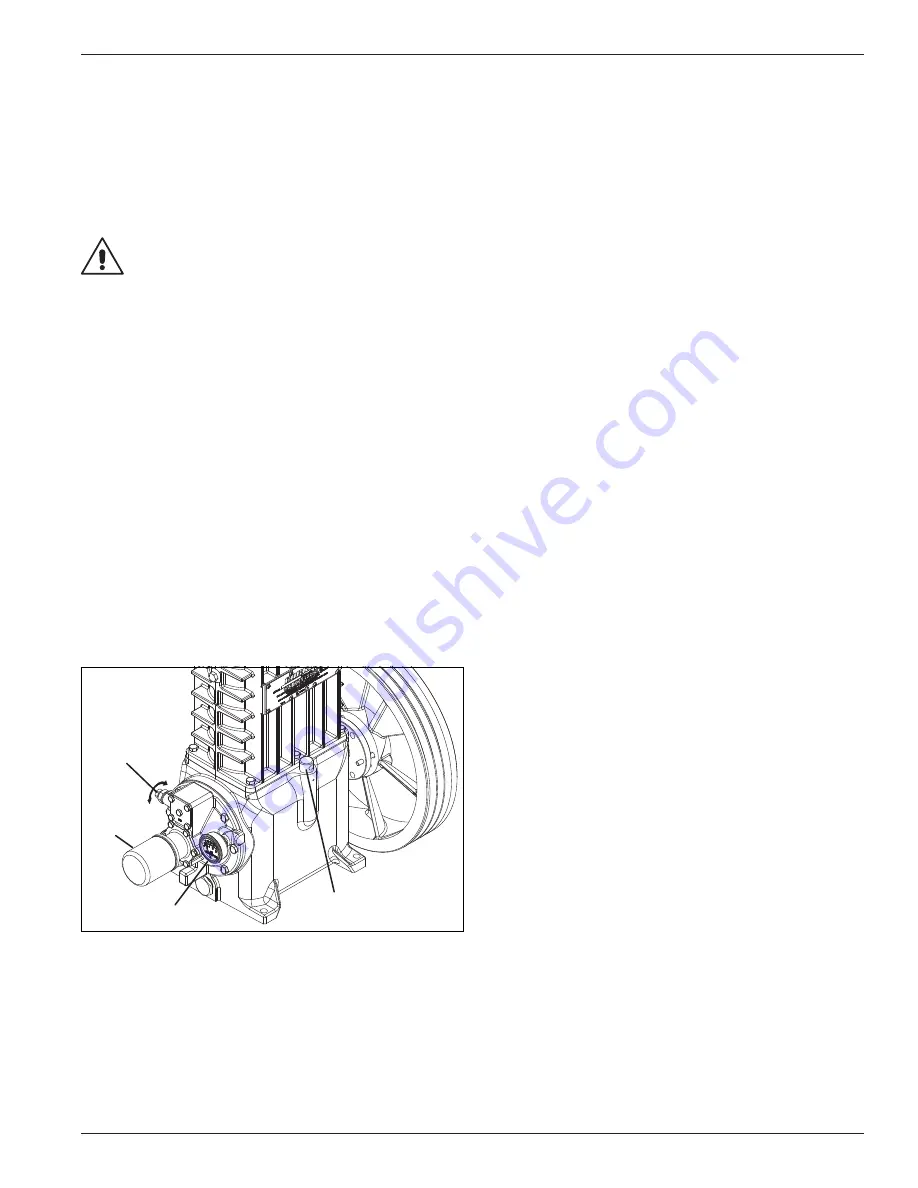
2.3 Crankcase Oil Pressure
Adjustment
Your Corken compressor is equipped with an
automatically reversible gear type oil pump. It is
essential to ensure the pumping system is primed and
the oil pressure is properly adjusted in order to assure
smooth operation.
WARNING
Before starting your compressor, check and
fill the crankcase with the proper amount of
lubricating oil.
When the compressor is first started, observe the
crankcase oil pressure gauge. If the gauge fails to indicate
pressure within 30 seconds, stop the machine. Loosen
the oil filter and remove the pressure gauge. Restart the
compressor and run it until oil comes out of the pressure
gauge opening or around the filter. Tighten the filter and
reinstall the pressure gauge.
The oil pressure should be about 20 psi (1.4 bars)
minimum for normal service. If the compressor
discharge pressure is above 200 psi (14.8 bars) the oil
pressure must be maintained at a minimum of 25 psi
(1.7 bars). A spring-loaded relief valve mounted on the
bearing housing opposite the flywheel regulates the
oil pressure. As shown in figure 2.3, turn the adjusting
screw clockwise to increase the oil pressure and
counterclockwise to lower it. Be sure to loosen the
adjusting screw locknut before trying to turn the screw
and tighten it after making any adjustment.
Oil filter
Oil pressure gauge
Breather cap
Oil pressure
relief valve and
adjustment screw
Figure 2.3: Oil pressure adjustment
2.4 Startup Check List
Please verify each item on this list below before
starting your compressor!
Failure to do so may result
in a costly (or dangerous) mistake.
Before Starting the Compressor
1. Become familiar with the function of all piping associated
with the compressor. Know each line’s use!
2. Make certain actual operating conditions will match
the anticipated conditions.
3. Ensure that the line pressures are within cylinder
pressure ratings.
4. Clean out all piping.
5. Ensure all distance piece openings are tubed or
plugged as desired.
6. Check all mounting shims, cylinder and piping
supports to ensure that no undue twisting forces exist
on the compressor.
7. Make certain strainer elements are in place and clean.
8. Make certain cylinder bore and valve areas are clean.
9. Check V-belt tension and alignment or drive alignment
on direct drive units.
10. Rotate unit by hand and make certain there is no
wobble or play.
11. Check crankcase oil level.
12. Drain all liquid traps, separators, etc.
13. Verify proper electrical supply to motor and panel.
14. Check all gauges and confirm a zero level reading.
15. Test piping system for leaks.
16. Purge unit of air before pressurizing with gas.
17. Carefully check for any loose connections or bolts.
18. Remove all stray objects (rags, tools, etc.) from vicinity
of the unit.
19. Confirm all valves are open or closed as required.
20. Double-check all of the above.
After Starting Compressor
1. Verify and note proper oil pressure. Shut down and
correct any problems immediately.
11