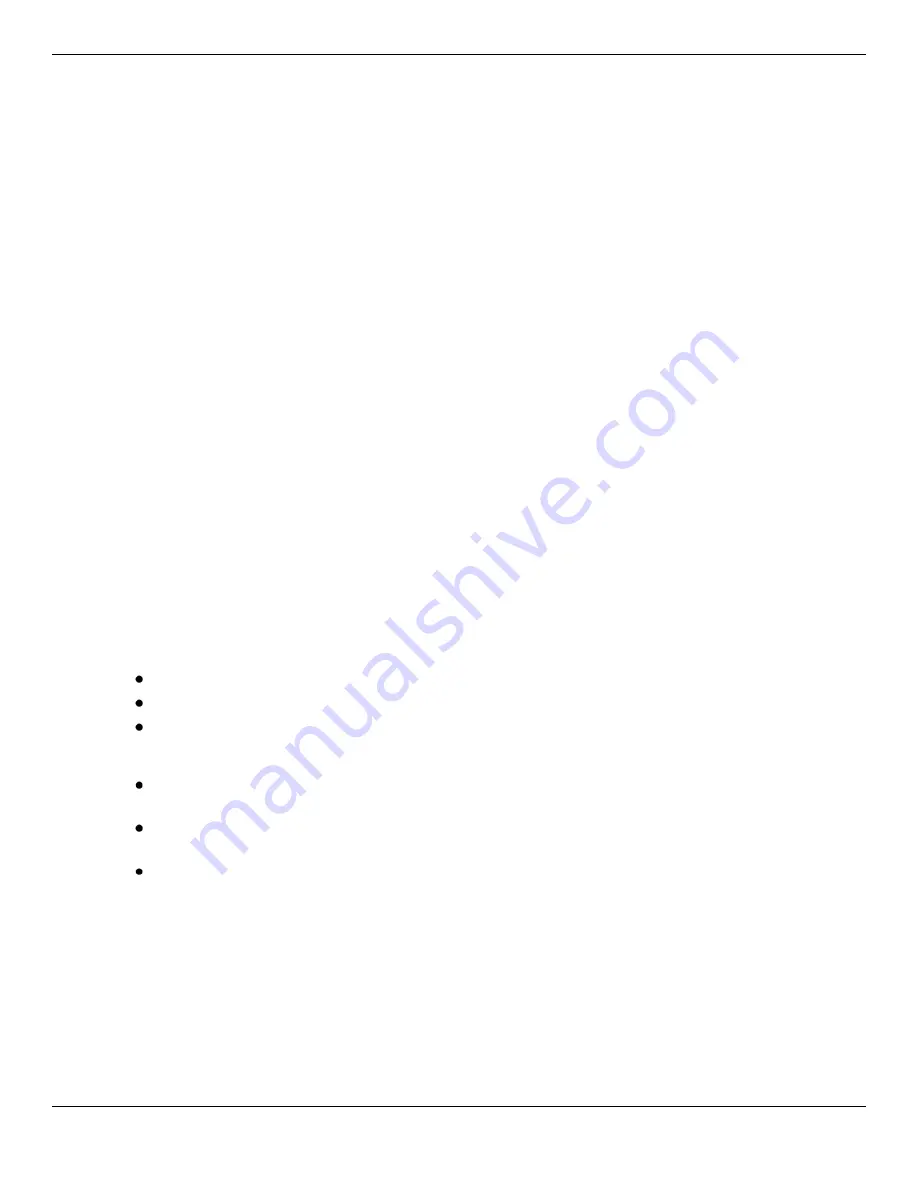
D2-10 Series Two-Post Lifts
29
P/N 5900249 — Rev. B — February 2021
To add Chalk Line Guides
:
1.
Decide where you want to locate the Lift. Which side will be the Approach Side?
2.
Create an Alignment Chalk Line at the Front of the Lift. For Symmetric Lifts, see the drawing on the
previous page.
For Asymmetric Lifts, put the Alignment Chalk Line through the notches, see the drawing on the
previous page.
Make the Alignment Chalk Line longer than the Width for your Lift model.
3.
Create two Perpendicular Chalk Lines at 90° angles to the Alignment Chalk Lines at the Width
distance for the Lift model you are installing.
4.
When you move the Posts into position for a
Symmetric
Lift, put the Base Plates into the corners
created by the Chalk Line Guides, as shown in the drawing on this page.
5.
When you move the Posts into position for an
Asymmetric
Lift, align the correct notches in each
of the Bases Plates with the Alignment Chalk Line, as shown in the drawing on the previous page.
6.
After the Lift Posts locations are properly marked, use chalk or crayon to make an outline of the
Base Plate on the floor at each location. Use the base plates as templates.
7.
Double check all dimensions and verify that the layout is perfectly square.
Installing the Posts
We strongly recommend having multiple people work together to install the Posts.
⚠
DANGER
Pay
special
attention when installing the Lift Posts. If done incorrectly, the Lift
could fall over, potentially causing damage to the Vehicle, the Lift, and injuring
bystanders.
Concrete specifications:
Depth
: 4 inches / 108 mm thick, minimum
PSI
: 3,000 PSI, minimum
Cured
: 28 days, minimum
The Concrete floor where you want to install your Lift must meet the following requirements:
The floor must be a flat, Concrete floor.
Do not install the Lift on a surface with more
than three degrees of slope
.
Do not install the Lift on cracked or defective Concrete or within 6 in (152 mm) of an expansion
joint.
Do not install on a post-tension slab, unless you have verified where the tension cables are located.
Contact the building architect before drilling. Using ground penetrating radar may help determine
the tensioned cable location.
⚠
WARNING
Cutting through a tensioned cable can result in injury or death. Do not drill into a
post-tension slab unless the building architect confirms you are
not
going to hit a
tensioned cable or you have located it using ground penetrating radar.
If colored
sheath comes up during drilling, stop drilling immediately
.
Summary of Contents for D2-10 Series
Page 11: ...D2 10 Series Two Post Lifts 11 P N 5900249 Rev B February 2021 D2 10A Specifications ...
Page 12: ...D2 10 Series Two Post Lifts 12 P N 5900249 Rev B February 2021 D2 10C Specifications ...
Page 72: ...D2 10 Series Two Post Lifts 72 P N 5900249 Rev B February 2021 Labels ...
Page 73: ...D2 10 Series Two Post Lifts 73 P N 5900249 Rev B February 2021 ...
Page 74: ...D2 10 Series Two Post Lifts 74 P N 5900249 Rev B February 2021 ...
Page 75: ...D2 10 Series Two Post Lifts 75 P N 5900249 Rev B February 2021 ...
Page 76: ...D2 10 Series Two Post Lifts 76 P N 5900249 Rev B February 2021 Parts Drawings ...
Page 77: ...D2 10 Series Two Post Lifts 77 P N 5900249 Rev B February 2021 ...
Page 78: ...D2 10 Series Two Post Lifts 78 P N 5900249 Rev B February 2021 ...
Page 79: ...D2 10 Series Two Post Lifts 79 P N 5900249 Rev B February 2021 ...
Page 80: ...D2 10 Series Two Post Lifts 80 P N 5900249 Rev B February 2021 ...
Page 81: ...D2 10 Series Two Post Lifts 81 P N 5900249 Rev B February 2021 ...
Page 82: ...D2 10 Series Two Post Lifts 82 P N 5900249 Rev B February 2021 ...
Page 84: ...D2 10 Series Two Post Lifts 84 P N 5900249 Rev B February 2021 Maintenance Log ...
Page 85: ...D2 10 Series Two Post Lifts 85 P N 5900249 Rev B February 2021 Maintenance Log ...
Page 86: ...D2 10 Series Two Post Lifts 86 P N 5900249 Rev B February 2021 Maintenance Log ...
Page 87: ...D2 10 Series Two Post Lifts 87 P N 5900249 Rev B February 2021 Maintenance Log ...