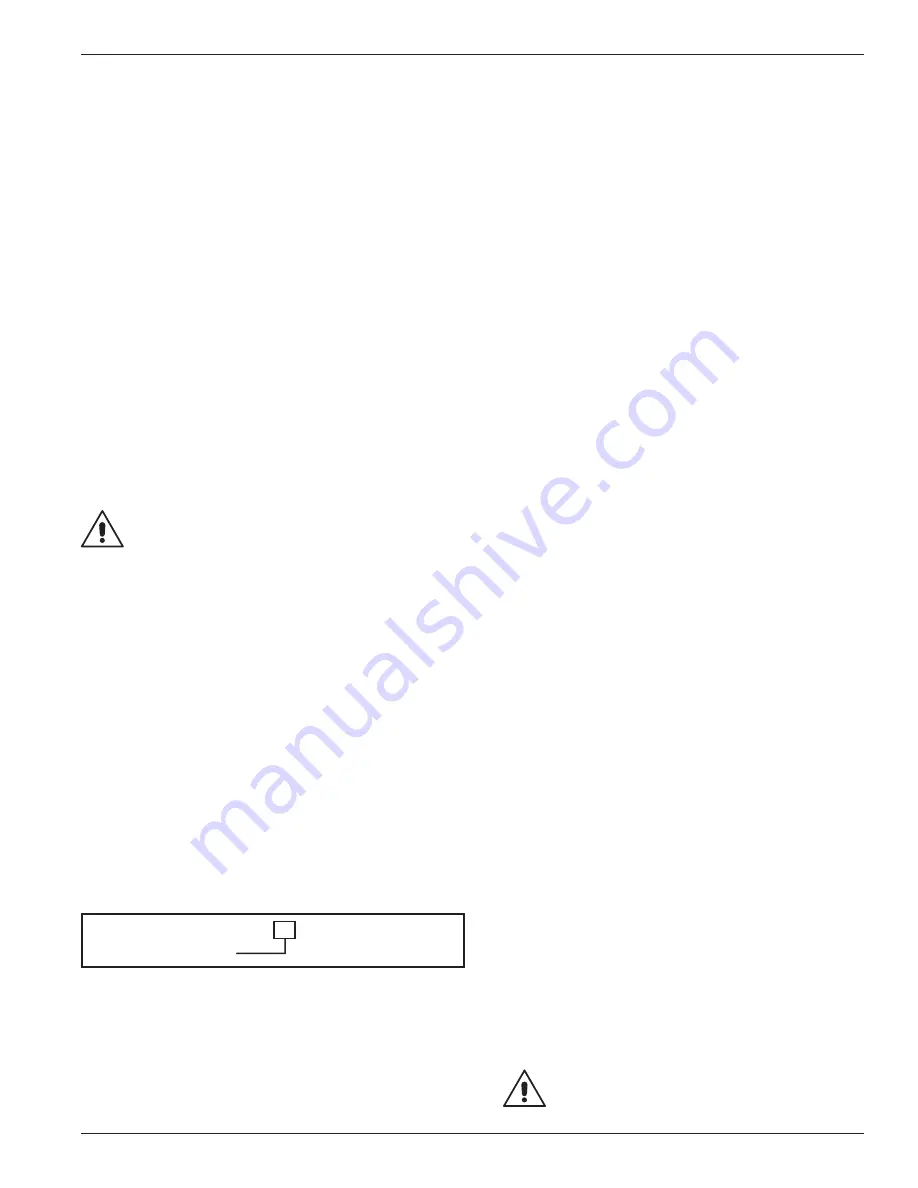
CAUTION: Always relieve pressure in the unit
before attempting any repairs. After repair, the unit
should be pressure tested and checked for leaks at
all joints and gasket surfaces.
If routine maintenance is performed as listed in chapter
3, repair service on your Corken gas compressor is
generally limited to replacing valves or piston rings.
When it comes time to order replacement parts, be sure
to consult the part details appendix in the back of this
Installation, Operation & Maintenance (IOM) manual for
a complete list of part numbers and descriptions.
4.1 Valves
Test the compressor valves by closing the inlet piping
valves while the unit is running; however, do not allow
the machine to operate in this way very long. If the
inlet pressure gauge does not drop to zero almost
immediately, one or more of the valves is probably
damaged or dirty. However, it is possible for the
pressure gauge itself to be faulty.
WARNING
In most cases, if a valve or gasket is leaking,
it will create more heat.
Each suction and/or discharge valve assembly is easily
removed as a unit for inspection. If any part of the
valve assembly is broken, the valve assembly should be
replaced. See valve assembly parts details in the Appendix
E for a complete list of part numbers and descriptions.
If a valve is leaking due to dirt or any other foreign
material that keeps the valve plate and seat from sealing,
the valve may be cleaned and reused. New valve gaskets
and O-rings should be used to assure a good seal.
The valve holddown assemblies and valve assemblies on
the following pages show the various specifications used
on this compressor. Since more than one suction valve
arrangement is available for each model of compressor,
it is necessary to know your complete model number so
you can identify the valve type specification number (see
example listed below).
Model number WFD551AM 4P FDAFSNN
Valve type = spec 4P
Valve Inspection and/or Replacement
Before removing and inspecting the valves, begin by
depressurizing and purging (if necessary) the unit.
Chapter 4—Routine Service and Repair Procedures
Disassembly
1. Unscrew the valve cap (or unloader if applicable)
assembly and remove the O-ring.
2. Remove the valve cover plate, O-ring and holddown
screw by removing each of the four bolts. The
holddown screw is easily removed with the special
wrench supplied with your compressor.
3. After the cover plate and O-ring have been removed,
the valve cage, valve assembly and valve gasket can be
lifted out.
4. Inspect valves for breakage, corrosion, debris and
scratches on the valve plate. In many cases, valves
may simply be cleaned and reinstalled.
5. To clean your valve assemblies, disassemble by
removing the valve seat and/or bumper, valve
spring and valve plate and soak in some rubbing
alcohol for a few minutes. Remove the parts from
the rubbing alcohol and dry each with a lint-free
cloth. Reassemble the valve assemblies in the same
order using the part details in Appendix E. After you
have reassembled the valve assemblies, check for
leaks by pouring a small amount of rubbing alcohol
through the valve seat opening. If the valves are
sealing properly, no alcohol will be allowed to seep
through to the valve bumper.
6. If the valves show any damage, they should be
repaired or replaced. Replacement is usually
preferable although repair parts are available. If
valve plates are replaced, seats should also be
lapped until they are perfectly smooth. If more
than .005 of an inch must be removed to achieve
a smooth surface, the valve should be discarded.
If plates are replaced without relapping the seat,
rapid wear and leakage may occur.
Assembly
1. Insert metal valve gasket into the suction and/or discharge
opening of the head. The metal valve gasket should
always be replaced when the valve is reinstalled.
2. Insert cleaned or new valve assembly. Make sure
the suction and discharge valves are in the proper
suction and discharge opening in the head.
3. Insert the valve cage.
4. Replace the O-ring and valve cover plate. Torque
the bolts to the value listed in Appendix B.
WARNING
Be sure the holddown screw has been removed.
13