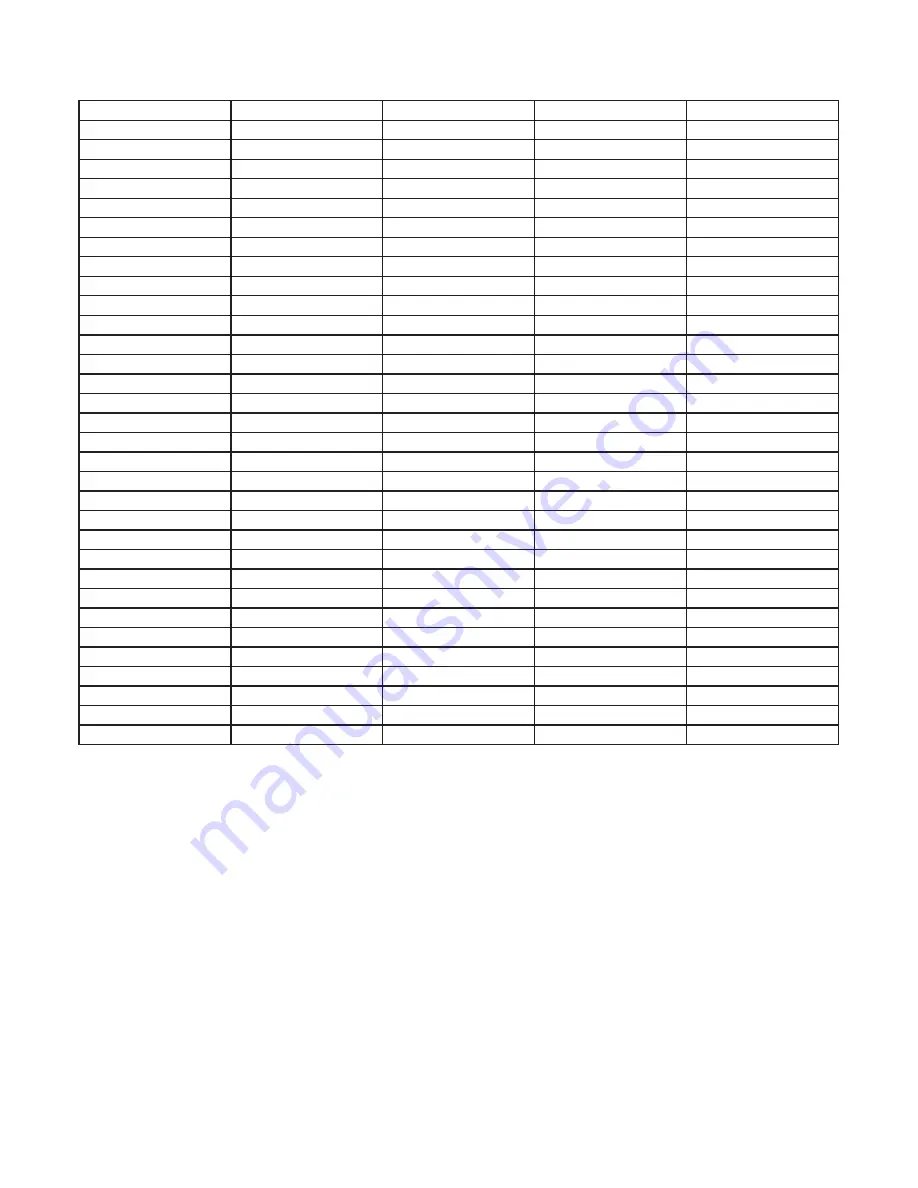
8
6
60T - 280T
COSMOGAS
TECHNICAL FEATURES MYDENS
UM
60T
70T
100T
115T
140T
180T
210T
280T
Burner electrical power
W
110
150
220
220
300
430
430
591
Electrical power absorbed by the pump
W
N.A.
N.A.
N.A.
N.A.
N.A.
N.A.
N.A.
N.A.
Air intake and flue exhaust duct diameter (split)
mm
80
80
110
110
110
160
160
160
Max. flue exhaust duct length (split)
m
10
10
10
10
10
10
10
10
Max. air intake duct length (split)
m
10
10
10
10
10
10
10
10
Equivalent length of one curve
m
4
4
4
4
4
4
4
4
Weighted CO (0% O2)
G20
ppm
15
15
15
15
15
15
15
15
Weighted NOx (0% O2) (EN 483 class 5)
G20
ppm
15
15
15
15
15
15
15
15
CO2 (%) at minimum / maximum output heat
G20
%
8,5 / 8,7
8,5 / 8,7
8,5 / 8,7
8,5 / 8,7
8,5 / 8,7
8,5 / 8,7
8,5 / 8,7
8,5 / 8,7
G25
%
8,3 / 8,8
8,3 / 8,8
8,3 / 8,8
8,3 / 8,8
8,3 / 8,8
8,3 / 8,8
8,3 / 8,8
8,3 / 8,8
G30
%
10,1 / 10,6
10,1 / 10,6
10,1 / 10,6
10,1 / 10,6
10,1 / 10,6
10,1 / 10,6
10,1 / 10,6
10,1 / 10,6
G31
%
9,8 / 10,2
9,8 / 10,2
9,8 / 10,2
9,8 / 10,2
9,8 / 10,2
9,8 / 10,2
9,8 / 10,2
9,8 / 10,2
O2 (%) at minimum / maximum output heat
G20
%
5,8 / 4,9
5,8 / 4,9
5,8 / 4,9
5,8 / 4,9
5,8 / 4,9
5,8 / 4,9
5,8 / 4,9
5,8 / 4,9
G25
%
5,8 / 4,9
5,8 / 4,9
5,8 / 4,9
5,8 / 4,9
5,8 / 4,9
5,8 / 4,9
5,8 / 4,9
5,8 / 4,9
G30
%
5,9 / 5,1
5,9 / 5,1
5,9 / 5,1
5,9 / 5,1
5,9 / 5,1
5,9 / 5,1
5,9 / 5,1
5,9 / 5,1
G31
%
6,0 / 5,4
6,0 / 5,4
6,0 / 5,4
6,0 / 5,4
6,0 / 5,4
6,0 / 5,4
6,0 / 5,4
6,0 / 5,4
Maximum flue gas recirculation in case of wind
%
10
10
10
10
10
10
10
10
Maximum flue gas temperature at boiler outlet
°C
90
90
90
90
90
90
90
90
Minimum flue gas temperature at boiler outlet
°C
30
30
30
30
30
30
30
30
Δt temperature fumes/Return (at 100% of the load) (80/60)
°C
16
17
16
16
17
17
17
17
Δt temperature fumes/Return (at 30% of the load) (37/30)
°C
1
1
1
1
1
1
1
1
Flue gas mass flow rate
kg/h
95
115
163
190
230
284
345
460
Flue gas mass flow rate at minimum output heat
kg/h
20,7
25,4
20,7
20,7
25,4
25,4
25,4
25,4
Head available at exhaust
Pa
110
110
110
110
110
110
110
110
Maximum combustion air temperature
°C
40
40
40
40
40
40
40
40
Maximum CO2 content in combustion air
%
0,9
0,9
0,9
0,9
0,9
0,9
0,9
0,9
Maximum over-heating flue gas temperature
°C
92
92
92
92
92
92
92
92
Max. admissible vacuum in the flue exhaust/intake system
Pa
50
50
50
50
50
50
50
50
Maximum condensate flow rate
l/h
7,2
8,7
12,0
14,4
17,4
21,5
26,1
34,8
Condensate average degree of acidity
PH
4
4
4
4
4
4
4
4
Operating ambient temperature
°C
0 ; + 50
0 ; + 50
0 ; + 50
0 ; + 50
0 ; + 50
0 ; + 50
0 ; + 50
0 ; + 50
Boiler weight (empty)
kg
96
98
142
142
147
211
211
249
18 - TECHNICAL FEATURES
18.1 -
TECHNICAL FEATURES
MYDENS