse lever
Move the lever to the desired direction of
(F/R lever)
travel. Driving speed is proportional to the
movement of the lever. The roller is braked
via the hydrostatic transmission as you move
the lever toward neutral. The engine can only
be started with the lever in neutral.
25
Speed control
Limits movement of the F/R lever and thus
(optional equipment for CC 501)
the speed. The speed control can be
bypassed.
26
-
-
-
27
Vibration switch
MAN
In MAN mode, the vibration is switched ON/
MAN/AUT.
O
OFF with (23).
AUT
Vibration is OFF in the O mode.
The AUT mode gives automatic switching of
vibration ON/OFF when driving forward or
reverse.
Summary of Contents for CC 501
Page 2: ......