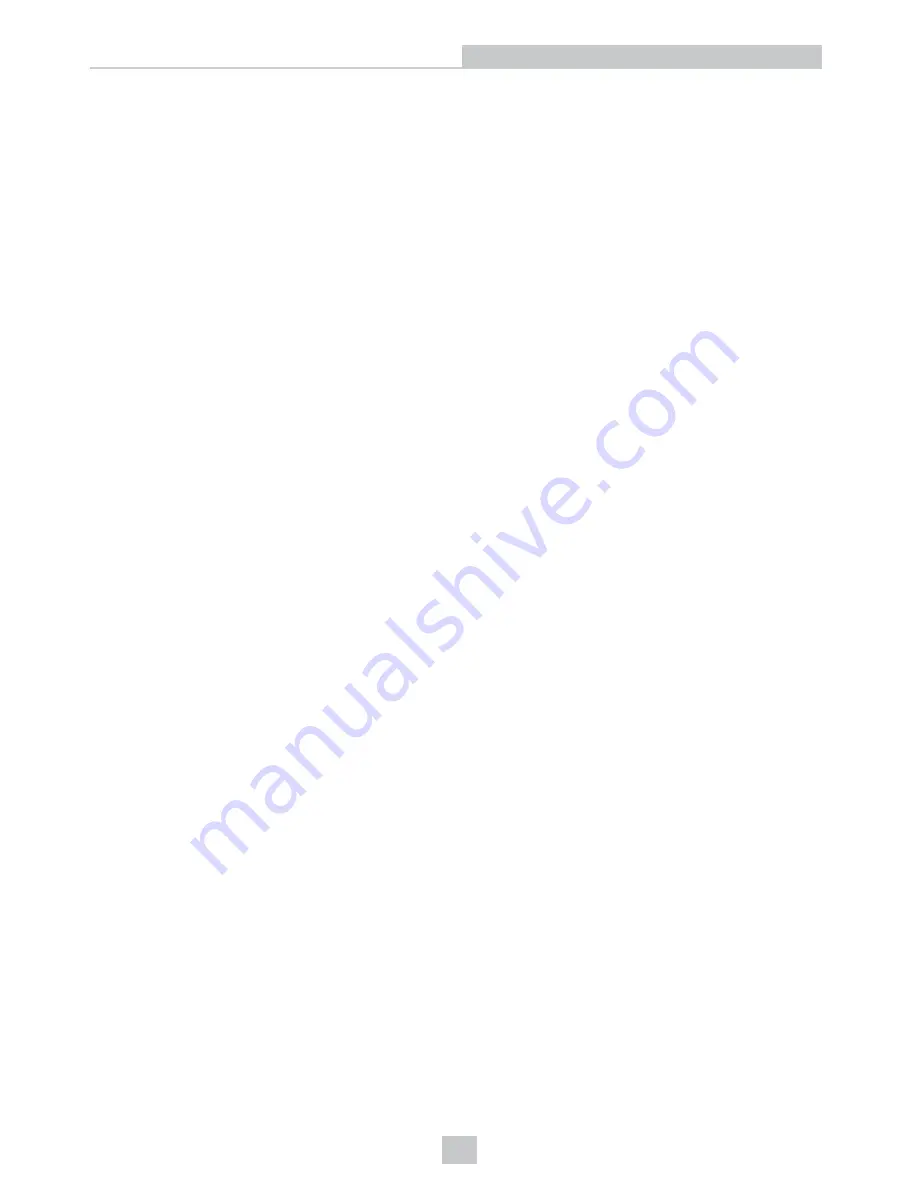
Error Influences
l
Reflection of the Target Surface
The sensor evaluates the diffuse light returned from the laser line projection. Note that it is not possible to identify
a specific minim reflectance factor in order for measurements to be successful. Testing is always required when
using a sensor on transparent objects or highly mirrored surfaces. Direct reflection on such surfaces cannot be
used for accurate measurements due to the fan-shaped form of the laser line projection.
l
Color Differences
Color differences of measurement objects have effects. However, these color differences are often also combined
with different penetration depths of the laser light into the material. Different penetration depths in turn result in
apparent changes of the line thickness. Therefore, color changes, combined with penetration depth changes, can
result in inaccurate measurements.
As the exposure parameters can only be changed as a whole for one profile, careful matching of the exposure to
the target surface is recommended.
l
Temperature Influences
A running-in time of at least 20 minutes during start-up is required in order to achieve a uniform temperature
spread in the sensor.
If measurements with accuracy in the μm range are made, the effect of temperature fluctuations on the mounting
must also be observed by the user.
Due to the damping effect of the thermal capacity of the sensor, fast temperature changes are only measured
after a delay.
l
External Light
An interference filter in the sensor is present for suppression of external light.
In general, the shielding of external light directly emitted on the target or reflected in the sensor must be ensured
using protective covers or similar.
Pay particular attention to unwanted reflections of the laser line outside the measuring object range (background,
object holder or similar) which can be reflected back again into the view area of the receiver.
Matte black surface coatings are recommended for all objects outside the measuring range (object holders,
transport apparatus or similar) which can be reflected back again into the view area of the receiver.
l
Mechanical Vibrations
If you want to achieve high resolutions in the μm range with the sensor, pay particular attention to stable or
vibration-damped sensor and measuring object mounting.
l
Surface Roughness
Surface roughness of 5 μm and more results in "surface noises" due to interference of the laser light.
Direct reflections of the laser light into the receiver can also occur due to fine surface grooves (e.g. abrasion
marks), particularly if these run parallel to the laser line. This can result in inaccurate measurements.
Prevention of this effect might be possible by adjusting several sensor settings e.g. exposure time, filter.
l
Shadowing Effects
l
Receiver: The laser line can disappear completely or partially behind steep edges. The receiver then can
not "see" these areas.
36
Error Influences
Summary of Contents for DS900 Series
Page 1: ...DS900 Series Displacement Sensors Reference 02 21 2018 Version 9 3 0 5...
Page 14: ...Dimensions DS910B 14 Dimensions DS910B...
Page 17: ...Dimensions DS925B 17 Dimensions DS925B...
Page 18: ...18 Dimensions DS925B...
Page 28: ...28 RS422 Synchronization...
Page 31: ...31 Measuring Field Selection...
Page 42: ...January 2018...