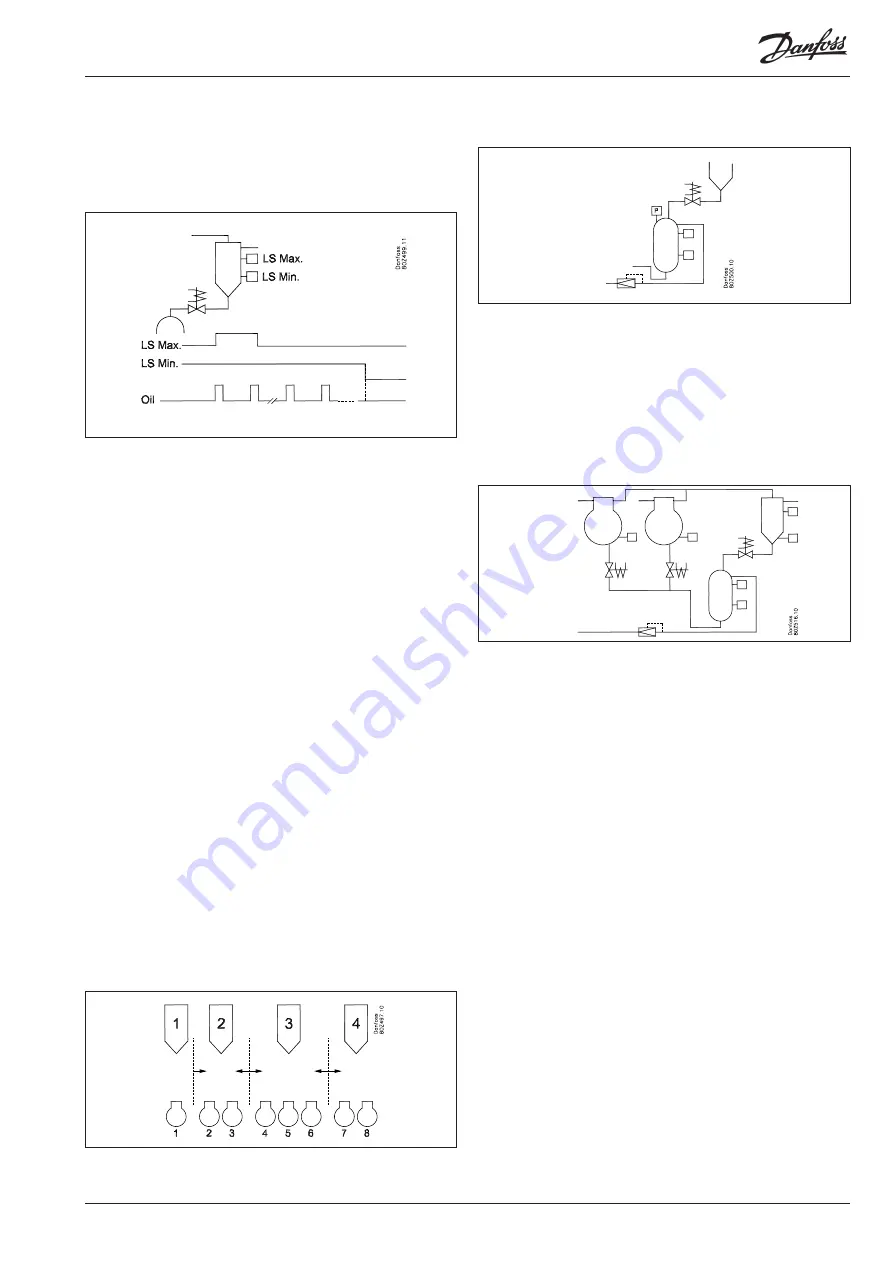
AK-PC 781
Capacity
controller RS8GG602 © Danfoss 2015-03
109
Control principle for pressure in the receiver
Pressostat
- In the case of lack of pressure difference to fill the MT compres-
sors, the solenoid valve is opened in user defined pulses and the
pressure is taken from the oil separator. The pulse length and
the period time between the pulses is determined by the system
and are the same as those set for the oil separator.
- When the pressure transmitter registers the required pressure,
the pulses are stopped.
- Alarm limits and texts for maximum and minimum pressure,
respectively, can be set.
Pulse counter
Here, the controller uses a pulse count to determine the pressure
build-up in the receiver.
Basis: The controller has counted the number of the set pulses
in a period time for all compressors. This value is divided by the
number of compressors.
Reading: The controller registers the number of pulses sending oil
to the compressors.
Action: When the measured number of pulses reaches a percent-
age of the basis (factory setting = 50%), the pulse sequence is
started from the separator to the receiver.
The function is normally used only with MT compressors, but can
also be used in MT+LT operation. This requires, however, an extra
extension module, AK-XM 107A, which counts pulses from the LT
circuit (the pressostat function is recommended instead).
Level signal
High and low level signals can also be received from the receiver.
These signals are only used for monitoring and alarms.
Miscellaneous
All oil valves are closed when the "Main switch" is off.
If you wish to carry out a manual oil injection, this can be done via
the function "Manual operation". Here, you can send one or more
pulses. The length of the pulse can be set in milliseconds.
If a compressor falls out due to lack of oil, it can be reconnected
manually in the plant itself. This can be done via a pulse pressure
on a defined input. There is one reset and this applies to all com-
pressors. Upon reset, all the counters are reset.
It can also be reconnected via the service tool indicated in
the “Safety monitoring” picture.
Simpel oil equalisation
(cyclical systems)
The function only begins when all compressors are in operation.
Here you can set an interval time at which the compressors will
alternate in pausing for a given period of time, so that the oil
equalisation can be performed.
Control principle for emptying the oil separator in the receiver
The system can then be controlled by signal(s) from one or two-
level switches:
• One-level switch:
- Full sequence. When the level switch registers oil, the oil is
emptied over in the receiver in a user-defined pulse sequence.
The system determines the pulse length, period time between
pulses and number of pulses.
- To level. Here a user-defined pulse sequence starts, but the
sequence stops immediately once the oil level falls below the
level switch.
• Two-level switches
Here, the high-level switch will start the pulse sequence, and the
low-level switch will stop the pulse sequence.
If the high level switch is still registering oil after the total number
of pulses has finished, an alarm is given for high oil level in the
separator.
If the low level switch is still registering oil after the total number
of pulses is finished, an alarm is given for remaining oil in the
separator.
An alarm for signal failure is also given if the high level switch
registers oil while a low level switch does not register oil.
If either the high or low level switch is activated in the set time
interval, a "no oil separated" alarm is given.
If an oil separator has been fitted for each compressor, it is the
level switch in the compressor, that determines the emptying
process of oil into the compressor. The level switch in the separa-
tor can be used for monitoring.
If "partial shared oil separators" have been fitted, the distribution
from compressor 1 and up will be as follows: The order
cannot
be changed but the number of compressors that belong to the
individual separators need to be set.
Summary of Contents for ADAP-KOOL AK-PC 781
Page 31: ...AK PC 781 Capacity controller RS8GG602 Danfoss 2015 03 31 ...
Page 41: ...AK PC 781 Capacity controller RS8GG602 Danfoss 2015 03 41 Example continued ...
Page 44: ...44 Capacity controller RS8GG602 Danfoss 2015 03 AK PC 781 ...
Page 135: ...AK PC 781 Capacity controller RS8GG602 Danfoss 2015 03 135 ...