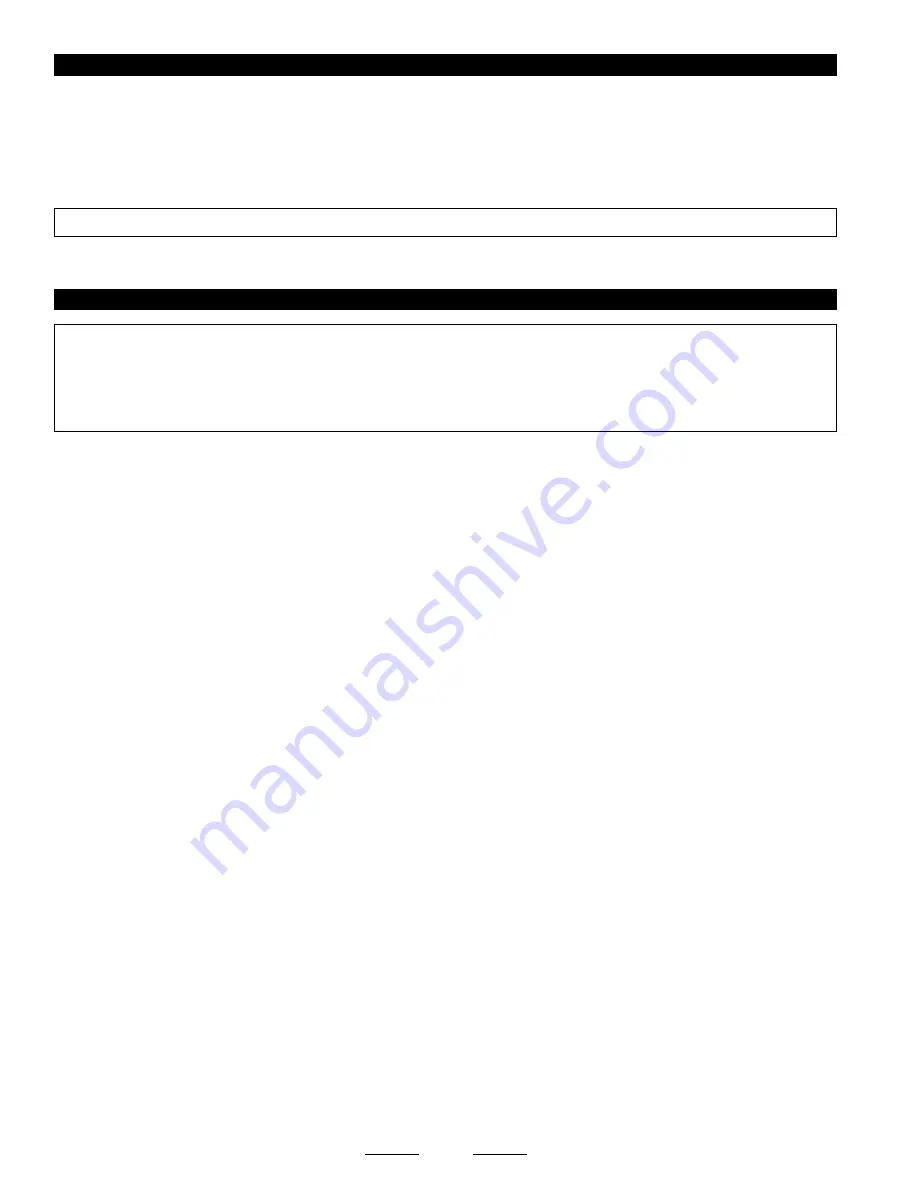
40
STEP 3: INSTALLING THE ESC
❑
If your ESC and motor do not use compatible connectors that can be plugged into each other, carefully solder the motor wires
to the motor wires on your ESC, being careful that the polarity is correct. Make sure to use heat-shrink tubing to insulate the
solder joints.
❑
Install your ESC into the fuselage as far forward as possible. Use a piece of double-sided tape or Velcro to hold the ESC
firmly in place.
✦
✦
✦
✦
✦
IMPORTANT
✦
✦
✦
✦
✦
Mount the ESC as far forward as conveniently possible to help balance the airplane.
❑
If your ESC features a micro switch, mount it in a convenient place on the side of the fuselage.
STEP 4: INSTALLING THE FLIGHT BATTERY
If you are using a LiPO flight battery, the LiPO flight battery that you choose MUST be able to handle the current draw
of your motor, gear box and propeller combination. Before charging or otherwise using your LiPO battery pack, please
read all warnings included with it.
Smaller capacity LiPO flight batteries may be too light to balance the airplane properly. In this case, it may be necessary
to add some nose weight.
❑
Install your flight battery into the fuselage using your favorite method to secure it into place. You will need to mount your flight
battery in the best location to balance the airplane. We have included two plywood plates that can be cut to length and glued
between the fuselage sides to mount your flight battery to.
❑
After installing your flight battery, complete step # 1 on page # 34 to install the hatch cover. You can then continue with mounting
your receiver and balancing the airplane.