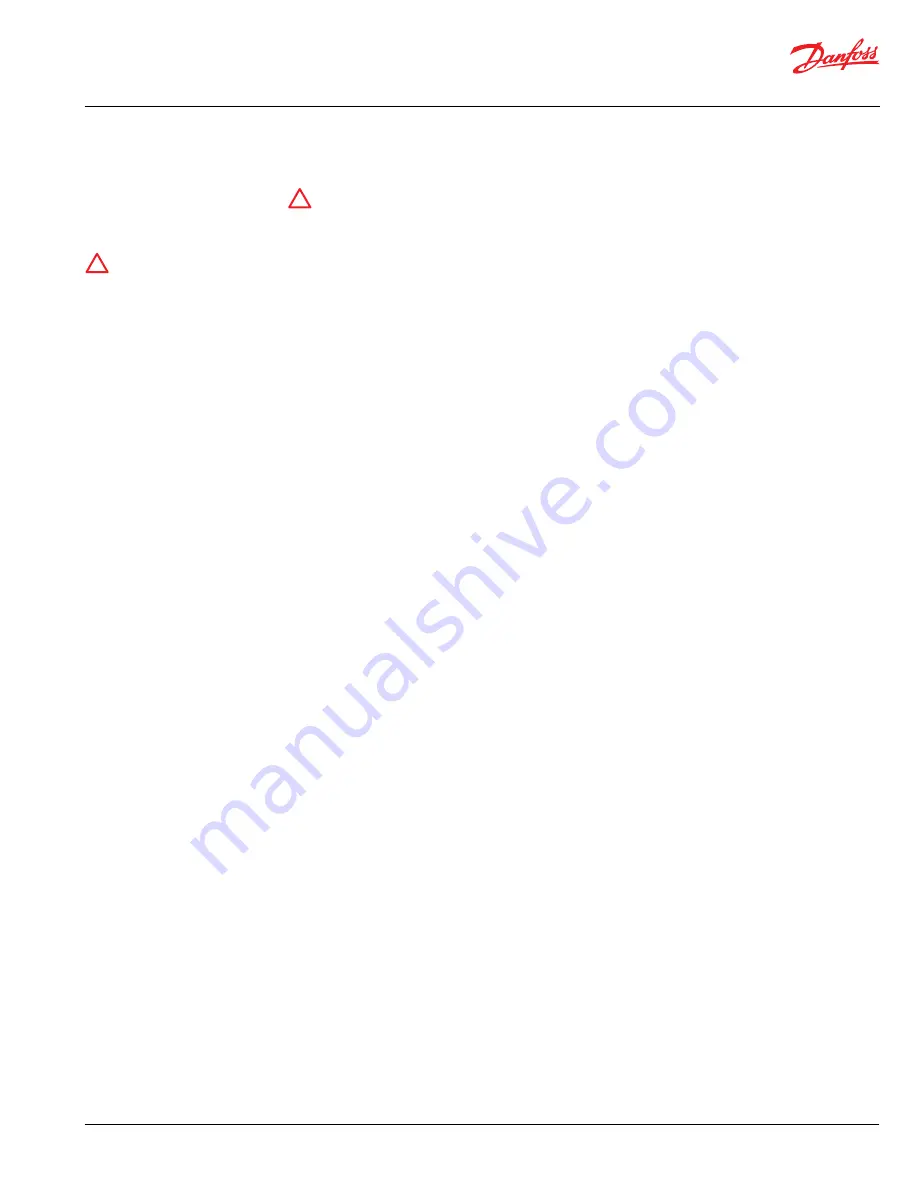
Danfoss ET4000 Crimp Machine Operator’s Manual
AQ439269047772en-000101
© Danfoss ET4000 Crimp Machine Operator’s Manual | 2023.02. | 3
Read and understand the operator’s
manual before attempting to
operate any equipment.
WARNING
Aeroquip hose, hose fittings and
assembly equipment should be
used only with other Aeroquip
hose, hose fittings and assembly
equipment and Weatherhead
hose, hose fittings and assembly
equipment should be used only
with Weatherhead hose, hose
fittings and assembly equipment.
Do not combine or use Aeroquip
or Weatherhead hose, hose fittings
and assembly equipment with
each other, i.e. Aeroquip hose
with Weatherhead fittings, or with
hose, hose fittings or assembly
equipment supplied by another
manufacturer.
Danfoss hereby disclaims any
obligation or liability (including
incidental and consequential
damages) arising from breach
or contract, warranty, or tort
(under negligence or strict liability
theories) should Aeroquip or
Weatherhead hose fittings or
assembly equipment be used
interchangeably or with any hose,
fittings or assembly equipment
supplied by another manufacturer,
or in the event that product
instructions for each specified hose
assembly are not followed.
WARNING
Failure to follow process and
product instructions and limitations
could lead to premature hose
assembly failures, resulting in
property damage, serious injury or
death.
Aeroquip and Weatherhead fitting
tolerances are engineered to match
Aeroquip and Weatherhead hose
tolerances. The combination or
use of Aeroquip or Weatherhead
hose and hose fittings with each
other, i.e. Aeroquip hose with
Weatherhead fittings, or with hose
or fittings supplied by another
manufacturer may result in the
production of unreliable and/
or unsafe hose assemblies and
is neither recommended nor
authorized by Danfoss.
Safety Instructions
1. PREVENT UNAUTHORIZED
OPERATION.
Do not permit anyone to operate
this equipment unless they have
read and thoroughly understand
this manual.
2. WEAR SAFETY GLASSES.
3. AVOID PINCH POINTS.
Do not rest your hand on the crimp
ring. Keep your hands clear of all
moving parts. Do not allow anyone,
other than the operator, close to the
equipment while it is in operation.
4. MAINTAIN DIES WITH CARE.
Dies used in the ET4000 crimp
machine are hardened steel,
offering the best combination of
strength and wear resistance for
long life.
Hardened dies are generally brittle
and care should be taken to avoid
any sharp impact. Never strike a die
with a hardened instrument.
5. USE ONLY SPECIFIED
AEROQUIP/WEATHERHEAD
PRODUCTS.
Make hose assemblies using only
Aeroquip and Weatherhead hose
and fittings specified for this
assembly equipment.
6. VERIFY CORRECT CRIMP
DIAMETERS.
Check and verify correct crimp
diameters of all fittings after
crimping. Do not put any hose
assemblies into service if the crimp
diameters do not meet Danfoss
crimp specifications.
7. MAkE SURE ALL DIES ARE
COMPLETELY IN PLACE
and the cage is positioned
properly on the pressure plate.
8. DO NOT OVER PRESSURIZE.
Do not exceed the 10,000 psi
hydraulic pressure supplied to the
machine.
NOTE: All components used to
connect the pump and crimp
cylinder must meet the criteria
set forth in the Material Handling
Institute Specification #IJ100 for
hydraulic jacking applications.
9. DIE CHANGE. DO NOT
INSERT/REMOVE DIES
WHILE THE POWER IS ON OR
MACHINE IS IN OPERATION.
10. SECURE THE EQUIPMENT TO
A STABLE WORk SURFACE.
Prior to operation, secure the crimp
machine to a stable work surface
to prevent the equipment from
tipping. See pages 5-6 for mounting
instructions.
11. UNPLUG THE POWER
SUPPLY WHEN NOT IN USE.
12. kEEP WORk AREA CLEAN.
Cluttered areas and benches invite
accidents.
13. DO NOT OPERATE WITHOUT
THE BASE ADAPTER RING IN
PLACE.
!
Safety Instructions
!