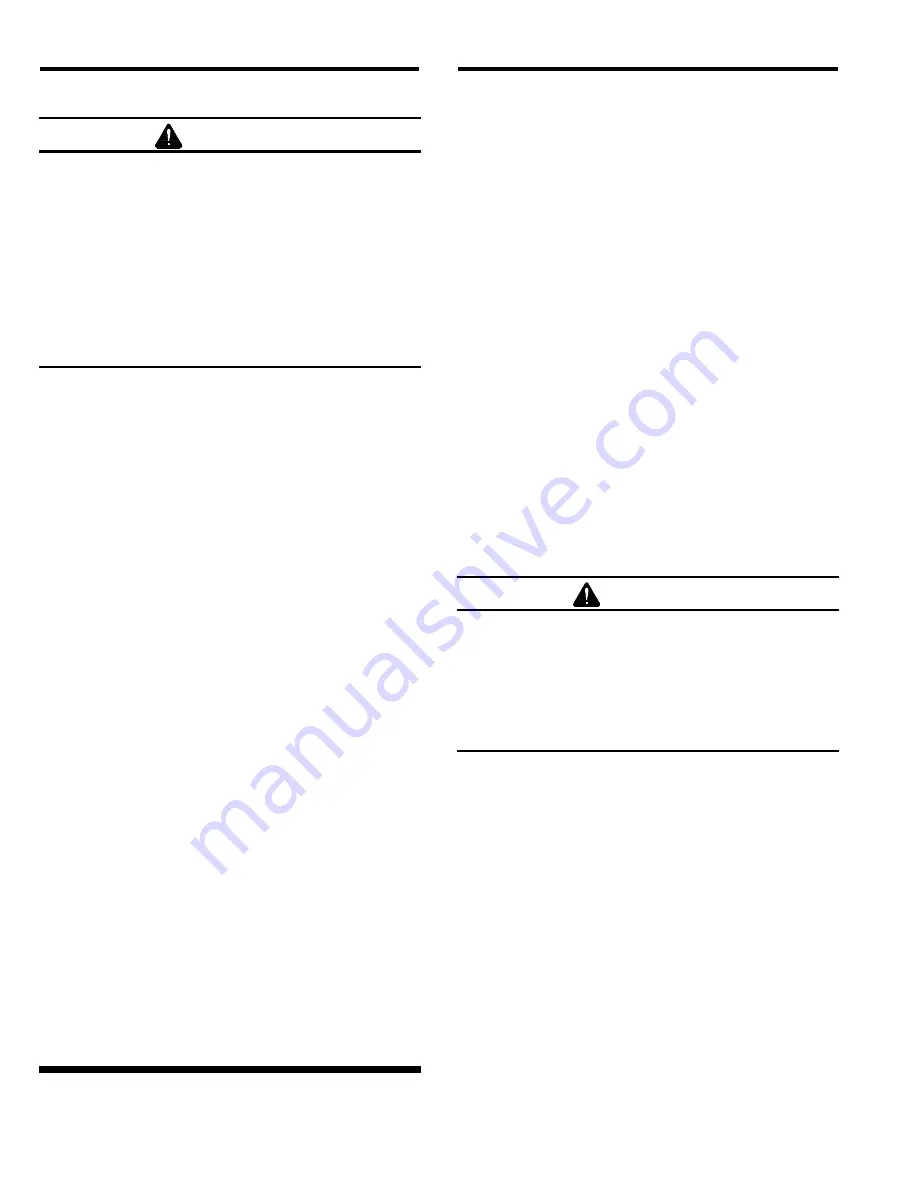
TLR-50 PNEUMATIC REMOTE CONTROLS
Page 6
© 2013 CLEMCO INDUSTRIES CORP.
www.clemcoindustries.com
Manual No. 03358 Rev. I
WARNING
OSHA requires the use of remote controls on all
blast machines when an operator controls the
nozzle. To comply with OSHA regulations, the
remote control handle, which starts and stops
the flow of air and abrasive, must be held down
manually. Do not tie down the control handle
lever or attempt to bypass any part of the remote
control system. Doing so will defeat the purpose
of the fail-to-safe feature of the remote control.
Serious injury or death could result from
uncontrolled blasting. Ref. 29 CFR 1910.244 (b).
3.5 Stop
Blasting
3.5.1
To stop blasting, release the control handle
lever. The pop-up valve automatically drops when air is
expelled from the machine and pressure equalizes.
3.5.2
When the control handle lever is released, the
safety lever-lock will flip up to lock the handle lever in the
up (no blast) position. Make sure the safety lever-lock is
up to prevent the handle lever from engaging.
3.5.3
Always open the safety petcock during work
breaks and before filling the blast machine. Opening the
petcock prevents unintentional blasting.
3.5.4
When finished blasting, shutdown per Section
3.6.
3.6 Shutdown
3.6.1
Empty the blast machine.
3.6.2
When finished blasting, and after cleanup is
completed, remove the respirator outside the respirator-
use area where the air is safe to breathe.
3.6.3
Close the compressed-air supply valve at the
compressor.
3.6.4
Drain receiver tank, filters, and water collecting
devices, and bleed the compressed-air supply hose.
3.6.5
Shutdown the compressor.
3.6.6
Cover the blast machine when not in use.
4.0 PREVENTIVE
MAINTENANCE
NOTE: These preventive maintenance instructions
pertain to the remote controls only. Also read the
manuals for the blast machine and all accessories, for
maintenance schedules of that equipment.
4.1 Daily
Inspection
4.1.1
With the air off, before blasting, do the following:
Make sure couplings are secure and lock pins and
safety cables are in place.
Inspect the RLX control handle; look for the
following:
The lever must not seal the opening on the
control unless the safety lever lock is pulled
down.
The
handle lever
must return to the "up"
position when released.
The
safety lever lock
must return to the "up"
position when the handle lever is released.
Both the handle lever and safety lever lock must
move freely with no drag or binding.
WARNING
Malfunctioning control handles could cause
unintentional actuation of a blast machine, or
prevent a machine from deactivating upon
release. Malfunctioning control handles must
be taken out of service immediately and
repaired or replaced. Serious injury or death
could result from unintentional blasting.
4.1.2
During blasting, do the following:
Check the control handle for leaks.
Inspect all control hoses, and valves for leaks. If
leaks are found, stop blasting and repair.
4.2 Periodic
Inspection
4.2.1
The remote control system is a safety device.
For safety and to avoid unscheduled down-time,
periodically inspect the internal parts of the inlet valve
and outlet valve. Inspect for wear and lubrication of o-
rings, pistons, condition of springs, seals, and castings.
Refer to Service Maintenance in Section 5.
4.2.2
The control handle is the actuator of the remote
control system. Periodically clean around the springs,
handle lever, and safety lever lock to ensure that the unit