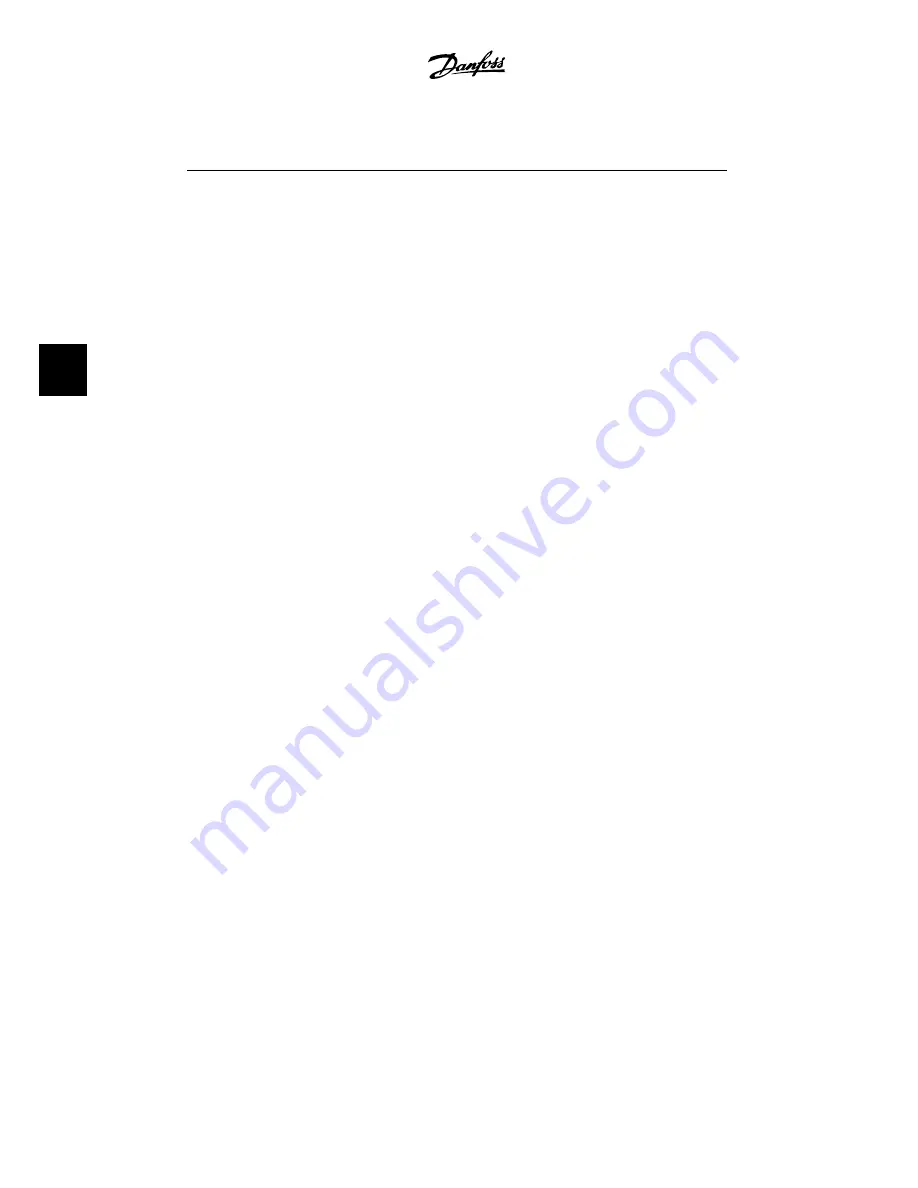
Protection and Features:
•
Electronic thermal motor protection against overload.
•
Temperature monitoring of the heatsink ensures that the adjustable frequency drive trips
if the temperature reaches a predefined level. An overload temperature cannot be reset
until the temperature of the heatsink is below the values stated in the tables on the
following pages (Guideline - these temperatures may vary for different power sizes, en-
closures, etc.).
•
The adjustable frequency drive is protected against short-circuits on motor terminals U,
V, W.
•
If a line phase is missing, the adjustable frequency drive trips or issues a warning (de-
pending on the load).
•
Monitoring of the intermediate circuit voltage ensures that the adjustable frequency drive
trips if the intermediate circuit voltage is too low or too high.
•
The adjustable frequency drive constantly checks for critical levels of internal tempera-
ture, load current, high voltage on the intermediate circuit and low motor speeds. As a
response to a critical level, the adjustable frequency drive can adjust the switching fre-
quency and/or change the switching pattern in order to ensure the performance of the
drive.
5. General Specifications
VLT
®
Automation Drive FC 300
Instruction Manual High Power
116
MG.33.U1.22 - VLT
®
is a registered Danfoss trademark.
5