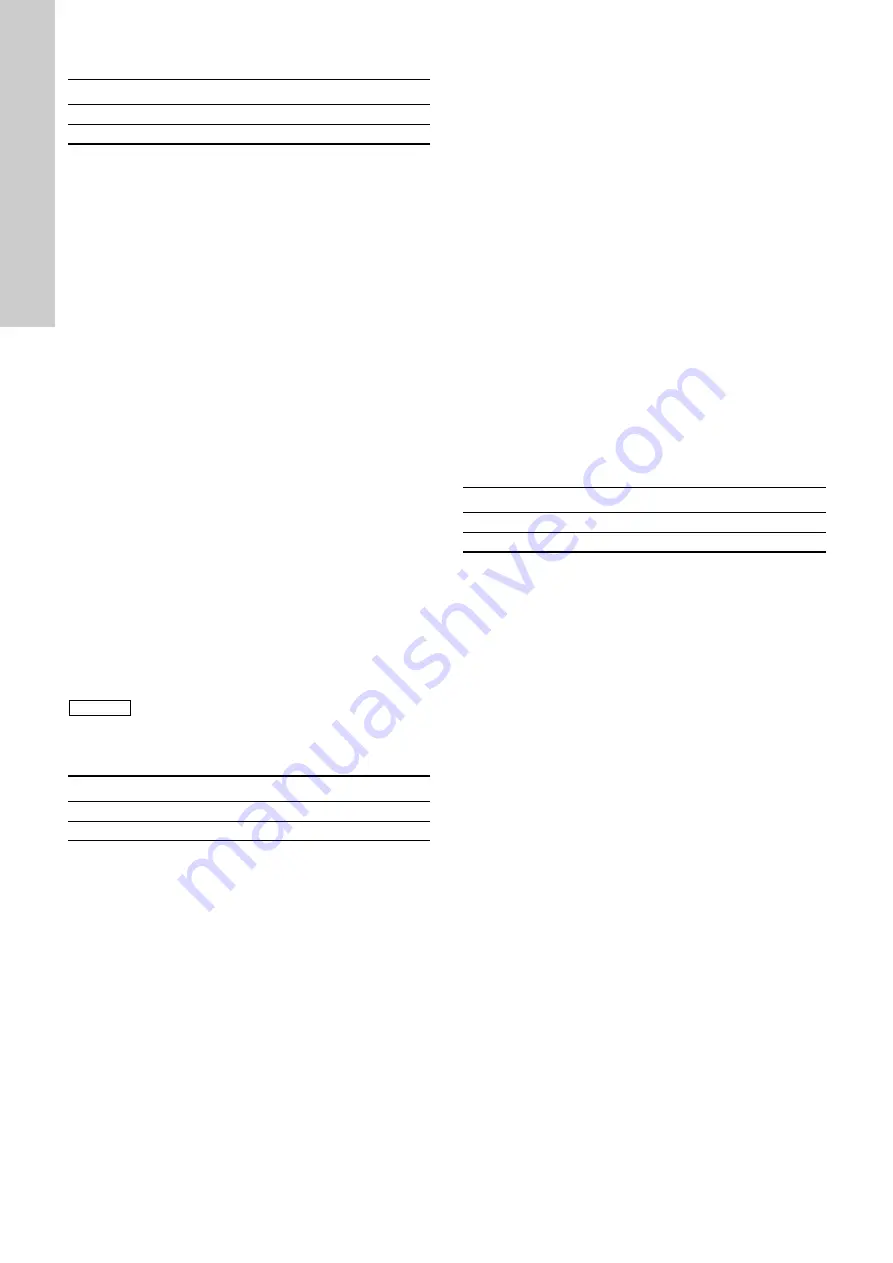
English (GB)
30
7.36 Connection code
This menu is only available in Grundfos GO.
You can setup a connection code to avoid having to press the
connection button each time and to restrict remote access to the
product.
Setting the code in the product using Grundfos GO
1. Connect Grundfos GO to the product.
2. In the product dashboard, select "Settings".
3. Choose "Connection code".
4. Enter the wanted code and press [OK].
The code must be a character string (ASCII).
You can always modify the code. The old code is not needed.
Setting the code in Grundfos GO
You can define a default connection code in Grundfos GO so that
it automatically attempts to connect to the selected product via
this code.
When you select a product with the same connection code in
Grundfos GO, Grundfos GO automatically connects to the
product and you do not have to press the connection button on
the module.
Define the default code in Grundfos GO in this way:
1. In the main menu, under "General", select "Settings".
2. Choose "Remote".
3. Enter the connection code in the field "Preset connection
code". The field now says "Connection code set".
You can always modify the default connection code by pressing
[Delete] and entering a new one.
If Grundfos GO fails to connect and ask you to press the
connection button on the product, it means that the product has
no connection code or has a different connection code. In this
case, you can only establish connection via the connection
button.
7.37 Run start-up guide
This menu is only available in the advanced control panel.
The startup guide automatically starts when you start the pump
for the first time.
You can always run the startup guide later via this menu.
The startup guide will guide you through the general settings of
the pump.
• Language. See section
.
• Select date format.*
See section
7.27 Date and time (Set date and time)
• Set date.*
See section
7.27 Date and time (Set date and time)
• Select time format.*
See section
7.27 Date and time (Set date and time)
• Set time.*
See section
7.27 Date and time (Set date and time)
• Setting of pump
– Go to Home
– Run with Constant curve/Run with Constant pressure.
(See section
.
– Go to "Assisted pump setup".
See section
– Return to factory settings.
* Applies only for pumps fitted with advanced functional module
(FM 300). For further information, see section
13. Identification of functional module
7.38 Alarm log
This menu contains a list of logged alarms from the product. The
log shows the name of the alarm, when the alarm occurred and
when it was reset.
7.39 Warning log
This menu contains a list of logged warnings from the product.
The log shows the name of the warning, when the warning
occurred and when it was reset.
7.40 Assist
The menu consist of a number of different assist functions which
are small guides that will take you through the steps needed to
set up the pump.
7.41 Assisted pump setup
The menu guides you through the following:
Setting of pump
• Selection of control mode. See page
.
• Configuration of feedback sensors.
• Adjusting the setpoint. See page
• Controller settings. See page
.
• Summary of settings.
Example of how to use the "Assisted pump setup" for setting
up the pump to constant pressure:
Grundfos GO
1. Open the "Assist" menu.
2. Select "Assisted pump setup".
3. Select control mode "Constant pressure" (Const. pressure).
4. Read the description for this control mode.
5. Select which analog input to use as sensor input.
6. Select sensor function according to where the sensor is
installed in the system. See fig.
on page
7. Select electrical input signal according to the sensor
specifications.
8. Select measuring unit according to the sensor specifications.
9. Set the minimum and maximum sensor range values
according to the sensor specifications.
10. Set the desired setpoint.
11. Set the controller settings K
p
and T
i
. See the
recommendations in section
.
12. Type the desired pump name.
13. Check the summary of settings and confirm them.
Pump variant
Connection code
CME
●
CRE, CRIE, CRNE, SPKE, MTRE
●
Note
After setting a connection code, you must switch
off the product until the light in Grundfos Eye
turns off before you can use the new connection
code.
Pump variant
Run start-up guide
CME
●
CRE, CRIE, CRNE, SPKE, MTRE
●
Pump variant
Assisted pump setup
CME
●
CRE, CRIE, CRNE, SPKE, MTRE
●
Summary of Contents for VT Booster Set
Page 1: ...VT Booster Set O M Manual...
Page 3: ...1 Important Health Safety Information Page 3 VT Booster Set...
Page 10: ...2 System Information Installation and Commissioning Page 10 VT Booster Set...
Page 11: ...2 1 Booster Set Components VT Booster Set Components Page 11 VT Booster Set...
Page 12: ...2 2 Control Panel Wiring Diagrams Twin Pump Wiring Diagram Single Phase Page 12 VT Booster Set...
Page 13: ...Twin Pump Wiring Diagram 3 Phase Page 13 VT Booster Set...
Page 15: ...VR VASCO Cold Water Booster Sets Page 15 VT Booster Set...
Page 16: ...VT3 Three Phase Control Panel Wiring Diagram Page 16 VT Booster Set...
Page 17: ...Page 16a VT Booster Set...
Page 23: ...3 User Maintenance and Troubleshooting Page 22 VT Booster Set...
Page 43: ...Appendix 14...
Page 50: ...Appendix 21...
Page 51: ...Appendix 22...
Page 55: ...Appendix 26...
Page 56: ...Appendix 27...