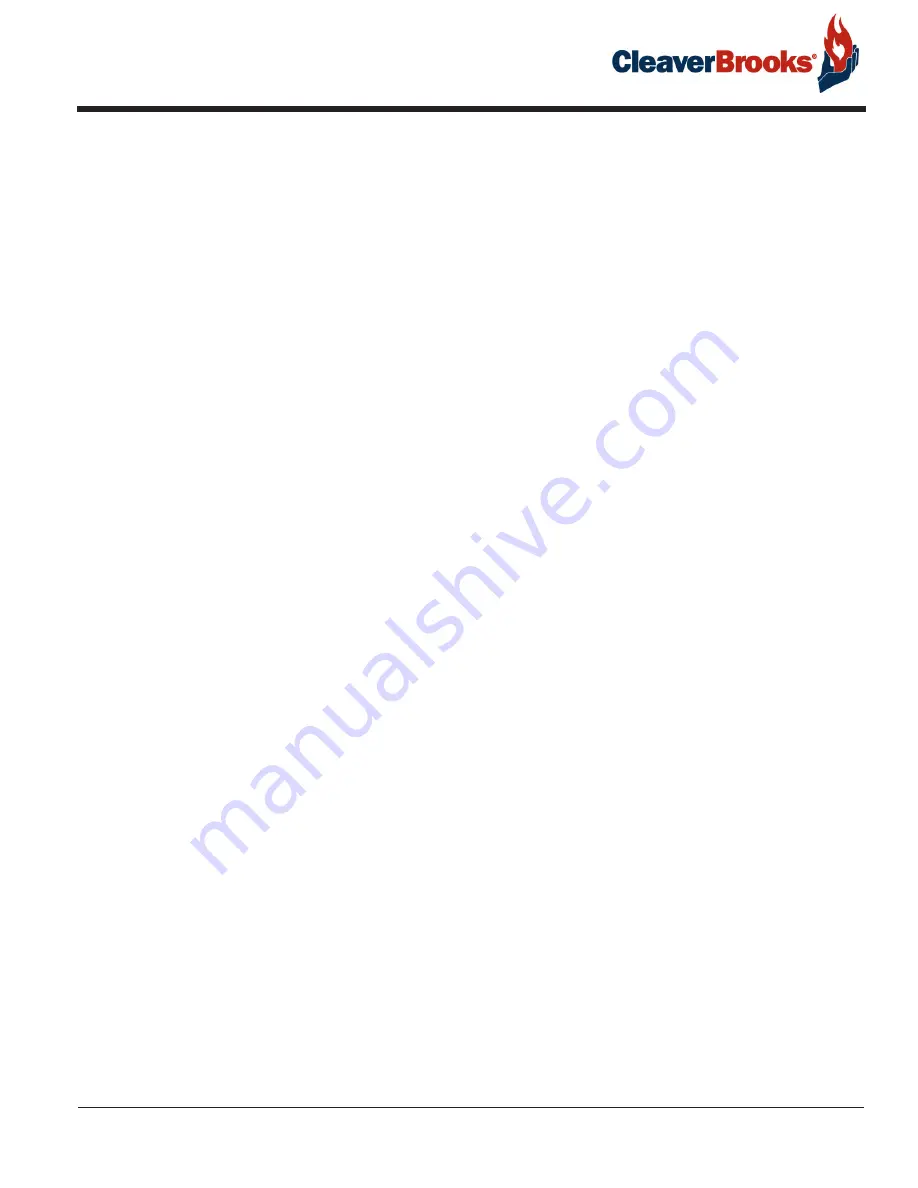
750-370
ProFire Q Series Manual
Warranty Policy
Limited Warranty:
The Company warrants that at the time of shipment, the equipment manufactured by it shall be
merchantable, free from defects in material and workmanship and shall possess the characteristics represented in
writing by the Company. The Company's warranty is conditioned upon the equipment being properly installed and
maintained and operated within the equipment's capacity under normal load conditions with competent supervised
operators.
Equipment, accessories, and other parts and components not manufactured by the Company are warranted only to the
extent of and by the original manufacturer's warranty to the Company. In no event shall such other manufacturer's
warranty create any more extensive warranty obligations of the Company to the Buyer than the Company's warranty
covering equipment manufactured by the Company.
Exclusions From Warranty:
(I) THE FOREGOING IS IN LIEU OF ALL OTHER WARRANTIES, ORAL OR
EXPRESS OR IMPLIED, INCLUDING ANY WARRANTIES THAT EXTEND BEYOND THE DESCRIPTION OF
THE EQUIPMENT. THERE ARE NO EXPRESS WARRANTIES OTHER THAN THOSE CONTAINED HEREIN
TO THE EXTENT PERMITTED BY THE LAW. THERE ARE NO IMPLIED WARRANTIES OF FITNESS FOR A
PARTICULAR PURPOSE. THE PROVISIONS AS TO DURATION, WARRANTY ADJUSTMENT AND
LIMITATION OF LIABILITY SHALL BE THE SAME FOR BOTH IMPLIED WARRANTIES (IF ANY) AND
EXPRESSED WARRANTIES.
(II) The Company's warranty is solely as stated in (a) above and does not apply or extend, for example, to: expendable
item; ordinary wear and tear; altered units; units repaired by persons not expressly approved by the Company; materials
not of the Company's manufacture; or damage caused by accident, the elements, abuse, misuse, temporary heat,
overloading, or by erosive or corrosive substances or by the alien presence of oil, grease, scale, deposits or other
contaminants in the equipment.
Warranty Adjustment:
Buyer must make claim of any breach of any warranty by written notice to the Company's
home office within thirty (30) days of the discovery of any defect. The Company agrees at its option to repair or
replace, BUT NOT INSTALL, F.O.B. Company's plant, any part or parts of the equipment which within twelve (12)
months from the date of initial operation but no more than eighteen (18) months from date of shipment shall prove the
Company's satisfaction (including return to the Company's plant, transportation prepaid, for inspection, if required by
the Company) to be defective within the above warranty. Any warranty adjustments made by the Company shall not
extend the initial warranty period set forth above. Expenses incurred by Buyer in replacing or repairing or returning the
equipment or any part or parts will not be reimbursed by the Company.
Spare and Replacement Parts Warranty Adjustment:
The Company sells spare and replacement parts. This
subparagraph (10.4) is the warranty adjustment for such parts. Buyer must make claim of any breach of any spare or
replacement parts by written notice to the Company's home office within thirty (30) days of the discovery of any
alleged defect for all such parts manufactured by the company. The Company agrees at its option to repair or replace,
BUT NOT INSTALL, F.O.B. Company's plant, any part or parts or material it manufacture which, within one (1) year
from the date of shipment shall prove to Company's satisfaction (including return to the Company's plant,
transportation prepaid, for inspection, if required by the Company) to be defective within this part warranty. The
warranty and warranty period for spare and replacement parts not manufactured by the company (purchased by the
Company, from third party suppliers) shall be limited to the warranty and warranty adjustment extended to the
Company by the original manufacturer of such parts; In no event shall such other manufacturer's warranty create any
more extensive warranty obligations of the Company to the Buyer for such parts than the Company's warranty
Summary of Contents for profire q
Page 2: ......
Page 12: ......
Page 22: ...Introduction 1 6 750 370 ProFire Q Series Manual...
Page 48: ...Maintenance 5 6 750 370 ProFire Q Series Manual...
Page 54: ...750 370 ProFire Q Series Manual...
Page 57: ......
Page 58: ...e mail info cleaverbrooks com Web Address http www cleaverbrooks com...