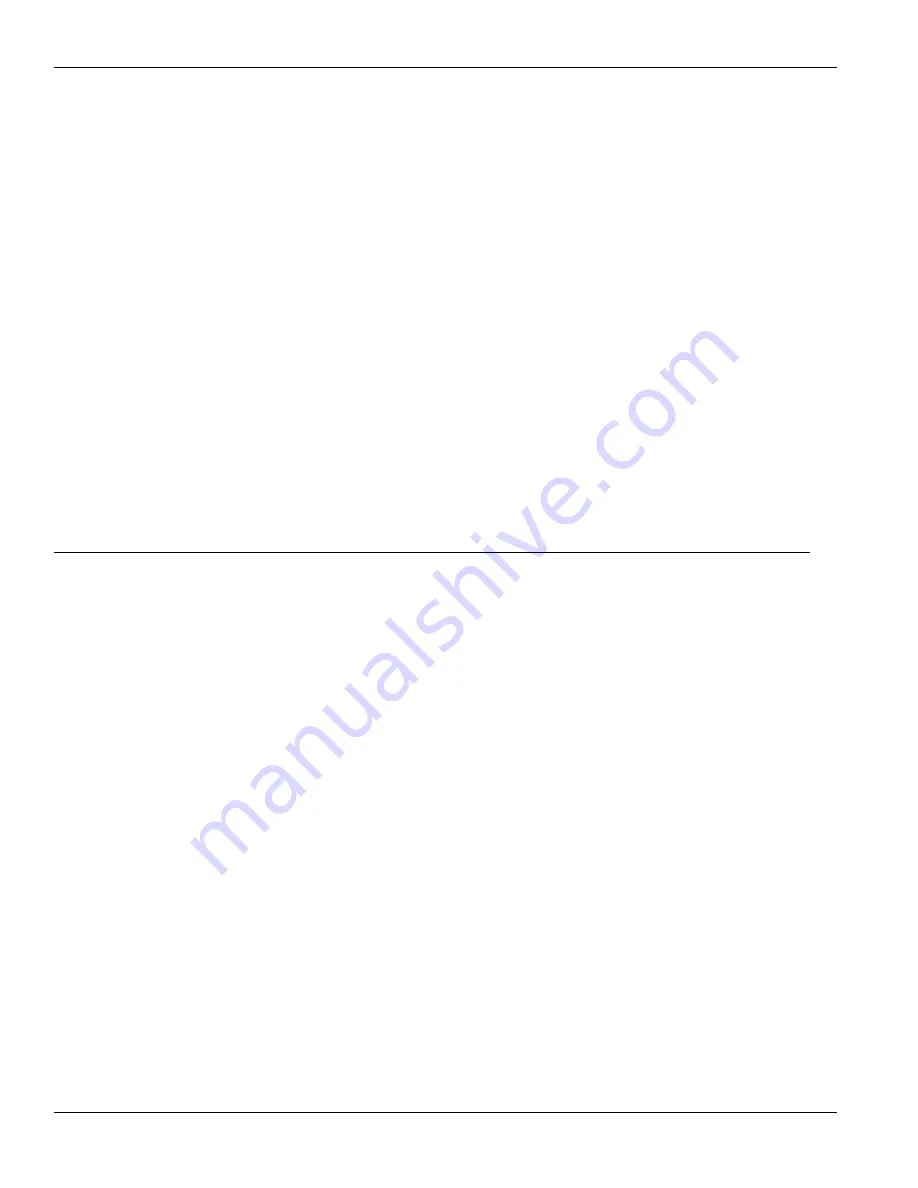
Page 52
FF5300 Operating Manual
5. The tool head is tight and the adjustable clamp on the tool head (Figure A-
7 on page 62) is locked on the axis that is not being used (Section 3.11 on
page 34).
6. The tool head swivel is tight (Figure 3-18 on page 35).
7. The cutting tool or insert is sharp and has the correct geometry for the
material and type of cut.
8. The speed and feed rates are set correctly. If necessary, experiment with
different speeds and feed rates. Typically, slower speeds and shallower cuts
produce less tool chatter.
5.5.4
The machine is not cutting flat
Do the following if the machine is not cutting flat:
1. Before making a critical finish pass, run the machine continuously for at
least 15 minutes to check that the machine is warmed up to operating tem-
perature.
2. Check the machine for level (Section 3.10 on page 33).
3. Check that the machining arm is seated securely in the lower clamp blocks
and that there is no debris between the arm and the clamps.
5.6
D
ECOMMISSIONING
Do the following to decommission the FF5300 before disposal:
1. Drain the oil from the PCU for disposal or recycling through appropriate
channels and according to local regulations.
2. Dispose of or recycle machine parts according to local regulations.
Summary of Contents for FF5300
Page 2: ......
Page 4: ...Page B FF5300 Operating Manual CLIMAX GLOBAL LOCATIONS...
Page 5: ...P N 91025 Rev 4 Page C CE DOCUMENTATION...
Page 12: ...Page vi FF5300 Operating Manual This page intentionally left blank...
Page 20: ...Page 8 FF5300 Operating Manual This page intentionally left blank...
Page 52: ...Page 40 FF5300 Operating Manual This page intentionally left blank...
Page 68: ...Page 56 FF5300 Operating Manual FIGURE A 1 FF5300 ASSEMBLY P N 89900...
Page 69: ...P N 91025 Rev 4 Page 57 FIGURE A 2 FF5300 ASSEMBLY DETAIL P N 89900 7 7...
Page 72: ...Page 60 FF5300 Operating Manual FIGURE A 5 MACHINING ARM ASSEMBLY P N 90337...
Page 74: ...Page 62 FF5300 Operating Manual FIGURE A 7 TOOL HOLDER ASSEMBLY P N 89940...
Page 83: ...P N 91025 Rev 4 Page 71 APPENDIX B SDS Safety Data Sheets are available upon request...
Page 84: ...Page 72 FF5300 Operating Manual This page intentionally left blank...
Page 85: ......
Page 86: ......