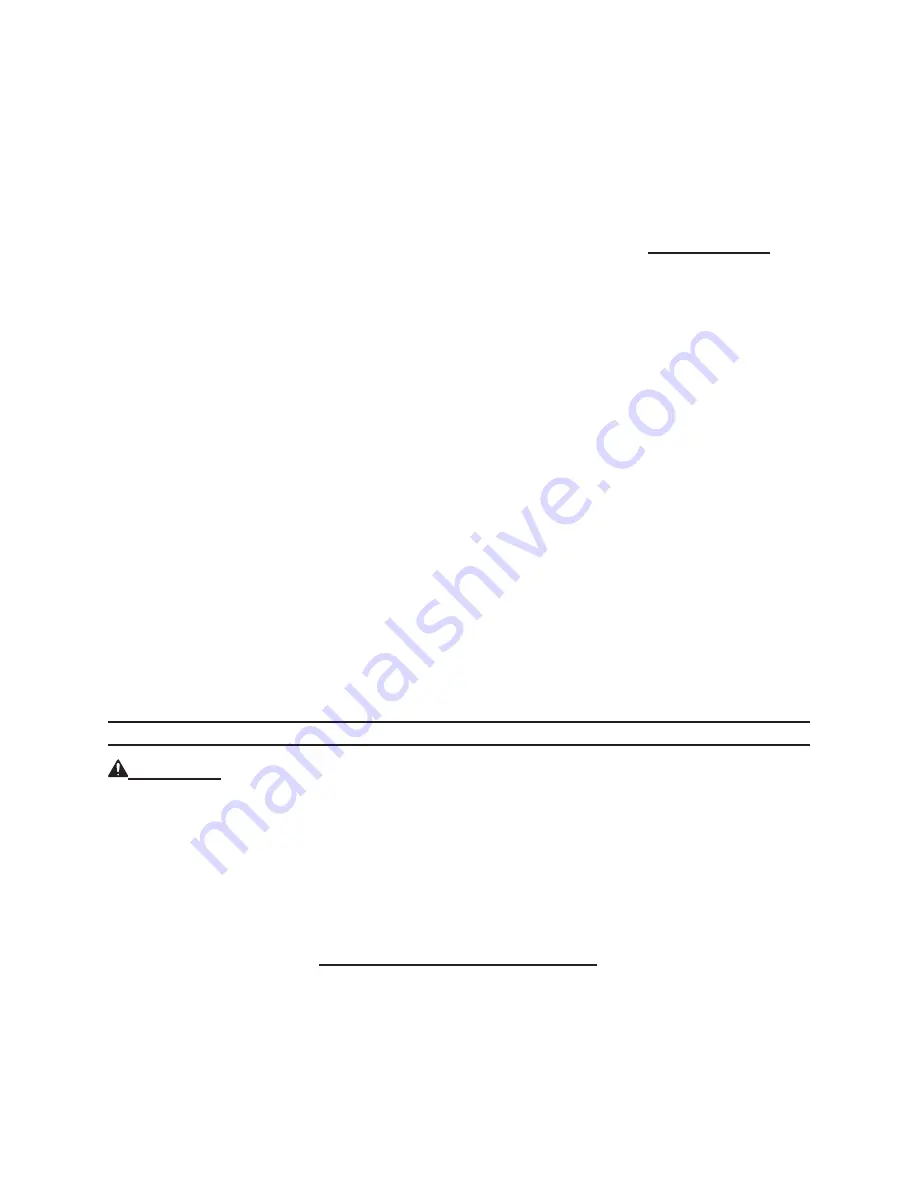
Page 17
SKU 90589
For technical questions, please call 1-800-444-3353.
While the wheel/tire is still clamped onto the Turntable (201), depress the Inflation
3.
Pedal (IT106) completely while slightly raising and lowering the tire by hand to
contact the beads on both sides of the tire with the edges on both sides of the
wheel rim. Meanwhile, air is being released from the inflation jet nozzles on
the Turntable, expanding the tire until the beads on both sides make complete
contact with the full circumference of the wheel rim on both sides and seal the
beads to the edges of the wheel rim.
(See Figures A and F, previous page.)
Immediately when there is an air tight seal between the beads on both sides and
4.
wheel rims on both sides release pressure on the Inflation Pedal (IT106).
(See Figure A.)
Attach the Nozzle of the air hose to the valve stem of the tire. Make sure the
5.
Locking Lever of the Nozzle is in the “UP” position to lock the Nozzle onto the
valve stem.
(See Figure F.)
Depress the Air Inflator Button. Depress the Inflation Pedal (IT106) down to its
6.
middle position to release air from the air hose.
(See Figures A and F.)
Remember to inflate the tire with brief jets of air, checking the air pressure
7.
frequently. Once the proper air pressure has been reached, release pressure on
the Inflation Pedal (IT106). Disconnect the nozzle of the air hose from the valve
stem of the tire, and screw a valve cap onto the stem.
(See Figures and F.)
Depress the Tilting Pedal (404) so the Vertical Column (101) will tilt back to its
8.
non-working position, release the clamping jaws and remove the wheel/tire from
the Tire Changer.
(See Figure A.)
INSpECTION ANd MAINTENANCE
WARNING!
prior to performing any inspection or maintenance procedures,
disconnect the Tire Changer from its air supply source. pump the bead
breaker pedal (402) several times to evacuate all compressed air from the
machine, and disconnect the unit from its electrical supply source.
before each use:
1.
Inspect the general condition of the Tire Changer. Check
for misalignment or binding of moving parts, cracked or broken parts, damaged
wiring, damaged air hoses, and any other condition that may affect its safe
operation. If abnormal noise or vibration occurs, have the problem corrected
before further use.
do not use damaged equipment.
daily:
2.
Clean the machine daily to remove any dirt or tire debris from the Jaw
Slides (202). Then, lubricate the Slides with grease.
At least once per week:
3.
Clean the Turntable (201) with detergent or a non-
flammable solvent. Then, lubricate the Jaw Slides (202) with grease.