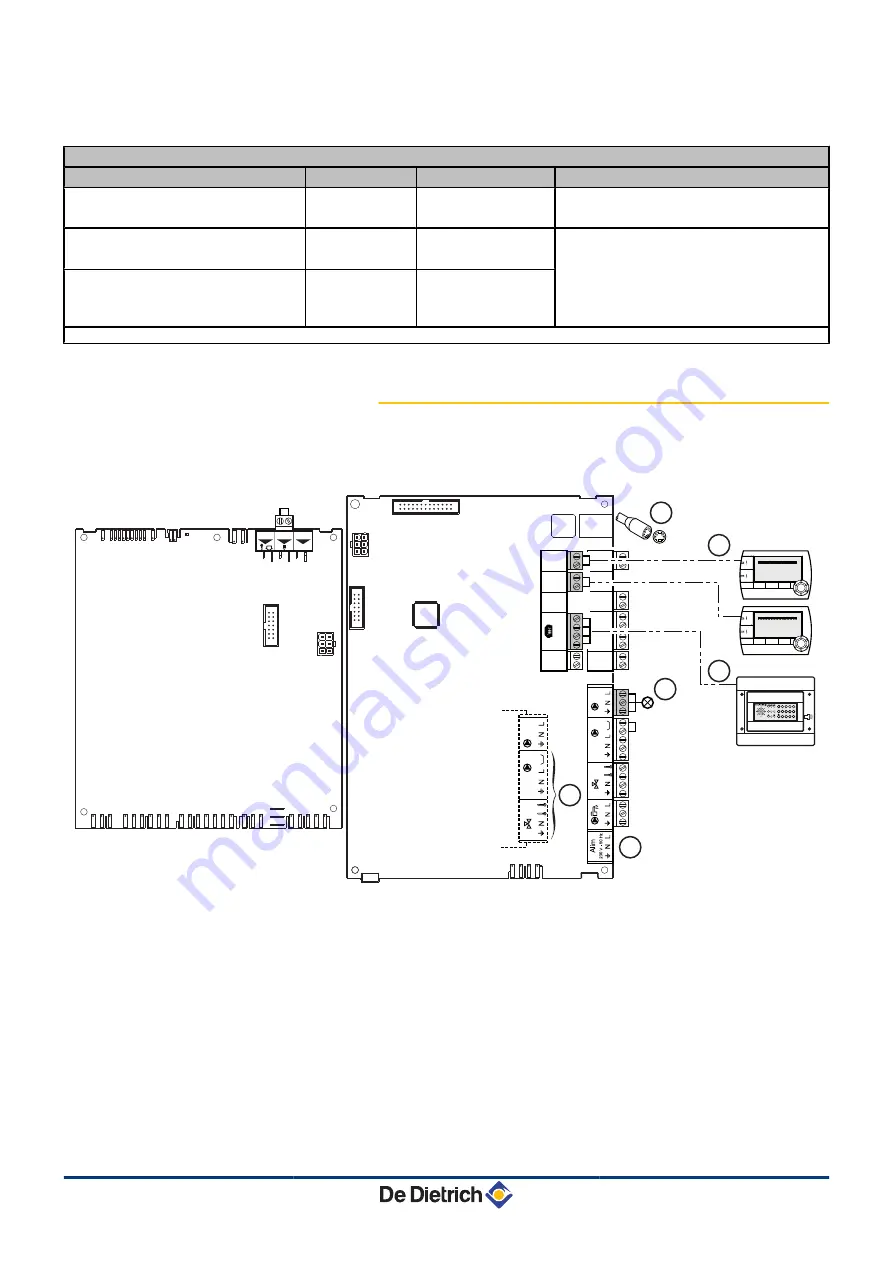
U
Connect the load pump.
Settings to be made for this type of installation
Parameters
Access
Settings to be made See chapter
INSTALLATION
Installer level
#SYSTEM
menu
EXTENDED
If the electric tank is connected to
M
A
:
CIRC.A
(1)
Installer level
#SYSTEM
menu
DHW ELEC
"Setting the parameters specific to the
If the electric tank is connected to
M
AUX
:
S.AUX
(1)
Installer level
#SYSTEM
menu
DHW ELEC
(1) The parameter is only displayed if
INSTALLATION
parameter is set to
EXTENDED
5.8.13.
Connecting the options
For example: TELCOM remote vocal monitoring module, remote
controls for circuits
A
and
B
, second DHW tank
On
/o
ff
OT
BL
SE
xt
PCU
SCU
T
S
+
C
A
U
X
C
C003151-D
T
S
+
B
A
B
0
-1
0
V
S
AMB
C
4
3
2
1
2
1
+
-
S
AM
B
B
2
1
S
AM
B
A
2
1
S
SYST
+
T
A
-
S
EC
S
S
EXT
S
D
EP
C
2
1
2
1
2
1
2
1
2
1
S
D
EP
B
2
1
MODE
r
x
0
2
4
6
8
10
12
14
16
18
22
24
20
c
MODE
r
x
0
2
4
6
8
10
12
14
16
18
22
24
20
c
V
PRG
TELCOM 2
ALP
AL2
AL1
3
2
1
SET
#
0
9
V
8
7
6
5
4
3
2
1
6
4
3
2
1
5
A
MODBUS cascade connection, VM
Z
Connect the remote control (Package AD254/FM52)).
E
Connect the TELCOM remote vocal monitoring module
(depending on its availability in your country).
R
Alarm indicator
T
Connect the load pump of the second tank.
Y
Do not connect anything to the terminal block.
AFC 18 - AFC 24 - AFC 30
5. Installation
09/07/2015 - 300026439-07
83