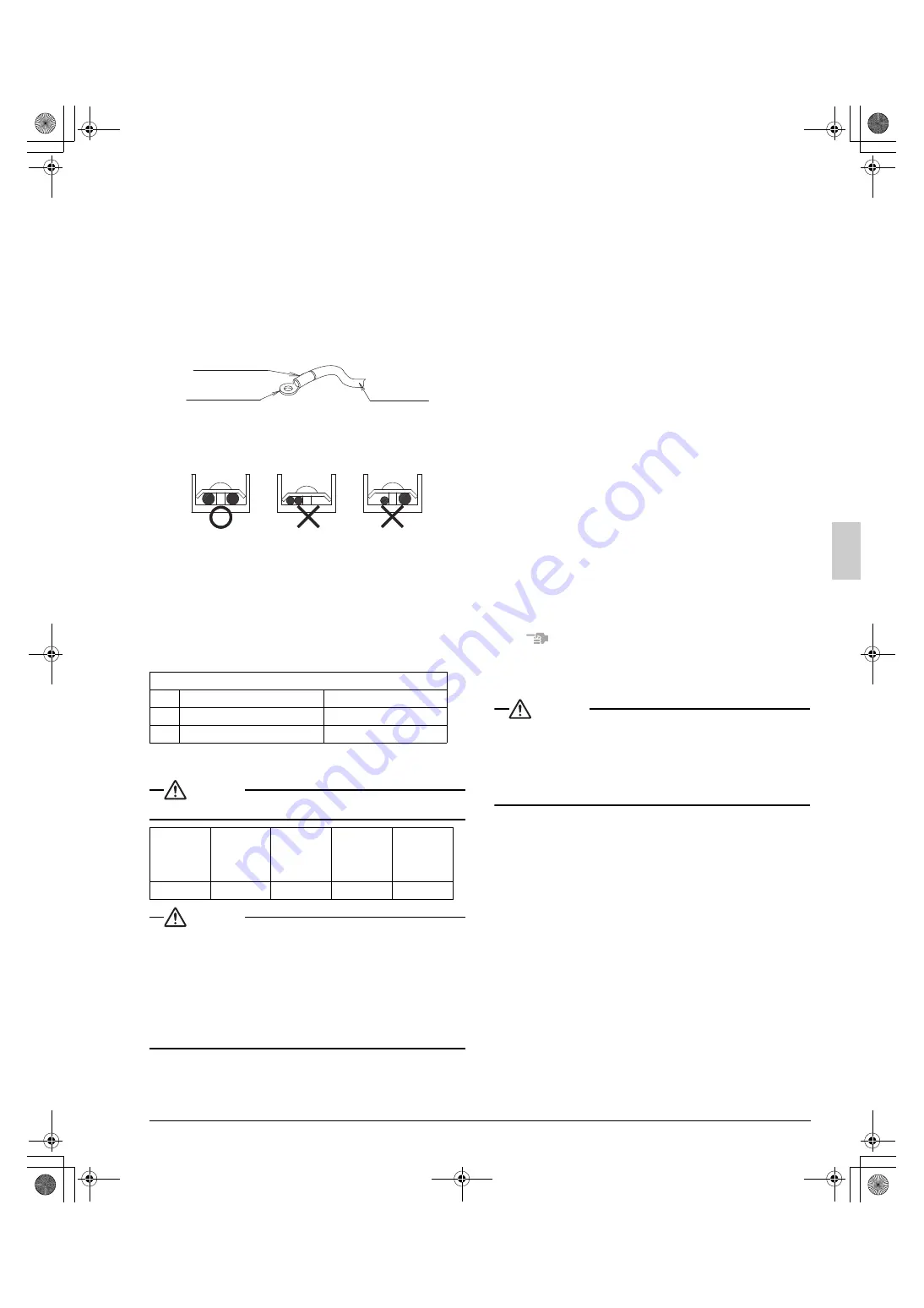
English
7
4.
Knockout hole
5.
Side of unit
6.
Front of unit
7.
Terminal block
8.
Control Box
<Precautions when laying power wiring>
• Wiring of different thicknesses cannot be connected to the power ter-
minal block.
(Slack in the power wiring may cause abnormal heat.)
• Use sleeve-insulated round pressure terminals for connections to
the power terminal block. When none are available, connect wire of
the same diameter to both sides, as shown in the figure.
Follow the instructions below if the wiring gets very hot due to
slack in the power wiring.
• For wiring, use the designated power wire and connect firmly, then
secure using the included clamping material to prevent outside pres-
sure being exerted on the terminal board.
• Use an appropriate screwdriver for tightening the terminal screws.
A screwdriver with a small head will strip the head and make proper
tightening impossible.
• Over-tightening the terminal screw may break it.
See the table below the tightening torque of the terminal screws.
6-3 How to connect the power supply wiring
CAUTION
Attach a circuit breaker/GFCI.
CAUTION
• The wiring should be selected in compliance with local specifica-
tions. See the table above.
• Always turn off the power before doing wiring work.
• Grounding should be done in compliance with local laws and reg-
ulations.
• As shown in figure 18, when connecting the power supply wiring to
the power supply terminal block, be sure to clamp securely.
• Once wiring work is completed, check to make sure there are no
loose connections among the electrical parts in the control box.
(Refer to figure 17)
1.
Stop valve attachment plate
2.
Clamp (accessory)
3.
Connecting power supply wiring
4.
Ground wire (Yellow/Green)
5.
Terminal block (X1M)
6.
Transmission wiring
7.
(To X2M [TO IN/ D UNIT] (F1, F2))
8.
Terminal block (X2M)
9.
Insulation tube (Large) (accessory)
10.
Insulation tube (Small) (accessory)
11.
Cut off the insulation tube sticking out of the outdoor unit.
6-4 Transmission wiring connection procedure
• Between indoor units in the same system, pass the wiring between
the units as shown in figure 18. (There is no polarity.)
(Refer to figure 18)
1.
Terminal block (X2M)
2.
Use balance type shield wire (with no polarity).
3.
Indoor unit
4.
Under no circumstances should 208/230V be connected.
Precautions regarding the length of wiring between units
Exceeding the following limits may cause transmission malfunctions, so
observe them.
Max. wiring length
Max. 984ft.(300m)
Total wiring length
Max. 1968ft.(600m)
Max. no. of branches 8
Precautions regarding wiring between units
•
Do not connect 208/230V power wiring to terminals for the
transmission wiring. Doing so would destroy the entire system.
• Wiring to the indoor unit should be wired to F1 and F2 (TO IN/D unit)
on the outdoor unit’s terminal block (X2M).
NOTE
•
The above wiring should be wired using AWG18-16 stranded, non-
shielded wiring.
(See figure 18 for how to ground the shielded parts.)
•
All transmission wiring is to be procured on site.
CAUTION
Up to 8 branches are available in the wiring among units.
Branch after branch cannot perform wiring between units.
(Refer to figure 19)
1.
Branch
2.
Branches after branch points
3.
Caution on branches in the wiring among units
7.
PRECAUTIONS ON REFRIGERANT PIPING
• Do not allow anything other than the designated refrigerant to get
mixed into the refrigerant cycle, such as air, nitrogen, etc. If any
refrigerant gas leaks while working on the unit, ventilate the room
thoroughly right away.
• Use R410A only when adding refrigerant.
• Installation tools:
Make sure to use installation tools (gauge manifold, charge hose,
etc.) that are exclusively used for R410A installations to withstand
the pressure and to prevent foreign materials (e.g., mineral oils and
moisture) from mixing into the system.
• Vacuum pump:
• Use a 2-stage vacuum pump with a non-return valve.
• Make sure the pump oil does not flow oppositely into the system
while the pump is not working.
• Use a vacuum pump which can evacuate to 500 microns.
Tightening torque (ft·lbf / N·m)
M5
Power terminal
1.76~2.15 / 2.39~2.91
M4
Shield ground
0.87~1.06 / 1.18~1.44
M3
Transmission wiring terminal block
0.58~0.72 / 0.8~0.97
Model name
Phase and
frequency
Voltage
Maximum
overcurrent
protective
device
Minimum
circuit
ampacity
RXSQ60 type
1~60Hz
208/230V
35A
29.1A
Insulating sleeve
Round crimp-style
terminal
Electric Wire
Connect wires
of the same gauge
to both side.
Do not connect
wires of different
gauges.
Do not connect
wires of the same
gauge to one side.
01_EN_3P591321-3B.fm Page 7 Tuesday, December 24, 2019 10:28 AM