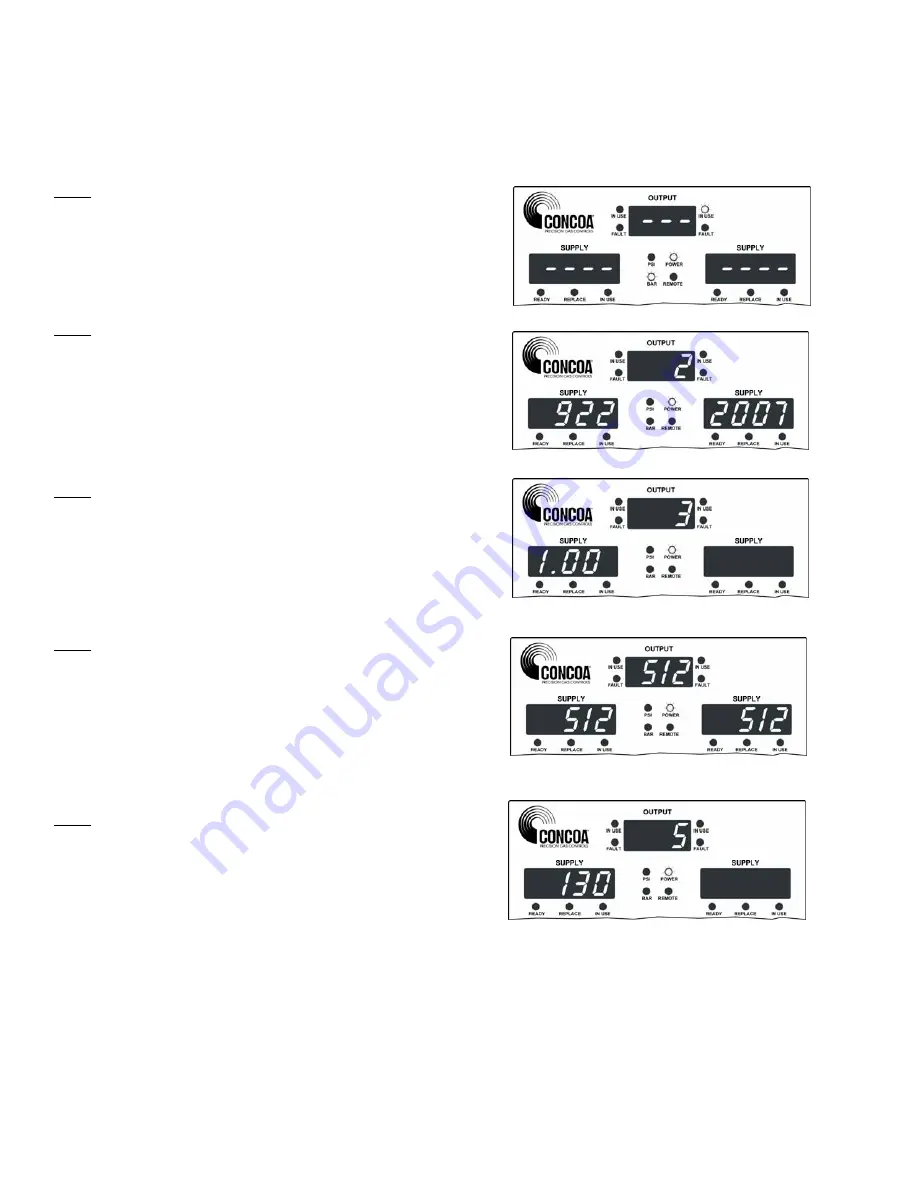
14
PERFORMING SELF TEST (IN-SERVICE)
Through the use of the Reset button on the front panel, a number of items can be observed or analyzed. A number 1 - 21 which is
displayed on the output pressure display identifies each test. To enter Test Mode press and hold the Reset button for 4 seconds. The
system will beep 3 times and then enter Test Mode. A description of the tests follows.
Test 1 –Display Test
This test exercises all segments of the displays and all status
lights except the power and remote alarm indication. If serial
communication is selected, the system will output a code
indicating that a self-test is being performed.
Test 2 - Date of Manufacturing
This test shows the year, month and day the product was
manufactured
Test 3 - Software Revision
This is the revision of the software running the product.
Test 4 – Analog Channel Check
This checks the circuitry that is used to read the pressure
transducers. It should display a value between 475 to 525 to
be working properly.
Test 5 - Display Switchover Pressure
The number on the display is the switchover (changeover)
pressure value that is internally set for product operation. The
value is in the units of measure selected for the product (PSI,
BAR, etc.)
Summary of Contents for IntelliSwitch 57 Series
Page 5: ...5 Figure 1 ...
Page 25: ...25 Figure 14 ...
Page 30: ...30 Figure 20 ...
Page 37: ...37 INTERNAL CABLE ASSEMBLIES REPAIR Figure 31 ...
Page 38: ...38 Figure 32 Figure 33 ...
Page 50: ...50 SELF TEST WORKSHEET Page 1 ...
Page 51: ...51 SELF TEST WORKSHEET Page 2 ...