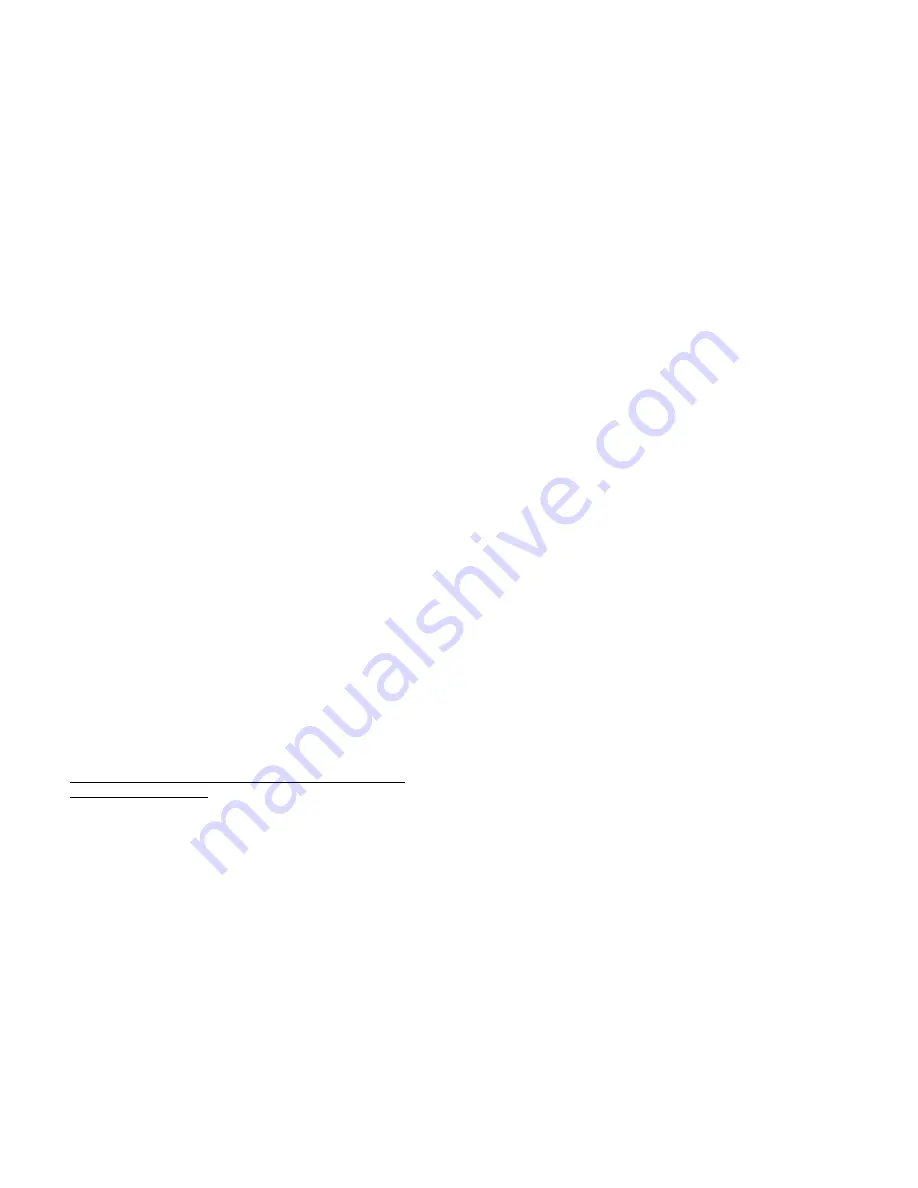
ELECTRICAL CONNECTIONS
All units are wired as completely as possible at the factory
prior to delivery. The connections which must be made by
the installer are to the main power source, control power
source, separate chiller heater power source and
interlocking the satellite equipment. In connecting power
wiring to the unit, the following precautions should be taken:
!
All field wiring is to be in accordance with the National
Electrical Code and state and local codes.
!
All wiring is to be checked for damage and all terminal
connections tested for tightness. Unit terminal blocks are
to be connected with copper conductors only, sized per
ampacity listed on unit data plate.
!
The power supply should match the unit nameplate in
volts, phase and Hertz. Voltage must be within ± 10% of
nameplate value and voltage imbalance between phases
must not exceed 2%.
!
For minimum circuit ampacity and maximum fuse size,
see Unit Nameplate.
Two separate 115 volt power sources must be field supplied
to provide power for control and heater circuits. If optional
control circuit transformer is provided, only one separate 15
Amp, 115V power source is required for chiller heater circuit.
All electrical connections should be periodically tightened.
Refer to the unit nameplate data for the minimum circuit
ampacity and maximum allowable dual element fuse size.
The factory supplied field power block is sized to accept
wires sized per NEC, 75C (3-in-conduit) up to 500MCM as
required. When multiple wires per pole are required to stay
at or below 500MCM, the power block supplied will have
multiple wire per pole capability.
A separate 15 amp 115V field power supply is required to
power the main control circuit (which includes the
compressor sump heaters) unless the control transformer
option is included.
OPERATION - ACDX
GENERAL
work involved, and also to be trained in the operation and
The unit should be started up only by a refrigeration
technician who is familiar with accepted operation practices
The representative will inspect the installation to
for refrigeration systems.
determine whether it meets Dunham-Bush, Inc.
Use small screw unit start-up report, Form NS1157 to record
installation, determine whether it is in satisfactory
all temperature, pressure, electrical readings and control
operating condition, and instruct specified customer
settings. A copy must be forwarded to Dunham-Bush, Inc.,
personnel in its operation and maintenance for the length
North American Service, Harrisonburg, Virginia before the
of time specified in the purchase contract.
warranty will be honored.
AIR COOLED PACKAGE CHILLER START-UP - ACDX
of 24 hours and the oil sump temperature must be at a
The unit is ready for start-up when the following procedures
representative. This will ensure that the oil is warm
have been completed.
enough to vaporize any dissolved refrigerant and that the
1. Water piping for the cooler is installed and tested.
2. Electrical connections are made and properly fused.
2. Before starting the compressor(s), check all three phases
3. Unit has been leak tested, leaks corrected, and charge
of supply voltage, of all legs of the motor. They must be
completed.
within ± 10% of the nameplate voltage. Check to be sure
4. Compressor crankcase heater(s) has been energized for
compressor is not running backwards.
a minimum of 24 hours.
5. Calibrated refrigerant gages have been connected to the
3. Start compressor(s), check the gages and note if the
suction and discharge.
pressures are within the prescribed limits.
6. Turn on the chilled water pump, check direction of
rotation and adjust the water flow through the cooler to
4. Check the refrigerant sight glass at the TX Valve to be
the specified flow rate. Bleed off all entrained air.
sure it is free of bubbles. If not, charge as required to
7. Manually energize the fan starters and check the fan
clean sight glass. .
rotation. Fans should pull air through the condenser coil
and discharge vertically upwards.
5. Stage unit down until all compressors are off and check
8. Check all refrigerant valves to be sure they are open.
the compressor crankcase sight glass for oil level. It
9. Proceed to System Start-up.
should be 1/2 to 3/4 of the compressor sight glass. If not,
SYSTEM START UP
1. Request for Start-Up Representative - Start-up service is
expansion valve superheat setting should be checked, it
an option for these units and is requested when the unit
should be between 9
E
and 12
E
F at full load design
is ordered. If you purchased start-up service, then after
conditions. In some instances, it will be necessary to
the installation has been completed and checked, Form
lower the superheat setting to ensure proper distribution.
9180 must be filled out and sent to the local Dunham-
Turn the TX valve adjustment stem clockwise to increase
Bush representative who sold the unit. Following receipt
the superheat setting and counterclockwise to decrease
of this signed form, a representative will be sent to the
the setting. Be sure and allow ample time between each
customer. The purchaser should have competent service
adjustment for the system to rebalance.
and operating personnel in attendance to assist in the
maintenance of this unit.
requirements, perform the initial start-up of the
NOTE: Sump oil heaters should be energized a minimum
minimum of 100
E
F (38
E
C) prior to arrival of start-up
oil is within the normal operating temperature range.
see procedure for adding oil on page 7.
6. Restart the compressor. After an hour of operation, the
6
Summary of Contents for ACDX
Page 25: ...TYPICAL POWER WIRING ACDX120A...
Page 26: ...TYPICAL CONTROL WIRING ACDX120A...
Page 27: ...TYPICAL OPTIONS WIRING ACDX120A...
Page 28: ...TYPICAL CONTROL WIRING ACDX120B W MICRO...
Page 29: ...TYPICAL CONTROL WIRING ACDX120B W MICRO...
Page 30: ...TYPICAL OPTIONS WIRING ACDX120B W MICRO...
Page 33: ......
Page 34: ...ACDX AUDX CONDENSER CLEARANCE...
Page 35: ......
Page 36: ...ACDX LOAD POINTS...
Page 37: ...ACDX RUBBER IN SHEAR ISOLATOR...
Page 38: ...ACDX SPRING ISOLATOR...
Page 39: ...AUDX LOAD POINTS...
Page 40: ...AUDX RUBBER IN SHEAR ISOLATOR...
Page 41: ...AUDX SPRING ISOLATOR...