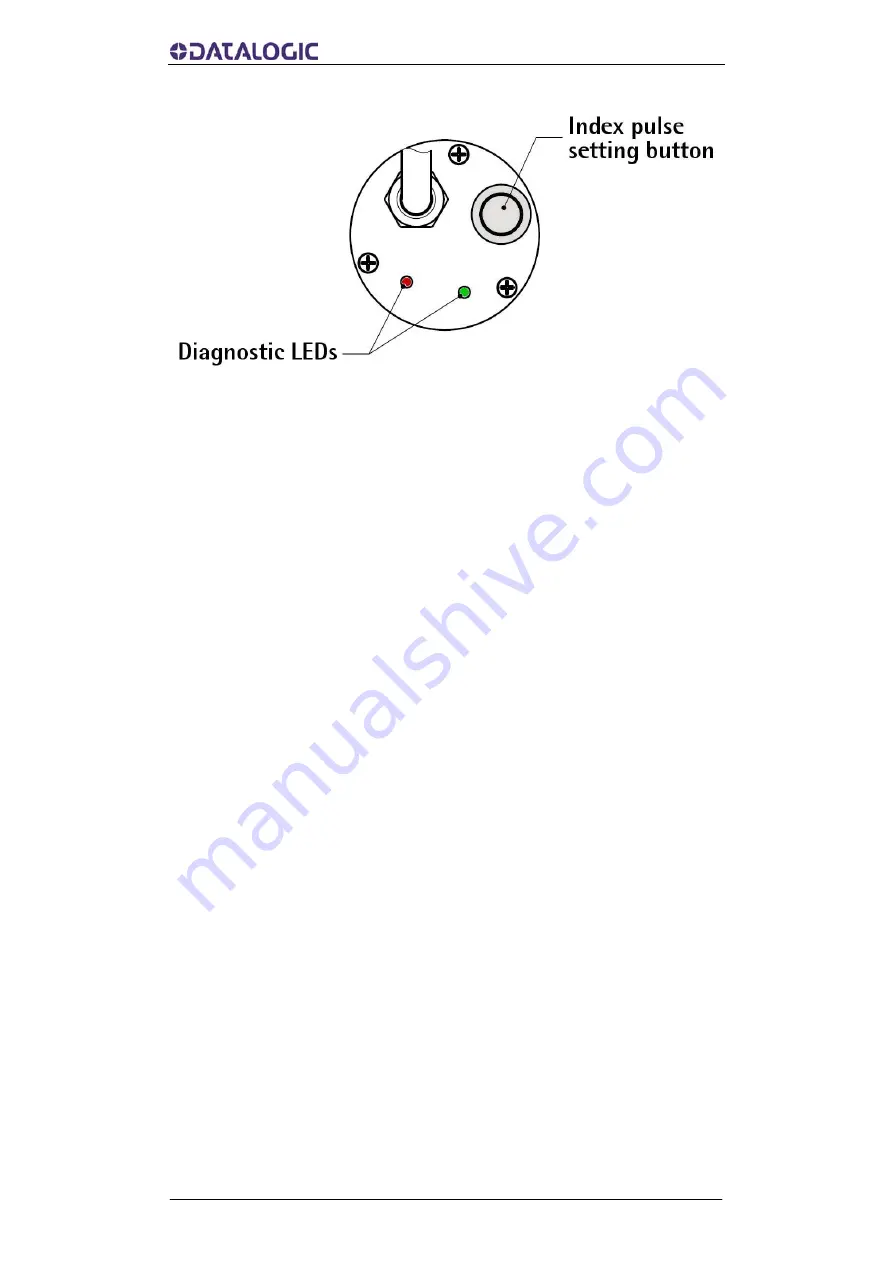
ENC58 PROG
13
Figure 1 - Diagnostic LEDs and Index pulse setting button
4.12 I
2
C (Inter Integrated Circuit) serial connection
The ENC58 programmable encoder is equipped with a serial
interface for the parametrization and set-up of the device.
The serial interface is a I2C (Inter Integrated Circuit) type interface.
To communicate with the encoder, you must connect the device to
the personal computer through a USB port using the specific
connection cable supplied by Datalogic Automation upon request.
The connection cable code is KIT ENC58.
It is provided with a M23 12-pin female connector for the devices
having ZCZ output circuit code; a M12 12-pin female connector for
the devices having ZCM output circuit code; and a terminal for
connecting the cable of the devices having ZCU output circuit code.
Summary of Contents for ENC-58 PROG
Page 1: ......
Page 10: ...ENC58 PROG 5 3 1 3 Installation using a flange code ST 58 FLNG ...
Page 38: ...www datalogic com ...