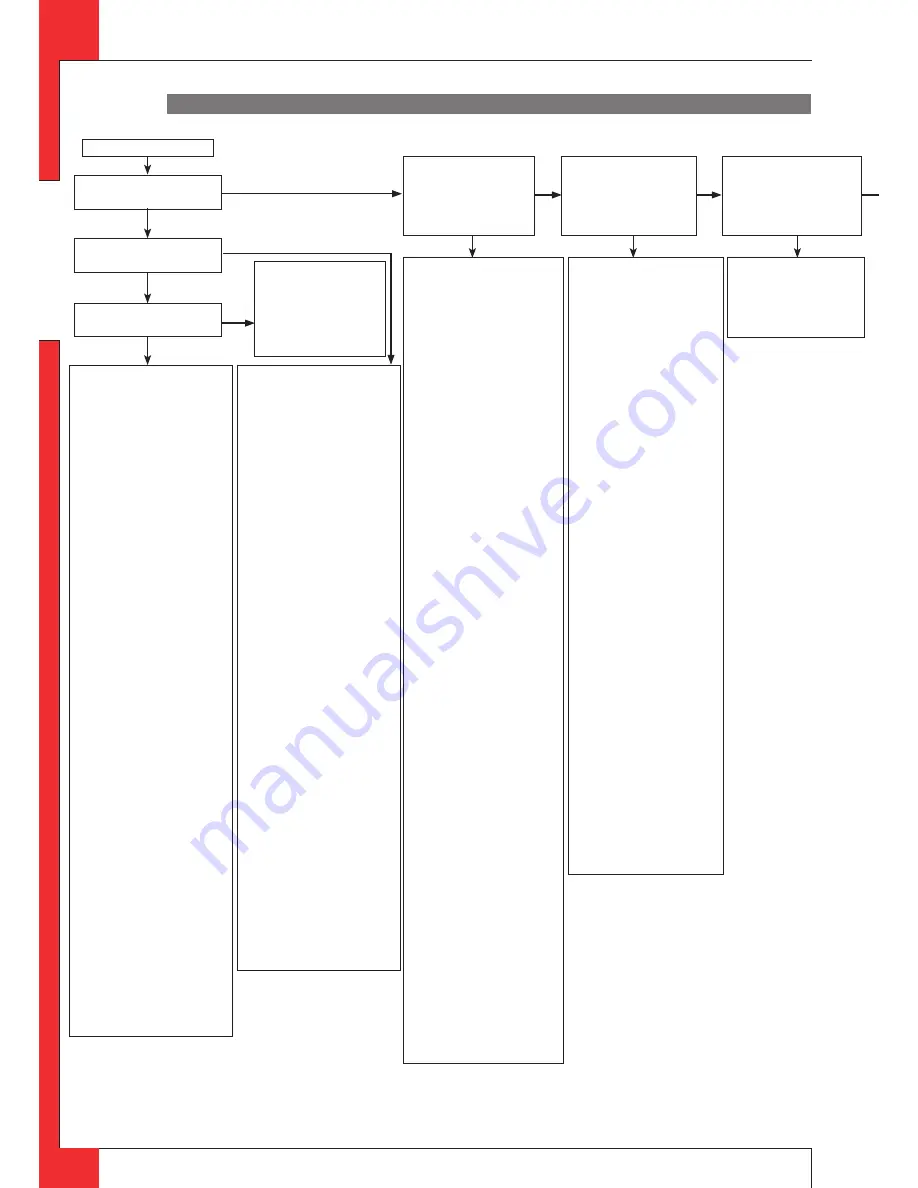
English
INS TA L L ATI O N M A NU A L
yes
Start
2.01 Can pilot be lit?
2.03 Only one spark?
2.02 Sparking?
2.09 Ignition procedure
-
Oval knob on gas control is
on "MAN". Set to "ON" and
restart.
Retarded ignition of main burner
Gas to main burner opens ca. 3-5
seconds after servo motor
operating the gas valve starts
running (sound of motor!). After
this the main burner is to ignite (at
least partially) within 10 seconds
and not with a firm noise WHOOF.
If not: no or delayed cross lighting
of main burner.
Hazardous situation. Stop ignition
procedure straight away and first
check for:
-
Position of logs or pebbles
-
Burner holes (locally)
blocked. Remove vermiculite
dust.
-
Vermiculite missing
-
Chips on burner
-
Vermiculite not distributed
evenly across burner(s)
PowerVent® (if present)
Consult PowerVent® installation
manual how to carry out the checks
below.
Check:
-
230V to fan controller unit
and fan
-
Silicon pressure
measurement hoses
swapped
leaking or barred
-
Pressure difference set too
high
-
Resistance of flue system too
high
adjustment of appliance
damper and air inlet guides)
flue length or number of
bends too large
dirty (e.g. cobwebs)
-
Operation of the fan
-
Operation of solenoid gas
valve
-
Operation of fan controller
unit
-
Operation of pressure
measurement gauge
2.11 No proper cross lighting
of main burner(s)
Go to box 2.09 and take
actions act as described for
'retarded ignition of main
burner'.
2.06 Pilot can be lit.
Does it stay alight?
2.10 Do(es) main burner(s)
ignite smoothly and across
its/their full length after after
first ignition by pilot burner?
2.08 Does main burner ignite
immediately?
2.04 Check:
Receiver
-
Replace missing, weak or
rechargeable batteries (not
enough power to open
thermoelectric valve)
Presence of gas on pilot burner
Check pilot on presence of gas at
normal ignition cycle or in Manual
Mode (turn oval knob on gas control
to MAN and keep safety shut off
valve opened with a screwdriver) and
ignite pilot with a lighter.
-
Pilot flame not on: Step 1
-
Pilot flame on: Step 2
Step 1: Pilot has no gas
-
Gas tap open?
-
Gas at gas control (line
pressure at measuring point on
gas control).
-
Check presence of gas at pilot
burner, by igniting in Manual
mode:
Turn oval knob on gas control
on MAN, open safety shut off
valve with a screwdriver and
try to ignite pilot with a lighter.
Not alight, then check the
following:
-
Blocking of pilot tube (kink or
dirt)
-
Gas flowing out of gas control?
(by loosening pilot tube at gas
control)
-
If not: check adjustment screw
pilot flame (under black cover):
sealing not to be broken.
Sealing broken: screw should
be fully open.
-
If this does not help: replace
gas control
Step 2: Pilot has gas, but no
ignition
-
Electrode with 90° bended tip:
bend tip 1mm higher
-
Spark too weak (thin and
reddish). Act as if 'no spark' in
box 2.05 and perform actions
described for ignition cable
and ignition electrode.
-
Pilot flame too weak (dirty).
Remove injector (remove
gland nut and the pilot tube).
See that it does not fall away.
Clean with compressed air.
Rectify. Retry.
2.05 Check:
Ignition cable
-
Present and connected
-
Being free from metal parts or
concrete
-
Too long: cut away all
excessive length at receiver
end, and reconnect
-
Shorting out to earth; replace
ignition cable.
-
Spark in wrong position
-
slide rubber sleeve on ignition
cable over ceramic of
electrode.
-
Replace electrode if
neccessary.
Ignition electrode
-
Straight electrode:
-
oxidation (roughen electrode
with file or sand paper)
-
position 4 mm from pilot
burner
-
Cracks in ceramic (not always
visible), replace electrode.
Thermocouple circuit interrupted
-
Check connection between:
-
thermocouple and interruptor
-
interruptor and gas control
Is it tight? (han half a
turn)
-
Black wires (yellow/red end)
not (well) connected in
thermocouple interruptor, in
right position on receiver (in
right position)
-
Thermocouple broken inside
thermocouple interruptor:
Replace.
-
Thermocouple interruptor
defective.
Check by screwing
thermocouple directly in gas
control and ignition in Manual
mode (see 2.04))
Starting procedure
After switching off/going out the
remote is locked for 120 sec. (older
versions 60 sec).
Wait 2 minutes before reigniting.
2.07 Check thermocouple system
Step 1: Check pilot flame and
thermocouple
-
Pilot flame too small
-
pilot dirty. Rectify (see 2.04)
-
check for pilot gas tube
tightness
-
pilot tube kinks or dirt inside
-
line pressure too low
-
tip not in (correct!) pilot flame.
Bend into flame.
Step 2: Check circuit for
interruptions or short circuiting
-
thermocouple tight in
interruptor
-
interruptor tight in gas control
-
black wires (yellow/red end)
-
connected to inter
receiver
-
short circuitiong at interruptor
Step 3: Check receiver
Dismount black-red and -yellow
control cables from receiver and link
together. Ignite fire in Manual Mode
(see 2.04, light pliot with a
matchlight):
-
Pilot stays on: the receiver is
defective (replace) , and the
rest of the thermocouple
system is OK.
-
Pilot goes out: Step 4.
Step 4: Check thermocouple and
gas control
Screw thermocouple directly in gas
control and light in Manual Mode
(see 2.04, light pliot with a
matchlight):
-
Pilot stays on: Thermocouple
interruptor defective.
-
Pilot goes out:
-
thermocouple defective
-
thermo-electric device
defective
Go to step 5.
Step 5: Check thermocouple
Check thermocouple by replacing or
by measuring output voltage
(>5mV, with thermocouple
connected). See Appendix 3, fig. 42.
Step 6
If thermocouple is not the cause the
themo-electric device is defective.
Replace gas control.
8-Wire black control cable
-
8-wire cable between receiver
and gas control not
connected.
-
Poor contact of connector.
Check for pins on receiver not
being bended.
-
One of eight wires loose in
connector.
Check by pulling wire by wire at
both ends of cable)
yes
no
yes
yes
no
no
no
no
no
Fires with electronic ignition, fault finding: Ignition and burning
Appendix 1 diagnosis of malfunctions
GB
UK
2.03a
-
Loosen and retighten
earthing screw on gas
control.
-
If this does not work:
replace receiver.
yes
Summary of Contents for G20
Page 28: ...E n g l i s h INSTALLATION MANUAL UK 38c 1780 1 B Q T 38c 1778 S C D 4x K 38c 1779 7 5 6 ...
Page 29: ...E n g l i s h INSTALLATION MANUAL UK 38c 1781 1 G A H P 38c 1783 38c 1782 E F R 6x 9 8 10 ...
Page 30: ...E n g l i s h INSTALLATION MANUAL UK A A 38c 1784 A A 38c 1785 G H I L 12 11 ...
Page 31: ...E n g l i s h INSTALLATION MANUAL UK 38c 1786 L J R 38c 1787 14 13 ...
Page 33: ...E n g l i s h INSTALLATION MANUAL UK A B C D 38P 0267 0 38P 0268 A 38P 0269 B 22 21 23 ...
Page 34: ...E n g l i s h INSTALLATION MANUAL UK 38P 0270 C 38P 0271 D 25 24 ...