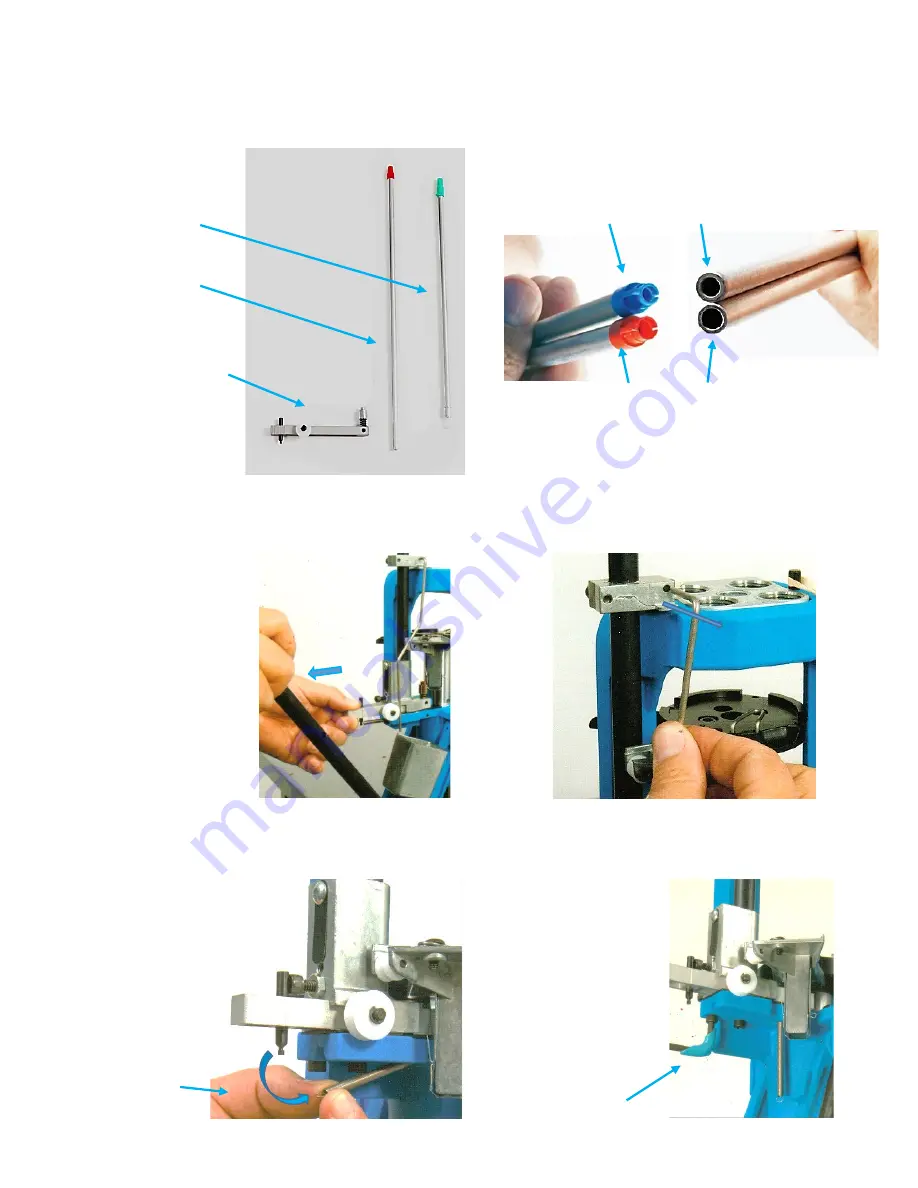
40
9.3
Primer Size Conversion
9.3.1
The RL550C comes configured for Small primers. The Large Primer Components are shipped separately.
9.3.2
The Magazine Tube Assembly uses color-coded plastic Primer Magazine Feed Tips. The Large Primer Magazine Tip
is red and Small Primer Magazine Tip is blue. The Small and Large Aluminum Magazine Tubes have different inside
diameters. A conversion Kit for the large primer system is included in the original shipment “Tube Pack.”
9.3.3
The Primer Size Conversion Kit included with the RL550C is shown below:
9.3.4
To change Primer Size, remove the Operating Rod by lowering the Operating Handle partway down, pull back on
the spring return Primer Slide, disengaging and removing the Operating Rod.
9.3.5
Unhook the Primer Slide Return Spring from the Prime Slide. Remove the two Primer Housing attachment Socket
Head Screws with a 5/32” Allen wrench.
Primer Size conversion Kit
•
Large Primer
Pickup Tube—
Green Tip
•
Large Primer
Magazine
Tube/Orifice
Tip—Red tip
•
Large Primer Slide
(Silver Cup)
Remove Spring and
let hang down
Remove the two
Primer Housing
attachment screws
Red Tip- Large Primer Magazine
Blue Tip--Small Primer Magazine
Summary of Contents for RL550C
Page 44: ...44 9 4 Powder Measure Conversion refer to the Exploded View below ...
Page 60: ...60 15 RL550C EXPLODED VIEWS AND PARTS IDENTIFIER 15 1 Complete Assembly Exploded View 1 ...
Page 61: ...61 15 2 Frame and Lower Assembly Exploded View 2 ...
Page 62: ...62 15 3 Toolhead Assembly Exploded View 3 ...
Page 63: ...63 15 4 Platform and Components Exploded View 4 ...
Page 64: ...64 15 5 Primer Feed Assembly PN 20263 no Operating Rod Exploded View 5 ...
Page 65: ...65 15 6 Powder Measure Assembly ...
Page 66: ...66 15 7 Primer Early Warning System PN20302 Rod and PEWS Kit PN14497 PEWS Alone ...
Page 75: ...75 18 RL550C TEMPLATE FOR DRILLING MOUNTING HOLES IN BENCH ...