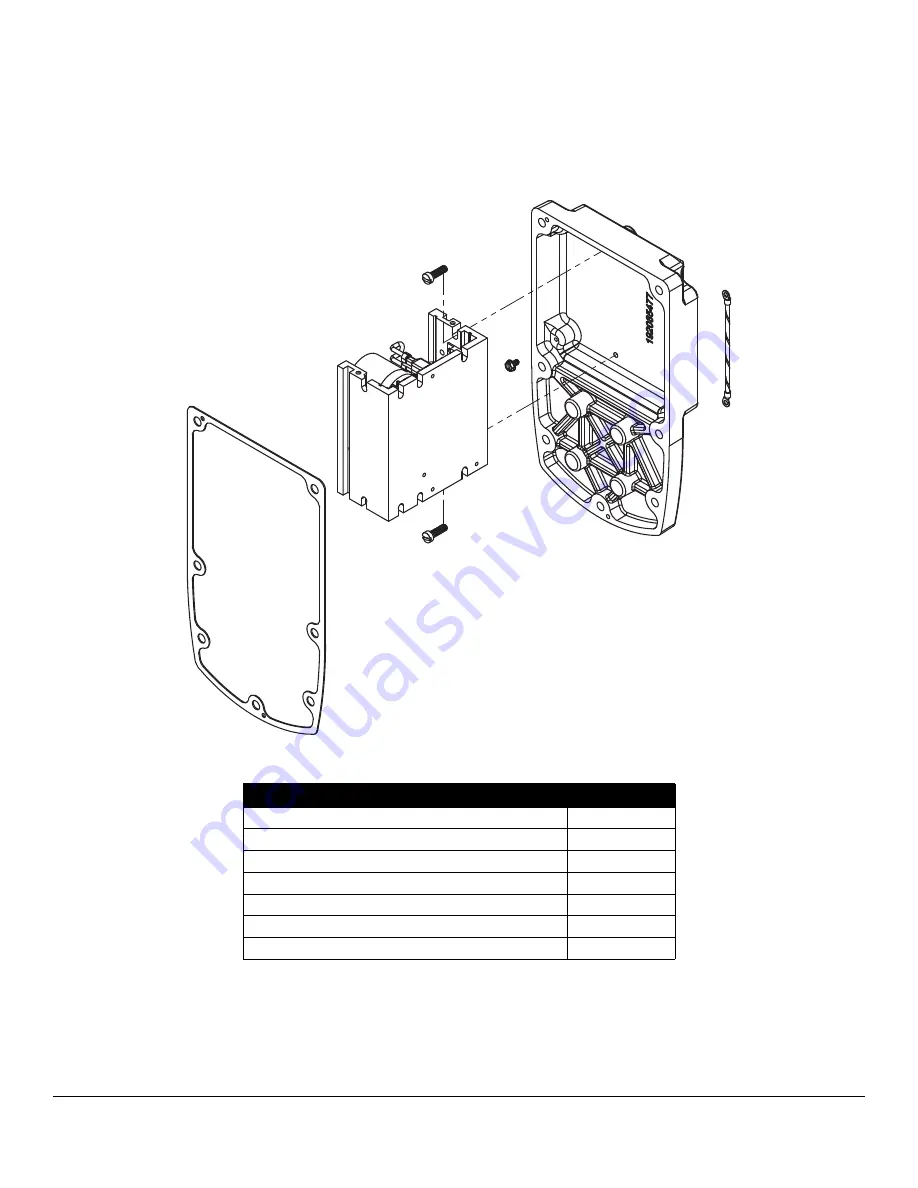
SPA Actuator with Intelli-Motion™ Technology Manual R00
May 2022
Page 41 of 48
5.4.3.3 Variable Frequency Drive (VFD) Parts Kit
Description
Qty
Cover Cap
1
Thermally Conductive Paste
1
VFD, KB Model KBVF-23D (MOD)
1
Screw, #10-24 x 0.625
2
Gasket, Cap Cover
1
Gnd Jumper Wire - Tether Short
1
#6-32 x 0.25 Grounding Screw
1
VFD Parts Kit
P/N: 192090515