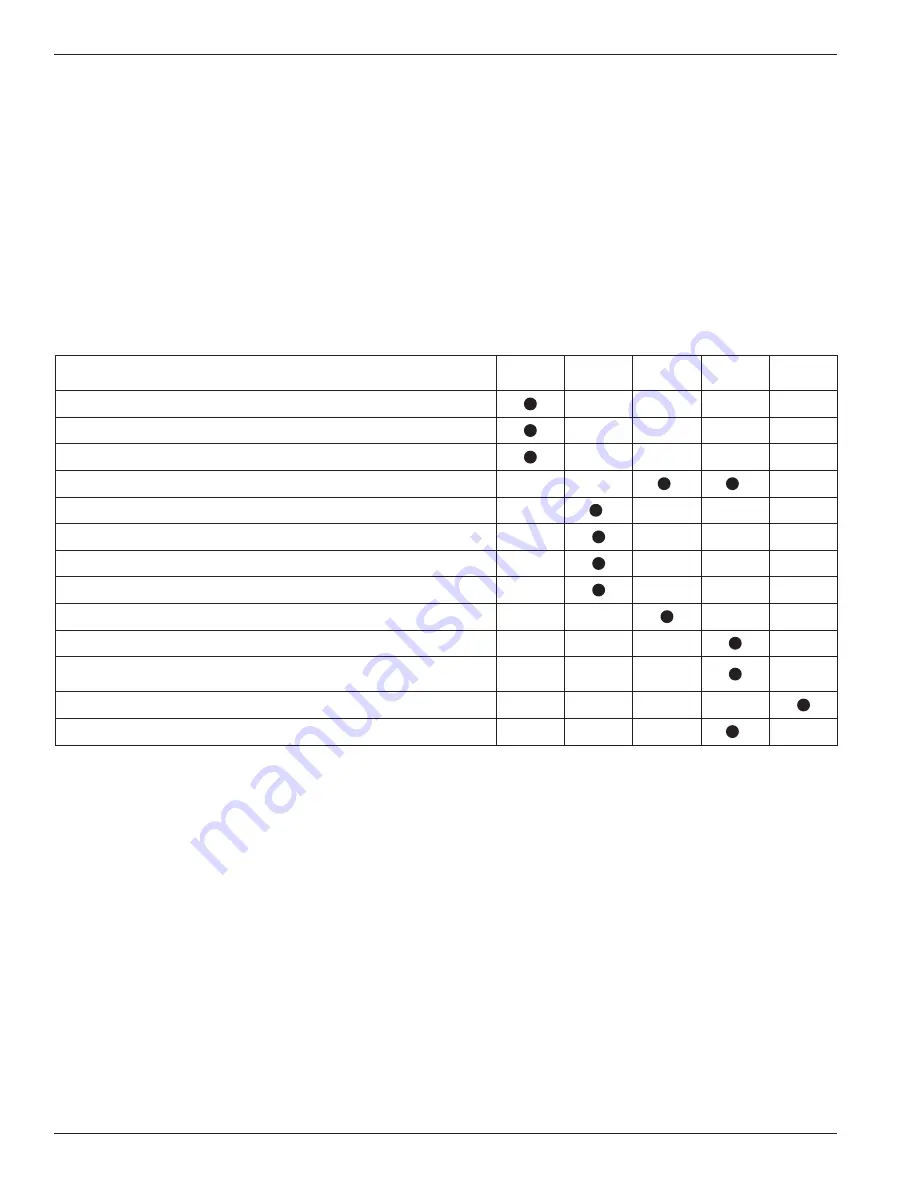
2. Observe noise and vibration levels. Correct immediately
if excessive.
3. Verify proper compressor speed.
4. Examine entire system for gas or oil leaks.
5. Note rotation direction.
6. Check start-up voltage drop, running amperage and
voltage at motor junction box (not at the starter).
7. Verify proper lubrication rate (lubed units only).
8. Test each shutdown device and record set points.
9. Test or confirm set point on all relief valves.
10. Check and record all temperatures, pressures and
volumes after 30 minutes and 1 hour.
11. After 1 hour running time, tighten all head bolts, valve
holddown bolts, and baseplate bolts. See Appendix B
for torque values.
Item to Check
Daily
Weekly Monthly
Six
Months
Yearly
Crankcase oil pressure
Compressor discharge pressure
Overall visual check
Crankcase oil level
2
2
Drain liquid from accumulation points
3
Drain distance pieces
Clean cooling surfaces on compressor and intercooler (if any)
Lubricator supply tank level (if any)
Check belts for correct tension
Inspect valve assemblies
Lubricate motor bearings in accordance with manufacturers'
recommendations
Inspect motor starter contact points
Inspect piston rings
1
1
1
Piston ring life varies greatly, depending on application, gas, and operating pressures. Consult factory for additional recommendations for
your specific application.
2
Change oil every 2,200 hours of operation or every 6 months, whichever occurs first. If the oil is unusually dirty, change it as often as needed
to maintain a clean oil condition. Change filter (part number 4225) with every oil change.
3
Liquid traps should be drained prior to startup.
Chapter 3—Routine Maintenance Chart
Note: The recommended maintenance procedures listed above are general guidelines only. Your specific
maintenance requirements may vary depending on the operating conditions and duty cycle.
12