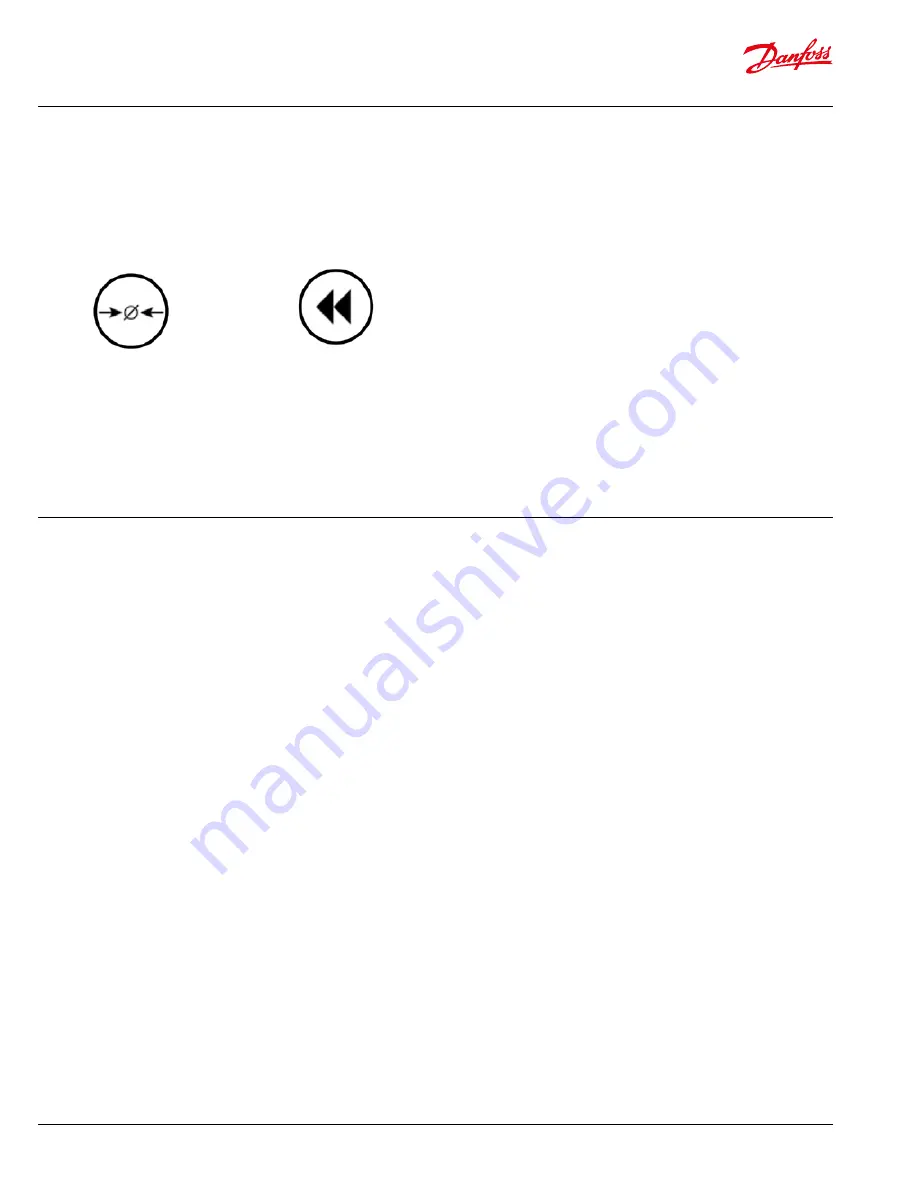
Danfoss ET5040 Crimp Machine Operator’s Manual
17 | ©Danfoss ET5040 Crimp Machine Operator’s Manual | 2022.10.
BC425481951279en-000101
Adjusting the Switching Point of the Crimp Machine
Adjust the switching point of
the machine from closing speed
to (slow) crimping speed in the
“Switching Point” fields, either based
on the displacement or the The
value first reached by the machine
triggers switching from closing to
crimping speed.
Takes you back to the previous
screen.
Operational Steps
1.
Define crimp specification in the appropriate field
2.
Reference the controller specified die required
3.
Load the appropriate dies utilizing the QDC button and instructions listed in this manual for safe die installation
4.
Verify uncrimped fitting diameter is smaller than the ‘switching point’ dimension (see Pg 18). Adjust to adhere as needed.
5.
Set any desired dwell time to hold the crimp in the closed position before auto opening (if desired)
6.
Set the auto opening diameter (if desired)
7.
Safely locate the fitting properly within the crimp tooling
8.
Activate crimper by depressing the cycle start button on the controller or the foot pedal if activated, completing the crimp
9.
Measure the crimped fitting to proper specification
10. If achieved crimp is larger or smaller than acceptable range, enter the needed numerical correction in the offset field (+/-).
11. Save the crimp setting under a user specified name (if desired).
Summary of Contents for ET5040
Page 1: ......