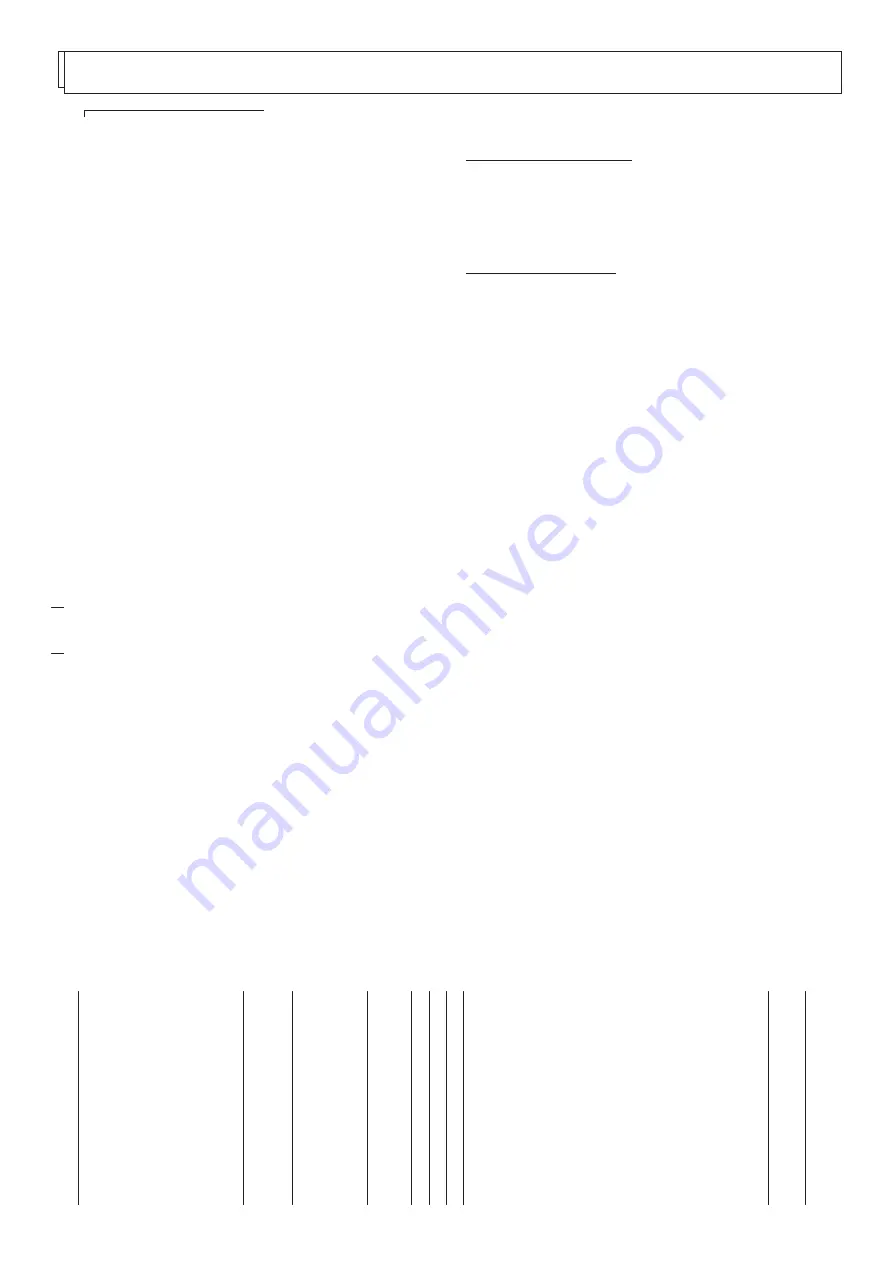
59
100
BURNER ASSEMBLY
101
BURNER 24KW
61313760
.
BURNER 30KW
61313763
.
BURNER 35KW
61314834
.
200
FAN ASSEMBLY
204
TEMPERATURE PROBE
990686
...
231
GASKET D:129.4
61306030
...
400
GAS SECTION
401
GAS SECTION ASSY
61307584
.
GAS SECTION ASSY
61310129
.
GAS SECTION ASSY
61315410
.
407
FAN ASSY
61314434
...
500
HYDRAULIC BLOCK
507
OVERHEAT THERMOSTAT 100°C
61010572
...
531
AIR SEPARATOR HEAD ASSEMBLY
61304608
...
532
GASKET KIT
61304618
...
537
PRESSURE RELIEF VALVE
61312668
...
538
PUMP + AIR SEPARATOR 15/50
61301964
...
PUMP + AIR SEPARATOR 15/60
61303461
...
554
PRESSURE SENSOR 0.8B
61310364
...
700
ELECTRICAL BOX
705
PRESSURE GAUGE
61313561
...
707
PRINTED CIRCUIT BOARD
65102353
...
PRINTED CIRCUIT BOARD ADJUST.
61312782
...
PRINTED CIRCUIT BOARD CONNECT.
61314958
...
709
IGNITER
61002105-20
...
Description
Key N°
Manf. Pt. N°
Type
G.C N°
FF
Manf. date
from to
M
IN
IM
A
H
E
24
FF
M
IN
IM
A
H
E
30
FF
M
IN
IM
A
H
E
35
Description
Key N°
Manf. Pt. N°
Type
G.C N°
FF
Manf. date
from to
M
IN
IM
A
H
E
24
FF
M
IN
IM
A
H
E
30
FF
M
IN
IM
A
H
E
35
Description
Key N°
Manf. Pt. N°
Type
G.C N°
FF
Manf. date
from to
M
IN
IM
A
H
E
24
FF
M
IN
IM
A
H
E
30
FF
M
IN
IM
A
H
E
35
Description
Key N°
Manf. Pt. N°
Type
G.C N°
FF
Manf. date
from to
M
IN
IM
A
H
E
24
FF
M
IN
IM
A
H
E
30
FF
M
IN
IM
A
H
E
35
Description
Key N°
Manf. Pt. N°
Type
G.C N°
FF
Manf. date
from to
M
IN
IM
A
H
E
24
FF
M
IN
IM
A
H
E
30
FF
M
IN
IM
A
H
E
35
Description
Key N°
Manf. Pt. N°
Type
G.C N°
FF
Manf. date
from to
M
IN
IM
A
H
E
24
FF
M
IN
IM
A
H
E
30
21. Maintenance Instructions
21.1 General remarks
It is recommended that the following inspections be carried
out on the boiler at least once a year;
1. Check the seals in the water group, and if necessary,
replace the gasket and restore the seal to perfect working
order;
2. Check the seals in the gas group, and if necessary
replace the gaskets and restore the seal to perfect
working order;
3. Visually check the overall condition of the boiler;
4. Visually check the combustion, and if necessary,
disassemble and clean the burner;
5. Following inspection 3, disassemble and clean the
combustion chamber as necessary;
6. Following inspection 4, disassemble and clean the
injector, if necessary;
7. Clean the primary heat exchanger. (see Section 21.2);
8. Check and adjust the CO
2
emissions as necessary (see
Section 14.3);
9. Check the correct operation of the heating safety devices:
- Overheat thermostat
10. Check the correct operation of the low water pressure
switch;
11. Check the correct operation of the gas group safety
devices:
- absence of gas or flame safety device (ionisation);
12. Check that the electrical connections are correct (as
described in Section 13, page 26);
13. Check the efficiency of the production of domestic hot
water (test the flow rate and temperature rise);
14. Carry out a general inspection of the boiler;
15. Check the flue and termination point;
16. Remove any oxide from the detection electrode by using
an emery cloth.
21.2 Cleaning the primary exchanger
Cleaning the exhaust side
Remove the air gas assembly (Section 18.2.1). Check that
the exhaust passages are free, if there are deposits present,
clean the exchanger with compressed air or wash with water
or a vinegar based detergent.
Cleaning the water side
Use detergents that dissolve CaCO3. Leave to act for a
short time and then rinse.
Make sure that the detergent does not remain inside the
exchanger.
Remove the condensate trap and clean it. Fill it with water
and reassemble.
21.3 Operational test
After servicing the boiler, fill the heating circuit to a pressure
of approximately 1.5 bar and release the air from the system.
-
Place the boiler in operation;
-
If necessary, release the air again from the heating
system;
-
Check the settings, seals and the correct functioning of
the system for expelling the products of combustion and
drawing combustion air;
-
Check the settings and correct operation of all the
control, regulation and monitoring components;
-
Check that the burner ignites properly and carry out a
visual check of the burner flame;
-
Check that the 3 bar safety valve is operating correctly;
-
Check the operation of the time control and room
thermostat (if fitted);
-
Complete the Service Interval Record (Section 25, page
36)
N
OTE
: T
HESE CHECKS ARE NOT EXHAUSTIVE
Summary of Contents for Minima HE System 24 Nat
Page 19: ...19 1 2 A A Fig 14 Fig 16 Fig 13 11 Installing the Boiler continued Fig 15 P P ...
Page 22: ...22 Fig 21 Fig 22 Fig 23 ...
Page 31: ...31 WIRING DIAGRAM FOR CONNECTION TO AN OPEN VENTED CYLINDER DIAGRAM B ...
Page 32: ...32 WIRING DIAGRAM FOR CONNECTION TO AN MTS UNVENTED CYLINDER DIAGRAM A ...
Page 61: ...61 24 Benchmark Commissioning Checklist ...
Page 62: ...62 25 Service Interval Record ...
Page 63: ...63 ...