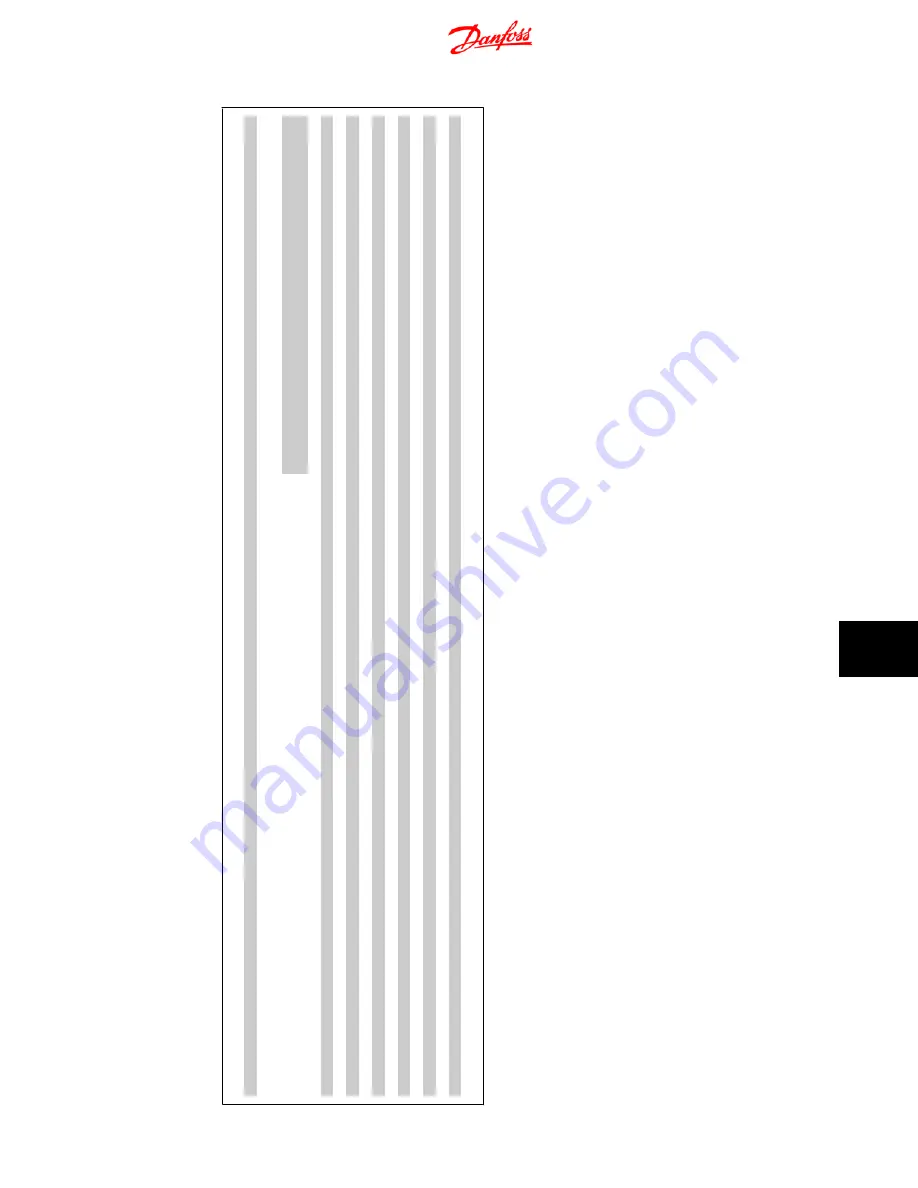
5
2
5
–
6
9
0
V
A
C
D1
/D
3
D2
/D
4
E1/E2
B
loc
k
D
ia
-
gr
am
D
es
ig-
n
at
or
Spare Par
t
Numb
er
Sp
ar
e P
ar
t N
am
e
C
om
m
en
ts
FC
10
2
P13
2
P16
0
P200
P2
50
P315
P400 550
P4
50
P5
00
P56
0
P63
0
FC 2
02
P1
32
P16
0
P200
P2
50
P315
P400 550
P4
50
P5
00
P56
0
P630
FC
30
2
P11
0
P13
2
P160
P2
00
P250
P315
P3
55
P4
00
P5
00
P560
PC
A
PC
A4
176F8
308
Spare,
Cur
re
nt
Scali
ng
PC
A,
4.
54
O
hm
In
st
all
s
on
th
e
Po
w
er
Card
--
-
1
--
-
--
-
--
-
---
1
1
--
-
--
-
PCA
4
17
6F
83
09
Spare,
Cur
re
nt
Scali
ng
PC
A,
3.
79
O
hm
In
st
all
s
on
th
e
Po
we
r
Card
--
-
---
--
-
--
-
--
-
--
-
--
-
--
-
1
--
-
PC
A4
176F8
310
Spare,
Cur
re
nt
Scali
ng
PC
A,
3.
10
O
hm
In
st
all
s
on
th
e
Po
w
er
Card
--
-
---
1
1
--
-
---
--
-
---
--
-
--
-
PCA
4
17
6F
83
11
Spare,
Cur
re
nt
Scali
ng
PC
A,
2.
56
O
hm
In
st
all
s
on
th
e
Po
we
r
Card
--
-
---
--
-
--
-
1
--
-
--
-
--
-
--
-
1
PC
A4
176F8
312
Spare,
Cur
re
nt
Scali
ng
PC
A,
5.
10
O
hm
In
st
all
s
on
th
e
Po
w
er
Card
--
-
---
--
-
--
-
--
-
1
--
-
---
--
-
--
-
PCA
4
17
6F
85
25
Spare,
Cur
re
nt
Scali
ng
PC
A,
5.
85
O
hm
In
st
all
s
on
th
e
Po
we
r
Card
1
---
--
-
--
-
--
-
--
-
--
-
--
-
--
-
--
-
PC
A5
176F8
626
Spare,
Gate
Dri
ve
PC
A,
CC,
D&
E
Frame
G
ate
Drive
Bo
ard
1
1
1
1
1
1
1
1
1
1
PCA
8
17
6F
85
23
Spa
re,
HF
PC
A,
T7
, D
&
E
Frame
Hi
gh
Fre
que
nc
y
Board
1
1
1
1
1
1
1
1
1
1
PC
A11
176F8
522
Spare,
S
oft
charge
PCA
, CC,
T7,
D
Frame
So
ft
ch
arg
e
bo
ard
, I
nc
lud
es
mo
un
ting
br
acke
t
1
1
1
1
1
1
--
-
---
--
-
--
-
PCA
11
17
6F
84
66
Sp
ar
e,
S
of
t
ch
ar
ge
P
CA
, C
C,
T
7,
E
F
ra
m
e
Sof
t
ch
ar
ge
boa
rd
--
-
---
--
-
--
-
--
-
--
-
1
1
1
1
PC
A9
176F8
526
Spare,
Bal
ance
, P
CA,
T7,
D&E
Frame
Cap
aci
tor
Ba
nk
Balance Card,
incl
ud
ed
wi
th
spare
Cap
Bank
1
1
2
2
2
2
2
2
2
2
Table 10.11: Spare P
art
s L
ist
PCA3
-11
High Power Service Manual for VLT
®
FC Series
Adjustable Frequency Drives
10 Spare Parts List
MG.90.L1.22 - VLT
®
is a registered Danfoss trademark
10-13
10
Summary of Contents for VLT HVAC FC 100
Page 219: ......