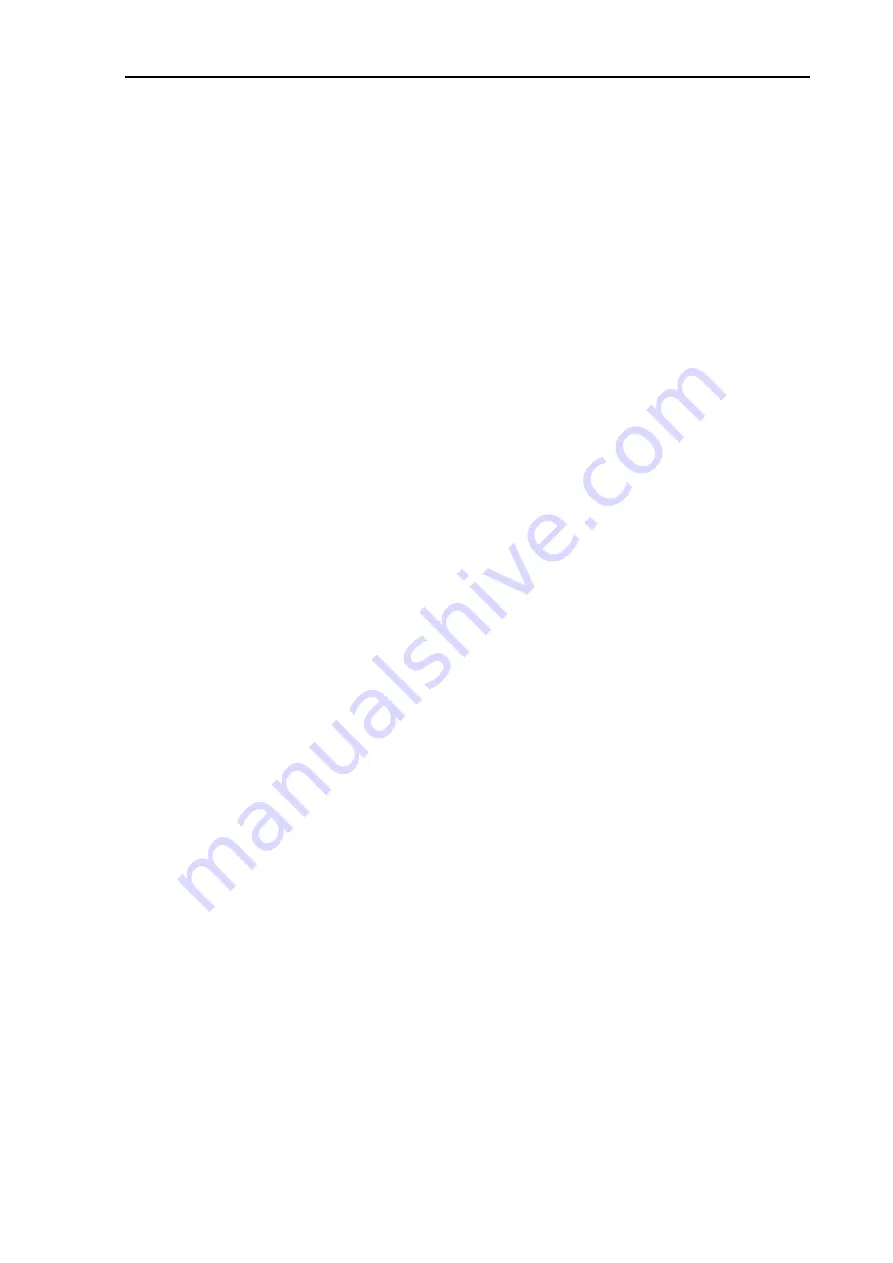
FSG/MTM/001 060511
112
Select
Camera
Loosen the three Camera Back-Plate fixing screws. The screws should be loosened just
enough to allow the Camera Back-Plate to be moved.
Adjust the Vertical Tilt Levers to get 8 Black Lines of the Vertical Position Patterns at both
ends of the scanline, and at the same time maintain correct CCD-Centering.
If 8 Black Lines at both ends can not be obtained:
Set the Vertical Tilt Levers to their nominal positions, that is, horizontal position for the lever
near the “connector end” of the camera board and vertical position for the other lever.
Loosen the lock screw for the Vertical Alignment Arm, see Fig. 4-44, page 121.
Adjust the Vertical Positioning Wheel to get 8 Black Lines at both ends of the scanline.
Tighten the Camera Back-Plate fixing screws, while maintaining the 8 Black Lines at both
ends of the scanline.
The Vertical Alignment Arm should now be turned to parallel with the Back Plate of the
camera.
1) The Vertical Alignment Arm may be turned by the Camera Motor using:
SCANtest 6, Test 9
Select
Camera
Press
Forward (1) to move the arm away from the Back Plate.
Press
Reverse (2) to move the arm towards the Back Plate.
Note: The Vertical Alignment Arm moves very slowly when turned by the motor.
2) Alternatively, the Vertical Alignment Arm may be turned manually. Disconnect the motor
from the connector on the CBE/CBF-Board and remove the two Motor Bracket fixing screws
(see Fig. 4-44, page 121) to dismantle the Camera Motor and turn the pulley of the spindle
manually.
When replacing: Make sure that the cylinder shaped nut on the spindle rests correctly in the
cutout of the Vertical Alignment Arm. The Motor Bracket should be pushed to the uppermost
position when tightening the fixing screws to ensure sufficient tension of the drive belt.
Tighten the lock screw for the Vertical Alignment Arm.
Tolerances:
The cameras should be adjusted to 8 Black Lines of Vertical Position Pattern at both ends of
the scanlines.
For maintenance check the adjustment is considered acceptable if the number of Black Lines
of the Green channel is within:
max. 12 Black Lines
min. 4 Black Lines
Summary of Contents for CHAMELEON 25
Page 69: ...FSG MTM 001 060511 65 Fig 3 21 OIBA Component Layout Fig 3 20 OSB Component Layout ...
Page 102: ...FSG MTM 001 060511 98 Fig 4 19 COUGAR Tx 36 CHAMELEON Tx 36 PREMIER Tx 36 Focus Signals ...
Page 106: ...FSG MTM 001 060511 102 Fig 4 20 COUGAR 25 CHAMELEON 25 Scan Width ...
Page 109: ...FSG MTM 001 060511 105 Fig 4 25 CHROMA Tx 40 CRYSTAL Tx 40 Scan Width Camera C ...
Page 118: ...FSG MTM 001 060511 114 Fig 4 32 COUGAR 25 CHAMELEON 25 CCD Centering and Vertical Positioning ...
Page 183: ...FSG MTM 001 060511 179 Fig 11 1 COUGAR 25 Primary Wiring WHITE LME WHITE SMPS L N WHITE ...
Page 185: ...FSG MTM 001 060511 181 Fig 11 3 CHAMELEON 25 Primary Wiring WHITE LME WHITE SMPS L N WHITE ...
Page 187: ...FSG MTM 001 060511 183 Fig 11 5 COUGAR 36 Primary Wiring WHITE SMPS WHITE LME L N WHITE ...
Page 193: ...FSG MTM 001 060511 189 Fig 11 11 MAGNUM XL 54 Primary Wiring ...
Page 194: ...FSG MTM 001 060511 190 Fig 11 12 MAGNUM XL 54 Secondary Wiring ...
Page 205: ...FSG MTM 002 060511 7 Fig 2 1 COUGAR Sx 25 and CHAMELEON Sx 25 Block Diagram ...
Page 207: ...FSG MTM 002 060511 9 Fig 2 2 CHROMA XL 42 and CRYSTAL XL 42 Block Diagram ...
Page 241: ...FSG MTM 002 060511 43 Fig 6 1 Sx 25 Primary Wiring ...
Page 242: ...FSG MTM 002 060511 44 Fig 6 2 Sx 25 Secondary Wiring ...
Page 243: ...FSG MTM 002 060511 45 Fig 6 3 XL 42 Primary Wiring ...
Page 244: ...FSG MTM 002 060511 46 Fig 6 4 XL 42 Secondary Wiring ...