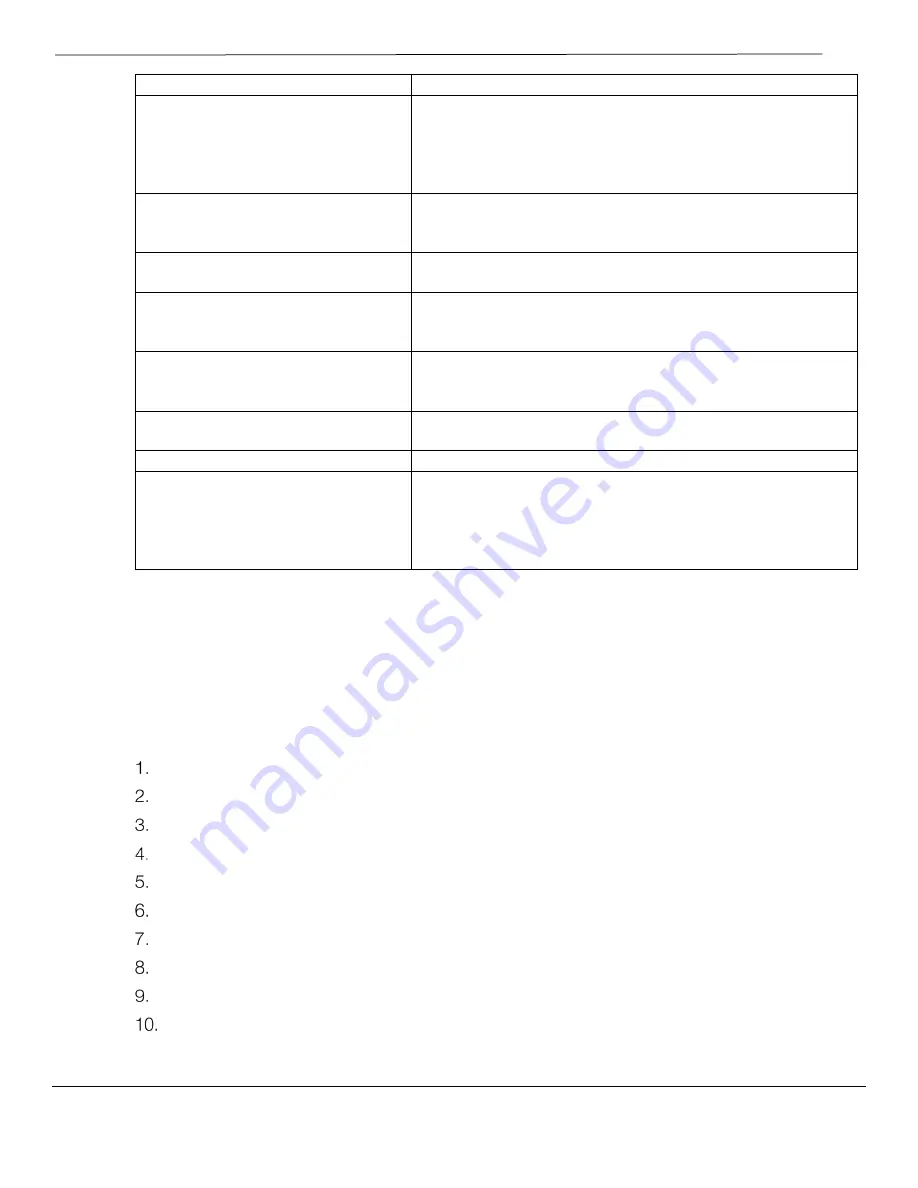
MB-240X Wheel Balancer
45
P/N 5900262 — Rev. A1 — Jan. 2021
Issue/Error Code
Action
00
1.
The sensor is wet or damaged, re-adjust the sensor,
conduct the 100 g calibration after drying or replace the
sensor.
2.
The processor program is corrupted. Replace circuit
board.
00-00
1.
Sensor leads are broken or disconnected. Repair or
reconnect.
2.
Memory values lost, perform the 100 g calibration.
Err1
1.
Check photoelectric circuit board.
2.
Check the Computer Board
Err2
1.
Insufficient speed of rotation. Speed up the rotation.
2.
Replace the Photoelectric Board.
3.
Replace the Computer Board.
Err3
1.
The unbalanced amount is too large.
2.
Replace with a new Wheel.
3.
Conduct the 100 g calibration.
Err4
Photoelectric sensor problem. Readjust the sensor position
or replace.
ErrH
Wheel speed is too fast. Slow down the rotation.
Err8
1.
100 g weight was not correctly applied.
2.
Check internal wiring harness for disconnected or broken
wires.
3.
Check power supply for broken wires.
4.
Computer Board fault, remove and replace.
If you continue to have problems with your Wheel Balancer, visit
Dannmar at
(877) 432-6627
.
Pressure Sensor Adjustment
This adjustment is to be performed if the sensors are damaged or if Error Code 00 appears on the
display. Refer to
Figure H
on the following page.
To Adjust the Pressure Sensors:
Open the cover under the main shaft.
Loosen Nuts (2) (3) (4) and (5).
Loosen Nut (1).
Remove vertical and horizontal rods.
Dry the sensor elements (6) and (7).
Replace the vertical and horizontal rods.
Tighten Nut (4) finger tight.
Tighten Nut (5).
Tighten Nut (2) finger tight.
Tighten Nut (3).
Summary of Contents for MB-240X
Page 46: ...MB 240X Wheel Balancer 46 P N 5900262 Rev A1 Jan 2021 Figure H...
Page 47: ...MB 240X Wheel Balancer 47 P N 5900262 Rev A1 Jan 2021 Wiring Diagram 220 V Power Board...
Page 48: ...MB 240X Wheel Balancer 48 P N 5900262 Rev A1 Jan 2021 Labels...
Page 49: ...MB 240X Wheel Balancer 49 P N 5900262 Rev A1 Jan 2021 D...
Page 58: ...MB 240X Wheel Balancer 58 P N 5900262 Rev A1 Jan 2021 Maintenance Log...
Page 59: ...MB 240X Wheel Balancer 59 P N 5900262 Rev A1 January 2021 Maintenance Log...
Page 60: ...1645 Lemonwood Drive Santa Paula CA 93060 USA 2021 BendPak Inc All rights reserved Dannmar com...