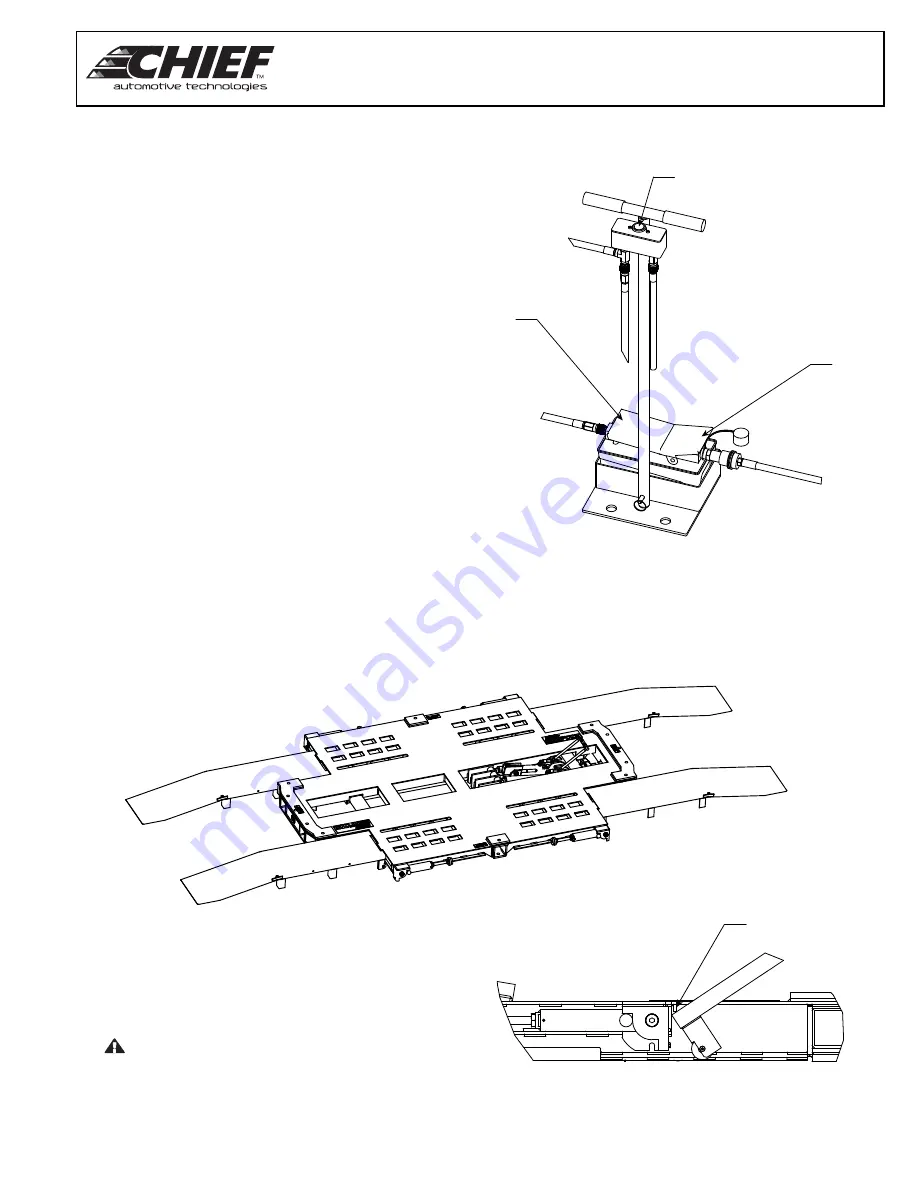
9
EZ LINER EXPRESS
USERS MANUAL
6. Disengage the Safety Latch by pressing the Release Button
on the Air Valve on the Pump Stand. And lower the lift
completely by pressing the release portion on the pedal of
the Lift Pump (see Figure 16).
Release Button
Pump
Release
Figure 16
Figure 17
Figure 18
IV. Locate Ramps
1. Roll a Ramp to each of the four corners of the lift (see Figure 17).
2. Hook Ramps to the Lift Mainframe by hooking the tab from
Mainframe into slot on the Ramp (see Figure 18).
Tip: To aid in locating the ramps when reinstalling
the ramps while preparing to unload the vehicle
from the lift, you may want to mark the floor with
the location of the ramps.
Tab For Hooking Ramps
Summary of Contents for EZ LINER EXPRESS
Page 1: ...2013 Vehicle Service Group USERS MANUAL EZ LINER EXPRESS ...
Page 30: ...NOTES ...
Page 31: ...NOTES ...