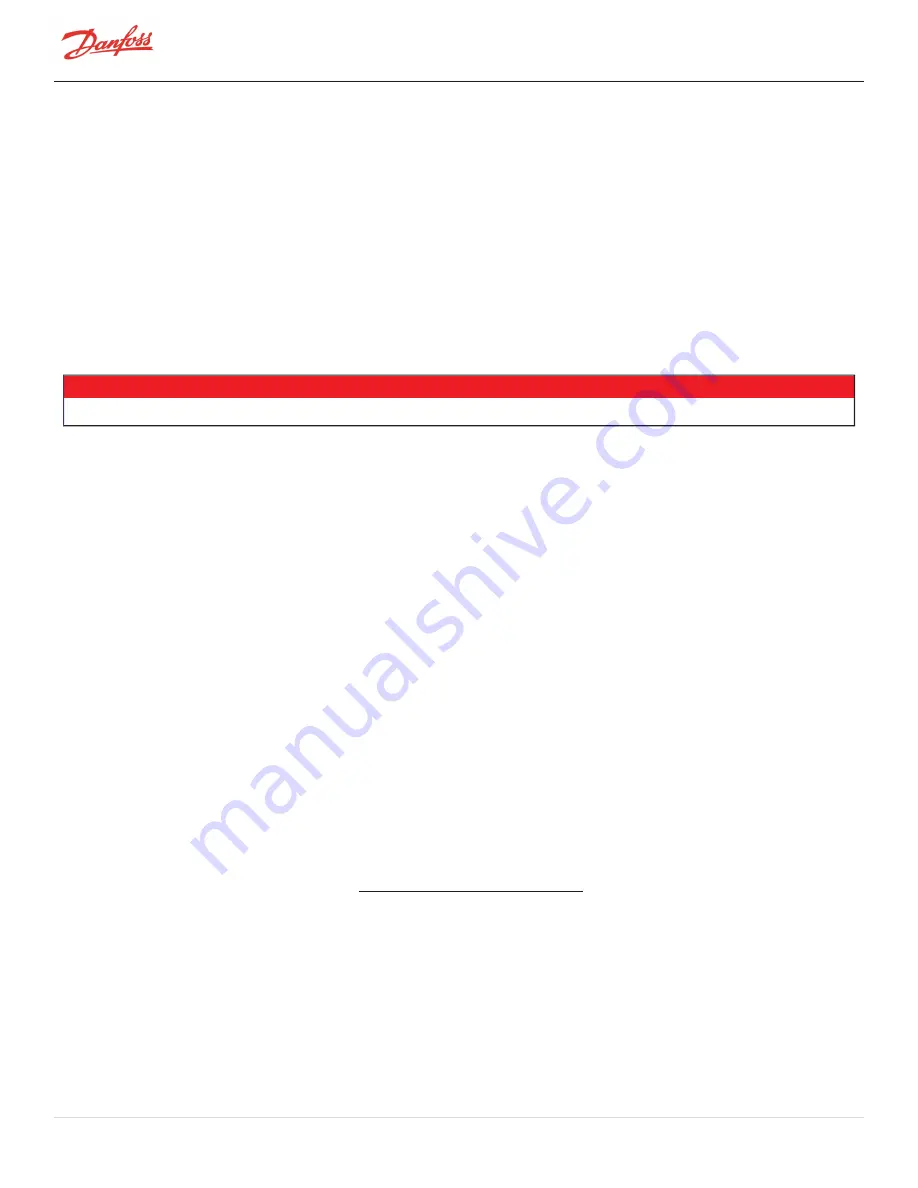
5.3.1.2 Regular Maintenance Calibration
Calibration can be performed during regular maintenance visits for the purpose of comparing the values stored in
EEPROM to the latest current calibration values to determine changes over time. There is no benefit to save the
calibration to EEPROM if the compressor has been operating normally.
A calibration report should always be created for future comparison.
5.3.1.3 Calibration when Troubleshooting
Troubleshooting procedures that require a bearing calibration to be performed will need to be saved to EEPROM.
Click on the “Save to EEPROM” button even if a message indicating values are out of range is displayed. Ensure that
“Stored” values are updated to be identical to “Latest” values. Cycle power to the compressor ensuring the green
LED on the I/O board turns off. This may need to be repeated multiple times. Create a calibration report before any
change is made and after each calibration. Ensure the shaft levitates correctly by clicking “Validate” after calibration
values have been saved to EEPROM.
NOTE
The compressor performs an automatic startup check bearing calibration after a power cycle.
5.3.1.4 BMCC Change
If a replacement BMCC is installed in a compressor, a calibration must be performed, saved to EEPROM, and
repeated to match the BMCC to the specific compressor.
5.3.2 Performing a Calibration
Once Calibration is started , the SMT Bearing Calibration Tool will automatically change the Compressor Control
Mode to Calibration Mode and send a delevitate shaft signal to the bearing control. After calibration is complete, the
SMT will revert back to the original Compressor Control Mode. It is necessary to verify the control mode of the
compressor after completing the calibration process.
A manual validation can be performed by clicking the Validate button. Validation uses the stored calibration values
to momentarily levitate the shaft and compares the values to tolerance limits.
5.3.2.1 Before Performing a Calibration
l
Interlock must be open
l
RS485 or other external compressor communication connection must be disconnected
5.3.2.2 Calibration
1. Open the SMT and connect to the compressor.
2. Open the Bearing Calibration tool. The Bearing Calibration tool displays. Refer to Figure 5-2 Bearing
3. Click on the Start Calibration button.
l
See the current Service Monitoring Tools User Manual for further instructions on performing a
calibration and validation.
Page 264 of 294 - M-SV-001-EN Rev. H 1/23/2023
Summary of Contents for Turbocor TT Series
Page 2: ...THIS PAGE INTENTIONALLY LEFT BLANK Page 2 of 294 M SV 001 EN Rev H 1 23 2023...
Page 14: ...Page 14 of 294 M SV 001 EN Rev H 1 23 2023 THIS PAGE INTENTIONALLY LEFT BLANK...
Page 16: ...Page 16 of 294 M SV 001 EN Rev H 1 23 2023 THIS PAGE INTENTIONALLY LEFT BLANK...
Page 18: ...Figure 1 2 New Type Code Page 18 of 294 M SV 001 EN Rev H 1 23 2023...
Page 46: ...Page 46 of 294 M SV 001 EN Rev H 1 23 2023 THIS PAGE INTENTIONALLY LEFT BLANK...
Page 250: ...Page 250 of 294 M SV 001 EN Rev H 1 23 2023 THIS PAGE INTENTIONALLY LEFT BLANK...
Page 268: ...Figure 5 3 Bearing Calibration Flow Page 268 of 294 M SV 001 EN Rev H 1 23 2023...
Page 274: ...Page 274 of 294 M SV 001 EN Rev H 1 23 2023 THIS PAGE INTENTIONALLY LEFT BLANK...
Page 286: ...Page 286 of 294 M SV 001 EN Rev H 1 23 2023 THIS PAGE INTENTIONALLY LEFT BLANK...
Page 290: ...Page 290 of 294 M SV 001 EN Rev H 1 23 2023 THIS PAGE INTENTIONALLY LEFT BLANK...
Page 292: ...Page 292 of 294 M SV 001 EN Rev H 1 23 2023 THIS PAGE INTENTIONALLY LEFT BLANK...