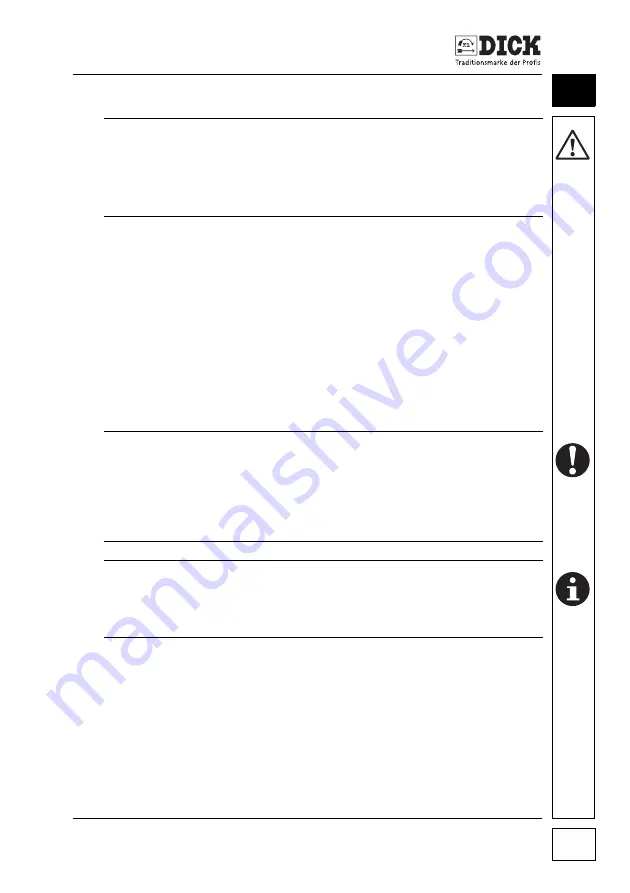
SM-200 TE Grinding and Honing Machine
57
Machining Workpieces
9
1
Position the knife on the wet grinding belt so that the knife
edge
points in the direction of rotation of the wet grinding
belt
.
2
Align the cutting edge of the knife horizontally so that it is posi-
tioned roughly perpendicular
to the grinding belt.
3
on the wet grinding belt at an angle
of approx. 15°
. Position the blade at approx. 20° with
a cleaver.
4
Grind the sides of the blade alternately when grinding until
a burr has formed over the entire surface.
WARNING
Risk of injury
The blade may cut into the grinding belt and be torn from the
hand.
• Never grind against the cutting edge.
NOTE
Workpieces heat during the grinding process
An over-heated cutting edge can anneal (loss of hardness) and
stress cracks can form on it.
• Always wet grind cutting tools.
NOTE
If the cutting edge has become thicker as a result of frequent grin-
ding, the cutting edge thickness can be reduced again by grinding
the flat sides.
Summary of Contents for SM-200 TE
Page 76: ......