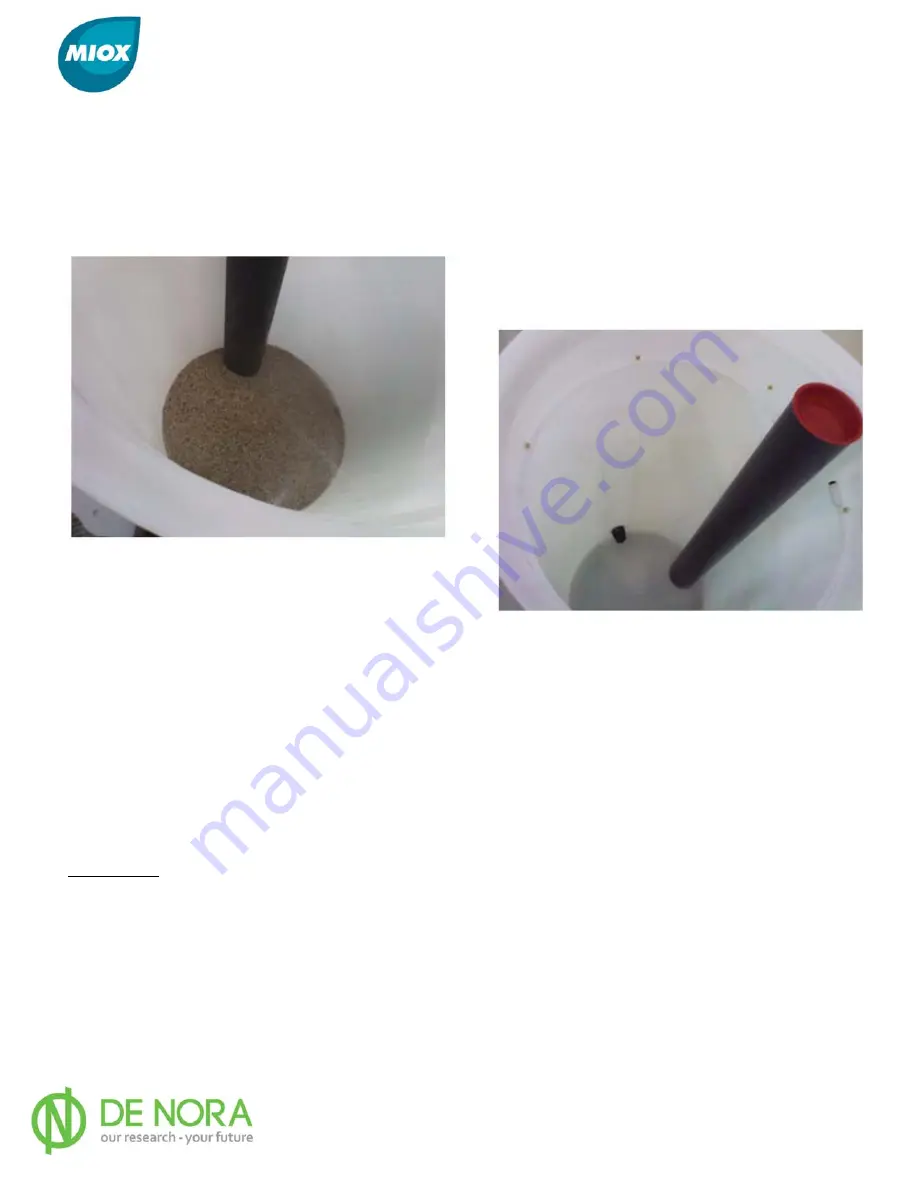
MIOX AE Series Operators Manual
102-00085-E
Page
21
The spray ring assembly provides a more consistent means of mixing the salt and water to meet the
brine saturation requirement. The spray ring at the top of the tank eliminates possibility of channeling
(or short circuiting) the water through the outlet of the tank. Adding a quartz rock bed at the bottom the
tank also reduces the possibility of brine channeling for any application. The following pictures provide
an illustration of the spray ring assembly installed in a quartz rock bed (right) and tank assembly
without quartz rock.
Figure 7 Internal View Float Valve Assembly and Detail
For instances where the float needs to be removed, turn off the water to the system. Remove the (red)
cap on top of the stillwell. Unscrew the 3/8” PVC coupler that mates to the feed water line and the black
threaded flange connection protruding through the tank wall. Unscrew the coupler that mates to the
plastic spray ring. The float valve can now be pulled out the stillwell. The float itself, can be unscrewed
at the clevis hinge that mates with the open/close poppet valve. To re-install the valve assembly, repeat
step in reverse order, making sure to use Teflon tape for replacing all NPT connections. Replace red cap
and return water supply. Verify float does close once high level is reached and system is not flowing
water.
Quartz Rock
In order to accommodate various salt types, MIOX provides a cross-shaped, slotted pipe manifold.
Thread the manifold into the bottom tank adapter. Place 7 inches of ½” x ¼” NSF quartz rock in the
bottom of the tank. Rake it flat and cover the slotted pipe manifold. Place 5 inches of ¼” x
⅛
” NSF
quartz rock on top of the first layer of quartz rock. Rake flat.