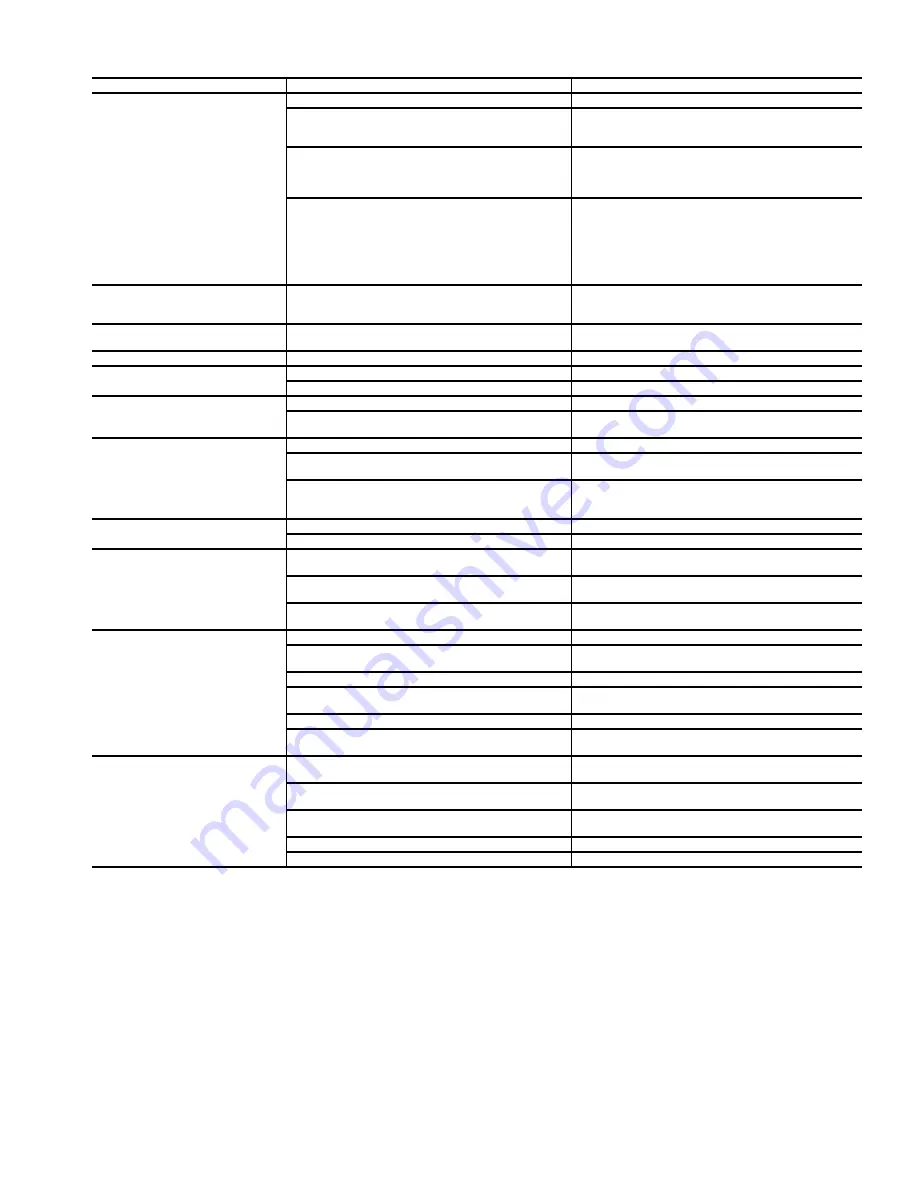
43
Table 15 — Variable Speed Head Pressure Control
LEGEND
PROBLEM
POSSIBLE CAUSE
SOLUTION
No fan operation
No 24V control voltage
Check for 24 VAC at control.
No input pressure to control
Check alignment of capillary fitting. Schrader valve
depressor must depress Schrader valve enough to
allow pressure into capillary.
Bad fan motor
Disconnect power. When P266 is used, place a
jumper from L1 to M1 and connect power. If fan
does not start, motor is bad and should be
replaced.
Pressure transducer problem
Disconnect 6 pin connector from right side of con-
trol. Place a jumper wire between third pin from the
top and bottom pin on the control (not the cable). If
fan goes to full speed, check for input pressure. If it
has been determined there is adequate pressure,
the transducer is bad and the control must be
replaced.
Fan stops when pressure
reached high end of operating
range.
Control is not wired correctly
See wiring diagrams.
No fan modulation
(on-off operation)
Control is not wired correctly
See wiring diagrams.
Fan starts at full speed
Control is not wired correctly
See wiring diagrams.
Erratic fan operation
Control is not wired correctly
See wiring diagrams.
Dirty or blocked condenser coil
Clean condenser coil.
Fan motor is cycling on thermal
overload
Dirty or blocked condenser coil
Clean condenser coil.
Wrong motor for fan speed control application
Replace with motor approved for fan speed control
application.
Erratic pressure control
Defective regulator
Replace defective part.
Dirt causing regulator to bind
Disassemble regulator and clean internal parts.
Install strainer.
Power source to hot gas solenoid or operation of
the solenoid is intermittent
Determine if problem is caused by supply voltage,
solenoid, or excessive MOPD. Make changes nec-
essary to correct problem.
Regulator leakage
Dirt in regulator causing seat to remain open
Clean regulator. Install strainer.
Worn or eroded seating surface on regulator
Replace defective part.
Regulator hunting (chattering)
with large fluctuations in con-
trolled pressures
Regulator is oversized
Contact a certified technician for correctly sized
regulator.
Regulator and liquid injection thermovalve have
control interaction
Increase superheat setting. Dampen bulb response
by repositioning.
Regulator and cylinder unloaders have control
interaction
Increase differential between the controls by lower-
ing the regulator’s setpoint.
Regulator will provide pressure
control
Regulator seat is restricted
Locate and remove stoppage. Install strainer.
Pressure adjusting stem is set at a point so high
that suction pressure never reaches the setpoint
Re-adjust the regulator.
Strainer clogged at the regulator inlet
Locate and remove stoppage.
MOPD exceeded across the solenoid or loss of
source voltage
Replace solenoid or troubleshoot the electrical
problem.
Solenoid coil burned out
Replace coil.
Wrong type of distributor for hot gas bypass to the
evaporator
Install proper Venturi-Flo™ type distributor for low
pressure drop.
Regulator fails to close
Dirt under seat of regulator
Locate and remove stoppage. Install strainer or fil-
ter drier.
Diaphragm failure (leakage around the adjusting
stem)
Replace defective parts.
Pressure adjusting stem is set at a point so high
that suction never reaches the setpoint
Re-adjust the regulator.
Blocked external equalizer passage
Locate and remove stoppage. Install strainer.
Worn or eroded regulator seat
Replace defective part.
MOPD —
Maximum Opening Pressure Difference