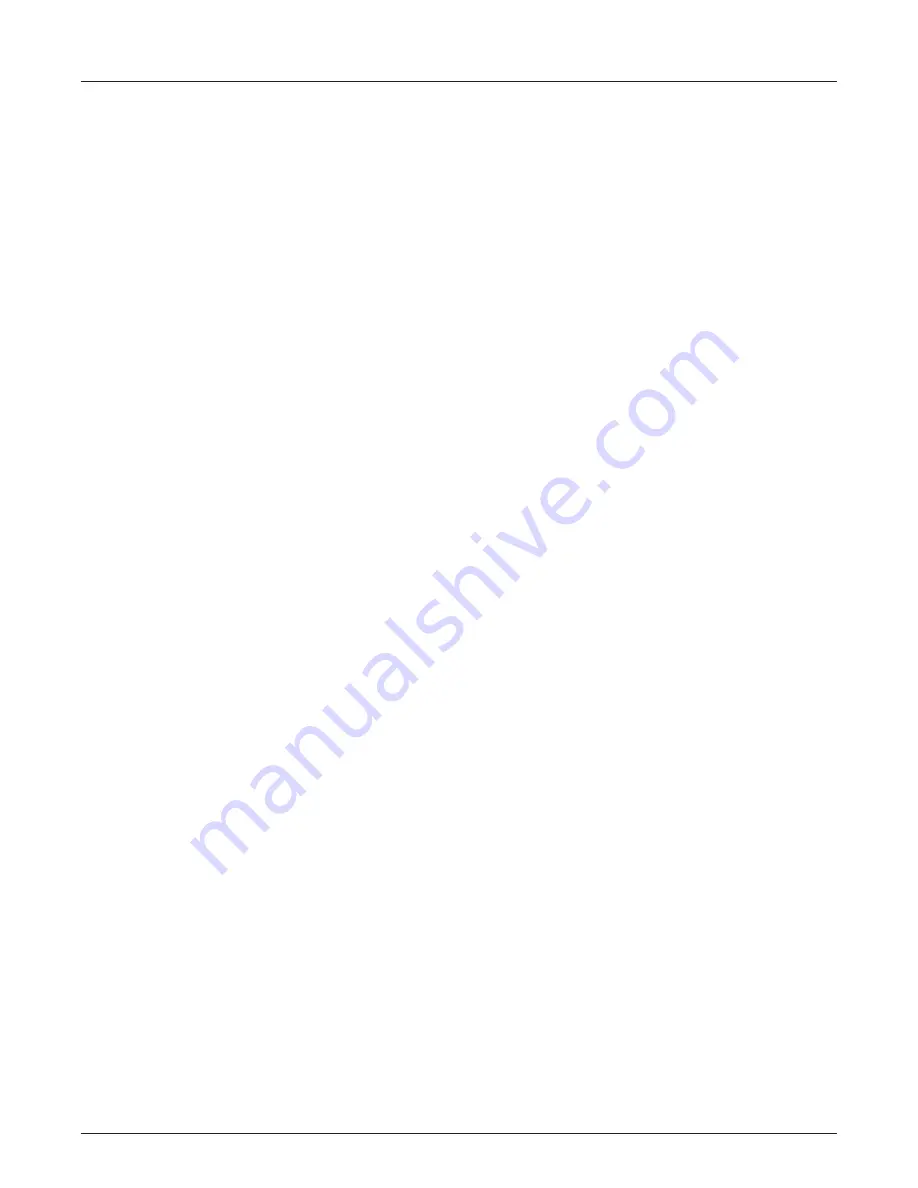
IonPac NS1 Manual
Document No. 034024-06
Page 28 of 35
5.2.2 Contaminated Anion Trap Column, the ATC-3 (4-mm)
When doing gradient analysis, ensure that the Anion Trap Column, the ATC-3 (2-mm) or the ATC-3 (4-mm) has been
installed correctly.
If it has not, install one as directed in Section 2.3, “The Anion Trap Column,” and watch the background
conductivity. If the background conductivity is now low, this means that the ATC is trapping contaminants from the eluent. The
eluents probably have too many impurities (see items A–C above).
Determine if the ATC is the source of high background conductivity.
Remove the ATC. If the background conductivity remains
high, then the ATC is not the problem. If the background conductivity decreases, the ATC is the source of the high background
conductivity.
A. Disconnect either the ATC-3
(4-mm) from the injection valve and direct the outlet to waste.
B. Flush the ATC with 200 mL of 35 mM NaOH or the highest NaOH concentration used in the application.
Use
a flow rate of 2.0 mL/min on a 4-mm system.
C. Equilibrate the ATC with the strongest eluent used during the gradient run.
Use a flow rate of 2.0 mL/min on a
4-mm system.
D. If the problem persists, replace the ATC.
5.2.3 Contaminated Guard or Analytical Column
Remove the IonPac NG1 Guard and IonPac NS1 analytical columns from the system. If the background conductivity decreases,
then one (or both) of these columns is (or are) the cause of the high background conductivity, clean the column as instructed in
Appendix B - Column Care.
5.2.4 Contaminated Hardware
To eliminate the hardware as the source of the high background conductivity, bypass the SRS suppressor and pump deionized water
with a specific resistance of 18.2 megohm-cm through the system. The background conductivity should be less than 2 µS. If it is
not, check the detector/conductivity cell calibration by injecting deionized water directly into it. See the appropriate manual for
details.
5.2.5 Contaminated Suppressor
Assume that the SRS or the AMMS-ICE is causing the problem if the above items have been checked and the problem
persists.
A. Check the regenerant flow rate
at the
REGEN OUT
port of the SRS or the AMMS-ICE. For the example isocratic
applications, this flow rate should be 3–5 mL/min in the Chemical Suppression Mode of operation.
B. Check the eluent flow rate.
For most applications, the eluent flow rate for 2-mm applications should be 0.50 mL/min
and for 4-mm applications, it should be 2.0 mL/min. Refer to the Self-Regenerating Suppressor Product Manual
(Document No. 031956) or the Anion-II MicroMembrane Suppressor-ICE Product Manual (Document No. 032661)
to ensure that the eluent is within suppressible limits.
C. Test both the suppressor and the Anion AutoRegen Regenerant Cartridge for contamination
if you are using an
AutoRegen Accessory with the ASRS ULTRA II (in the MPIC or Chemical Suppression Mode) or the CSRS (in the
Chemical Suppression Mode). Prepare fresh regenerant solution.
1. Clean or replace your SRS or AMMS-ICE if the background conductivity is high after preparing fresh
regenerant and bypassing the Anion AutoRegen Regenerant Cartridge.
Refer to the “Self-Regenerating
Suppressor Product Manual” (Document No. 031956) or the “Anion-ICE MicroMembrane Suppressor II Product
Manual” (Document No. 032661) for assistance.