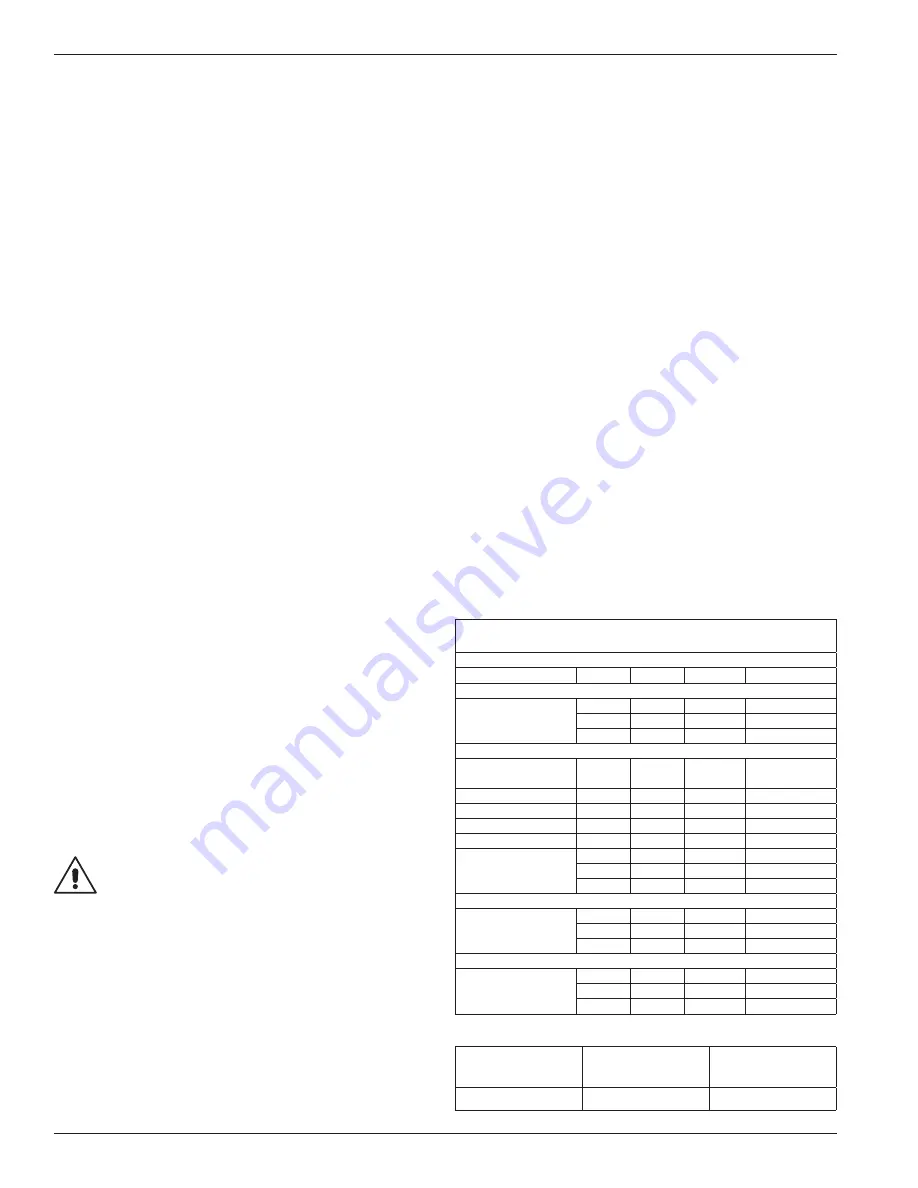
or back-check valve is to be installed in the compressor’s
suction line, care must be taken. The suction line volume
between the restrictive device and the compressor suction
nozzle must be at least ten times the swept cylinder volume.
On liquefied gas applications such as LPG/NH
3
, it is of
extreme importance to prevent the entry of liquid into
the compressor. Installing a liquid trap on the inlet side
will prevent liquid from entering the compressor.
It is of equal importance to protect the discharge side
of the compressor from liquid entry. This may be done
by installing a check valve on the discharge side of the
compressor and using a piping design that does not
allow liquid to gravity drain into the compressor.
For vapor recovery applications, be certain to install
a check valve on vapor lines discharging to the liquid
space of the tank.
All piping must be in accordance with the laws and codes
governing the service. In the United States, the following
codes apply:
For LP Gas—The National Fire Protection Association
Pamphlet No. 58, Standard for the Storage and Handling
of Liquefied Petroleum Gases.
For Ammonia—The American National Standards
Institute, Inc., K61.1-1989, Storage and Handling of
Anhydrous Ammonia.
Copies of these are available from NFPA, 60 Baterymarch
Street, Boston, Mass, 02110 and ANSI, 1430 Broadway, New
York, N.Y., 10018. Install, use and maintain this equipment
according to Corken instructions and all applicable federal,
state, and local laws and previously mentioned codes. Other
laws may apply in different industries and applications.
1.4 Driver Installation/Flywheels
Corken vertical compressors may be driven by either
electric motors or combustion engines (gasoline, diesel,
natural gas, etc.).
WARNING
Never operate a reciprocating compressor
without a flywheel.
Drivers should be selected so the compressor operates
between 400 and 825 RPM. The unit must not be
operated without the flywheel or severe torsional
imbalances will result that could cause vibration and
a high horsepower requirement. The flywheel should
never be replaced by another pulley unless it has a
higher wk2 value than the flywheel.
Humid climates can cause problems with explosion
proof motors. The normal breathing of the motor and
alternating between being warm when running and cool
when stopped can cause moist air to be drawn into the
motor. This moist air will condense, and may eventually
add enough water inside the motor to cause it to fail. To
prevent this, make a practice of running the motor at least
once a week on a bright, dry day for an hour or so without
the V-belts. During this period of time, the motor will
heat up and vaporize the condensed moisture. No motor
manufacturer will guarantee their explosion proof or totally
enclosed (TEFC) motor against damage from moisture.
For installation with engine drivers, thoroughly review
instructions from the engine manufacturer to assure the
unit is properly installed.
1.5 Crankcase Lubrication
To ensure proper lubrication of the crankcase parts
before startup, the crankcase should be filled through the
nameplate inspection opening (see figure 1.5C).
Non-detergent oil is recommended for Corken vertical
compressors. Detergent oils tend to keep wear particles
and debris suspended in the oil, whereas non-detergent
oils let them settle in the bottom of the crankcase.
When non-detergent oils are not available, detergent
oils may usually be successfully substituted, although
compressors handling ammonia, amine, or imine gases are
notable exceptions. These gases react with the detergent
and cause the crankcase oil to become corrosive and
contaminated. Figures 1.5A and 1.5B show recommended
oil viscosities and crankcase capacities. Ensure oil is
compatible with the product being compressed.
Compressor
Model
Approximate
Quarts
Capacity
Liters
WFD551
7.0
6.6
Figure 1.5B: Oil capacity chart
Acceptable Crankcase Oil Products
for Corken Compressors
Constant Weight - Non-Detergent - R&O Inhibited
Oil product
ISO
VI
SAE
Ambient Temp.
Exxon®
TERESSTIC
100
95
30
65° - 100° F
68
95
20+
45° - 70° F
46
95
20
35° - 50° F
Mobil®
RARUS 427
Reciprocating
100
95
30
65° - 100° F
Compressor Oil
DTE Oil Heavy Medium
64
95
20+
45° - 100° F
Dectol R&O Oil
44
95
20
35° - 50° F
Conoco®
Dectol R&O Oil
100
98
30
65° - 100° F
68
97
20+
45° - 70° F
46
99
20
35° - 50° F
Texaco®
Regal R&O Oil
100
92
30
65° - 100° F
68
97
20+
45° - 70° F
46
102
20
35° - 50° F
Sun®
SunVis 900 Oil
100
100
30
65° - 100° F
68
100
20+
45° - 70° F
46
100
20
35° - 50° F
Figure 1.5A: Oil selection chart
6