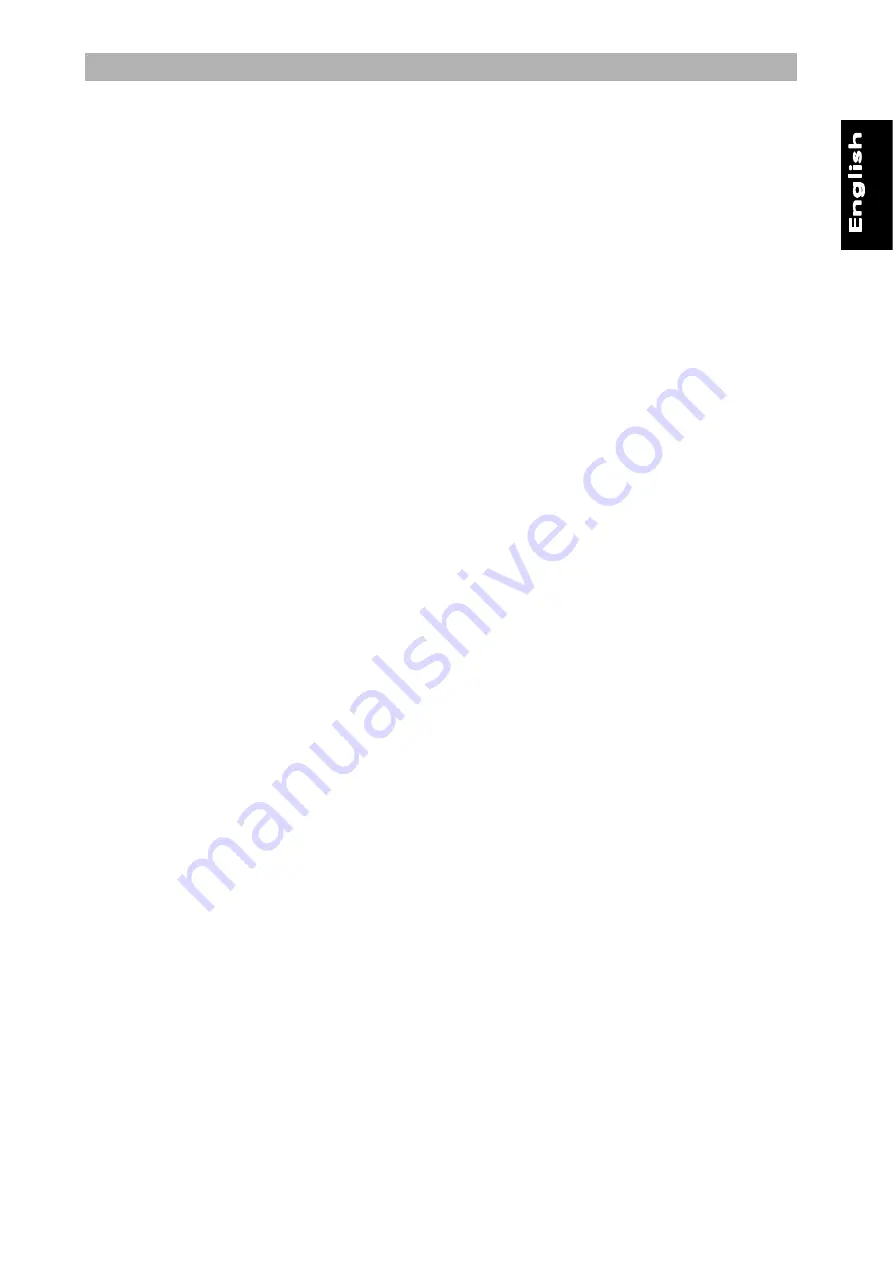
DataVS1
Series
Instruction
Manual
INDEX
GENERAL INFORMATION ............................................................................................................................................................... 1
Conventions used in the manual ........................................................................................................................................... 1
General description ............................................................................................................................................................... 1
Available models ................................................................................................................................................................... 1
ELECTRICAL CONNECTIONS ......................................................................................................................................................... 2
OPERATING DISTANCES ................................................................................................................................................................ 3
VISION SENSOR AND CONFIGURATOR: GENERAL CHARACTERISTICS ................................................................................ 4
DataVS1 Vision Sensor ......................................................................................................................................................... 4
Installing the sensor............................................................................................................................................................... 5
VSC Configurator .................................................................................................................................................................. 7
Installing the configurator ...................................................................................................................................................... 8
Hardware connections......................................................................................................................................................... 10
Safety recommendations..................................................................................................................................................... 11
INSPECTION CONFIGURATION USING VSC ............................................................................................................................... 12
Introduction.......................................................................................................................................................................... 12
VSC user interface .............................................................................................................................................................. 12
General considerations........................................................................................................................................................ 13
Step 1 - Configuration of the camera settings and choice of the inspection tool................................................................. 13
Step 2 - Configuration of the selected inspection tool ......................................................................................................... 19
Step 3 - Inspection tool function check................................................................................................................................ 20
Step 4 - Output definitions and saving the inspection settings to the sensor ...................................................................... 23
VSC CONFIGURATOR: ADVANCED FUNCTIONS ....................................................................................................................... 26
Output.................................................................................................................................................................................. 26
Trigger Mode ....................................................................................................................................................................... 28
Load/Save ........................................................................................................................................................................... 30
Fail Inspector ....................................................................................................................................................................... 32
DataVS1 Ver........................................................................................................................................................................ 33
Input Config ......................................................................................................................................................................... 34
Standard Protocol ...................................................................................................................................................... 34
Protocol description ................................................................................................................................................................................34
Protocol selection....................................................................................................................................................................................35
Expert Protocol .......................................................................................................................................................... 36
Protocol Selection ...................................................................................................................................................................................38
Digital Teach In .......................................................................................................................................................... 38
Password............................................................................................................................................................................. 38
CONTROLS ..................................................................................................................................................................................... 41
Remarks .............................................................................................................................................................................. 41
Brightness............................................................................................................................................................................ 42
Contrast ............................................................................................................................................................................... 45
Position................................................................................................................................................................................ 49
Width ................................................................................................................................................................................... 52
Edge count .......................................................................................................................................................................... 56
Pattern Match ...................................................................................................................................................................... 59
OCV..................................................................................................................................................................................... 63
Pattern Count ...................................................................................................................................................................... 67
TEACH BUTTON ............................................................................................................................................................................. 71
CHECKS AND PERIODIC MAINTENANCE ................................................................................................................................... 72
WARRANTY .................................................................................................................................................................................... 72
TECHNICAL DATA.......................................................................................................................................................................... 73
OVERALL DIMENSIONS ................................................................................................................................................................ 74
ACCESSORIES ............................................................................................................................................................................... 75
TUTORIAL ....................................................................................................................................................................................... 77
Digital image .................................................................................................................................................................. 77
Machine vision ............................................................................................................................................................... 78
General comments on lighting ....................................................................................................................................... 78
Lighting options .............................................................................................................................................................. 79
Binarization .................................................................................................................................................................... 80
Edge / Edge Detection ................................................................................................................................................... 81
Inspection times ............................................................................................................................................................. 82
Pattern Match.................................................................................................................................................................. 82
Exposure ........................................................................................................................................................................ 83
GLOSSARY ..................................................................................................................................................................................... 84