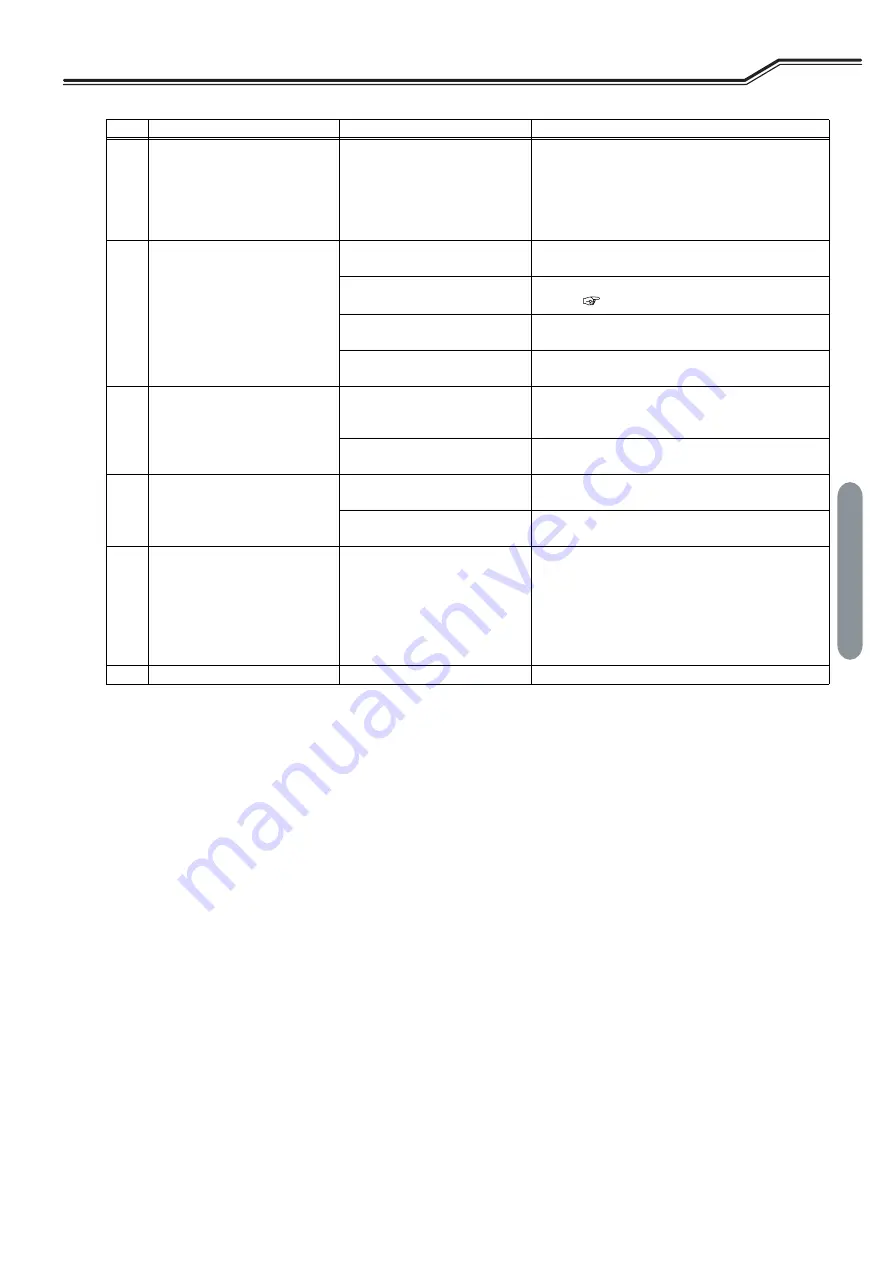
9-5
Chapter 9
T
roubleshooting
T
ROUBLESHOOTING
T
ROUBLESHOOTING
C
HAPTER
9
10
The welding conditions cannot
be set with the operation panel.
The welding mode does not
change even when switched
with the operation panel.
The erroneous prevention
function to prevent malfunction
of the operation panel is
enabled.
(Erroneous operation prevention
function)
Press and hold the ENTER key three seconds or
more to disable the erroneous operation prevention
function the operation panel.
11
Arc is unstable.
The setting of welding mode is
not correct.
Check the settings of wire diameter, wire materials
and shielding gas.
The wire is defective or there is a
failure in wire feeding.
Check that there is no problem in the wire or wire
feeder. (
Connection of the voltage
detection cable is not correct.
Check that connection of the voltage detection
cable is correct.
There is noise in the voltage
detection cable.
Adjust the arc characteristics to the plus side.
12
Wire is not fed (no error code is
displayed).
The pressure roll of wire feeder
came off.
Set correctly the pressure roll of wire feeder. (For
setting, see the instruction manual of the wire
feeder.)
There is an abnormality in
cables of the wire feeder.
Check that there is no abnormality in cables of the
wire feeder.
13
There are blowholes.
There is a problem in the
shielding gas.
Check that there is no abnormality in the gas
cylinder or gas hose.
The chip of the welding torch
wore out.
Replace the chip.
14
Continuous output of the WCR
signal is shown on the monitor
of the robot.
(The WCR signal is used for
communicating with the robot to
check the presence of the
welding current.)
The WCR relay of welding power
source is broken.
The WCR relay on the printed circuit board PCB1
(P30099P00) needs to be replaced.
Contact your dealer.
15
The password is lost.
-
Contact your dealer.
No.
Problem
Possible cause
Corrective action