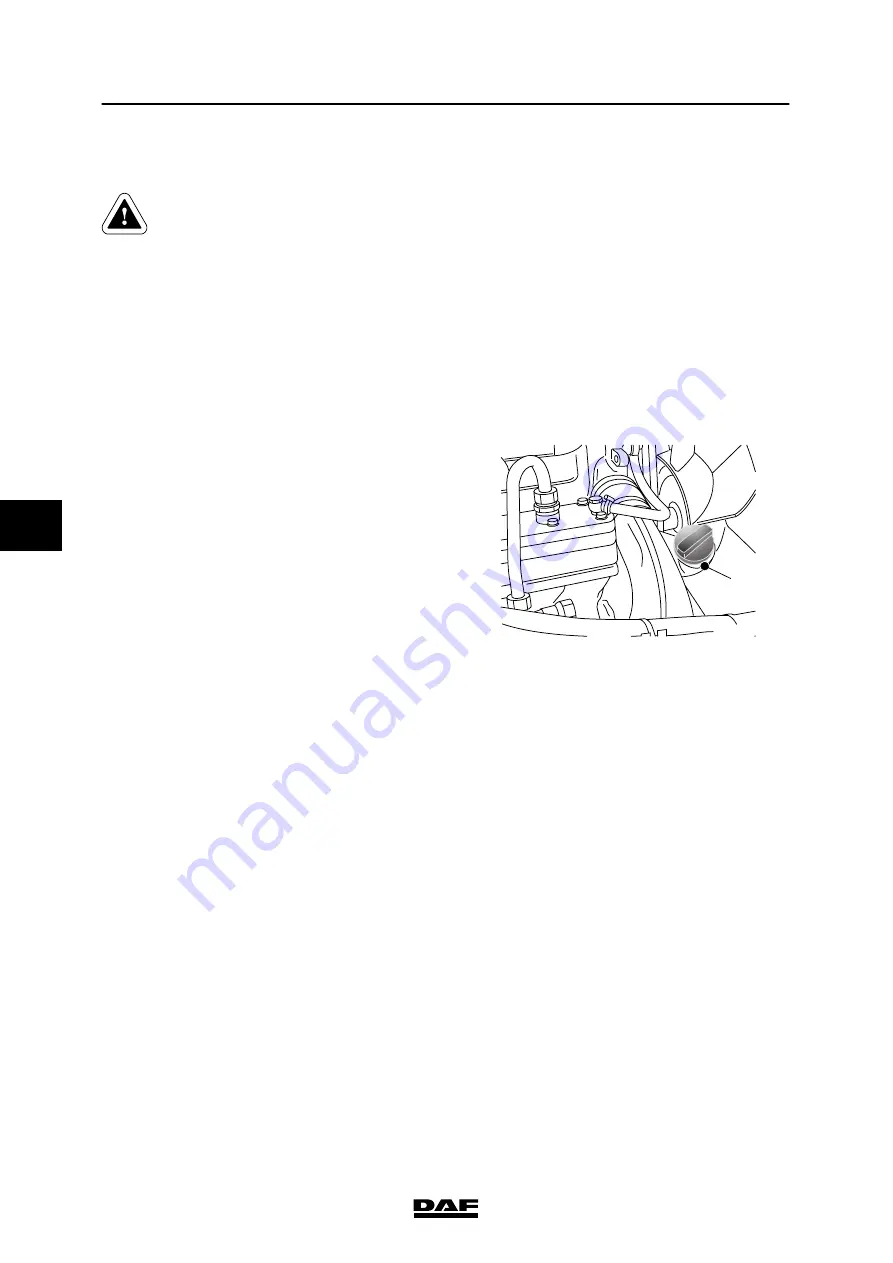
EXPLANATORY NOTES ON THE MAINTENANCE ACTIVITIES
Draining and filling
95
XF
series
5-2
5.2 DRAINING AND FILLING, ENGINE OIL
To prevent skin injury, avoid
unnecessary contact with the
drained oil.
XF/XE ENGINE
Draining engine oil
1.
Position the vehicle on a level surface.
2.
Drain the oil using the drain plug in the oil
sump.
3.
Replace the drain plug oil seal and tighten
the drain plug to the specified torque. See
”Technical data”.
Refilling engine oil
1.
Fill the engine through oil--filler pipe (D) with
the specified engine--oil quantity. See
”Technical data”.
D000268
D
VF ENGINE
Draining engine oil
1.
Position the vehicle on a level surface.
2.
Drain the oil using the drain plug in the oil
sump.
3.
Replace the drain plug oil seal and tighten
the drain plug to the specified torque. See
”Technical data”.
Refilling engine oil
1.
Fill the engine through the filler opening in
the valve cover with the specified engine oil
quantity. See ”Technical data”.
5
200424
Summary of Contents for 95XF
Page 1: ...Maintenance manual 95XF...
Page 2: ......
Page 4: ......
Page 6: ......
Page 8: ...TECHNICAL DATA Contents 95XF series 2 200424 0...
Page 16: ...TECHNICAL DATA Rear axle 95XF series 4 2 0 200424...
Page 18: ...TECHNICAL DATA Retarder 95XF series 5 2 200424 0...
Page 20: ...TECHNICAL DATA Brakes 95XF series 6 2 200424 0...
Page 22: ...TECHNICAL DATA Steering gear 95XF series 7 2 0 200424...
Page 24: ...TECHNICAL DATA Front axle 95XF series 8 2 0 200424...
Page 26: ...TECHNICAL DATA Trailing axle 95XF series 9 2 200424 0...
Page 28: ...TECHNICAL DATA Leading rear axle 09N044 FTP type vehicles 95XF series 10 2 0 200424...
Page 30: ...THREADED CONNECTIONS Contents 95XF series 2 2 200424...
Page 34: ...COOLANT OIL AND LUBRICANTS Contents 95XF series 2 3 200424...
Page 38: ...MAINTENANCE SCHEDULE Contents 95XF series 2 4 200424...
Page 52: ...EXPLANATORY NOTES ON THE MAINTENANCE ACTIVITIES Contents 95XF series 4 5 200424...
Page 60: ...EXPLANATORY NOTES ON THE MAINTENANCE ACTIVITIES General 95XF series 2 6 5 200424...
Page 174: ...EXPLANATORY NOTES ON THE MAINTENANCE ACTIVITIES Draining and filling 95XF series 5 16 5 200424...
Page 182: ...EXPLANATORY NOTES ON THE MAINTENANCE ACTIVITIES Cleaning 95XF series 6 8 5 200424...
Page 187: ......
Page 188: ...English Printed in the Netherlands DW03247106...