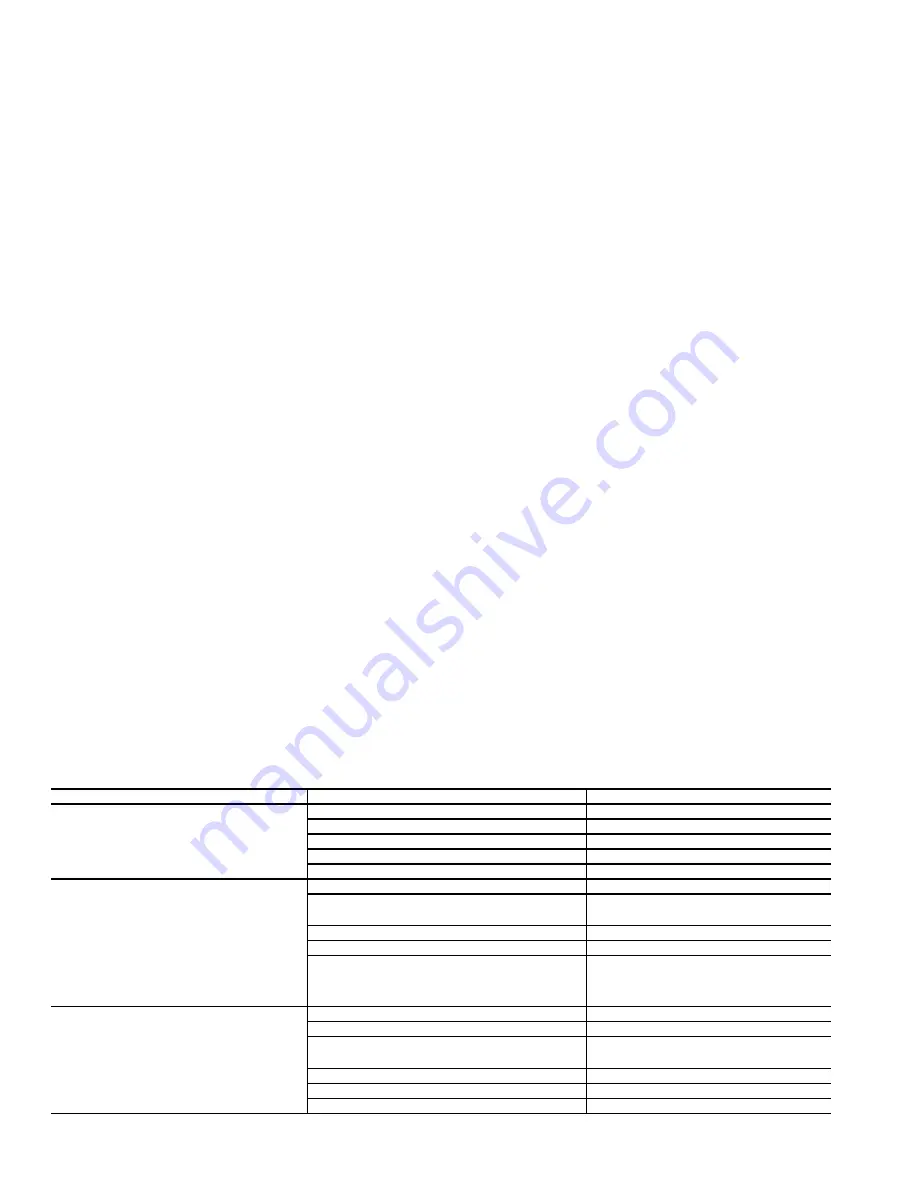
40
cessive pressure drop, then wheel cleaning should be per-
formed as follows:
1. Using a standard shop vacuum, vacuum any debris from
both faces of the wheel. Slowly work around the entire
face of the wheel to complete the procedure. Do not dam-
age wheel face by excessive pressure of the vacuum noz-
zle on the wheel face.
2. Using 20 psi clean, dry air and a small air nozzle, blow air
through one face of the wheel. At a similar location on the
opposite side of the wheel, gently apply a shop vacuum to
“receive” any remaining debris exiting the wheel. In the
event that this method does not remove visual buildup or
return pressure drop to within normal parameters, a wheel
washing procedure is recommended. The energy conser-
vation wheels can be washed thoroughly with water with-
out affecting the performance of the wheel. The wheel
will simply dry out following a washing procedure and
resume normal energy transfer without any deviation in
performance. If the energy conservation wheel can be
easily removed from the cassette or unit, it is recommend-
ed to do so to facilitate the washing process. However, in
most cases, it is impractical to remove larger wheels.
Therefore, the washing procedure must take place within
the air handling unit, and provisions need to be made to
collect the runoff water from the bottom of the unit or col-
lect the water by using a wet vac on the opposite side of
the wheel during the procedure.
3. Shield all electrical components and bearings with plastic
sheeting. Ensure that an adequate drainage system exists
to collect runoff water from the bottom of the unit. Alter-
natively, use a wet vac with a wide nozzle on the opposite
face of the wheel to collect the water during the washing
procedure.
4. Disable the drive motor.
5. Using standard pressure water (do not use a high pressure
washer) and working from the one side of the wheel,
wash the wheel with a standard “garden” nozzle to flush
any debris trapped within the flutes of the wheel. If de-
sired, a mild detergent can also be used to enhance clean-
ing without affecting the performance of the wheel.
Gas Heater
GAS LINE — Check for gas leaks.
MANUAL SAFETY SHUT OFF VALVE — Check for gas
leaks.
DIRECT SPARK IGNITER — Check for cracked ceramics,
excessive carbon residue, or erosion of the electrode. Replace
as required.
GAS VALVE — Check that gas valve seat is not leaking.
BURNERS — Soft brush or vacuum inside burner, at burner
ports, and at air inlet between burner and manifold pipe to
eliminate accumulation of lint and/or dirt.
HEAT EXCHANGER — Inspect for cracks, sagging, bend-
ing, or distortion. Clean with vacuum and/or stiff brush.
DRAFT INDUCER — Clean with compressed air or vacu-
um.
VENT PIPE/TERMINAL — Venting must be intact. Using a
flashlight, look for obstructions, cracks on the pipe, gaps in the
sealed areas, or corrosion. Clean vent terminal.
CONDENSATION DRAIN — Check for blockages.
Electric Heater Wiring and Wiring
Connections —
Check all wiring connections. Tighten as
necessary. Check internal wiring. Replace as necessary with
type THHN 221°F (105°C), 600V, 16-gauge wire or equiva-
lent.
CONTROL PANEL — Check heater control panel for dust/
dirt and moisture. Clean as necessary.
HEATING ELEMENTS — Check heating elements for dust/
dirt buildup and/or broken elements. Replace elements and/or
clean elements with low pressure air as necessary. Check ele-
ment male/female chassis insulators for breaks and/or cracks.
Replace as necessary. Check element support frame insulators.
Replace missing or broken insulators as necessary.
Filters —
Filters should be checked for dirt restriction on a
monthly basis (or as required). Replace filters with filters of
equal specification when they appear dirty.
TROUBLESHOOTING
See Tables 12-19 for possible causes and solutions to prob-
lems that may arise.
TROUBLESHOOTING
Table 12 — Supply Fan
PROBLEM
POSSIBLE CAUSE
SOLUTION
Blower motor does not run
Damper limit switch no closed or inoperative
Repair or replace switch.
Motor thermal overloads tripped
For tripped condition - reset.
Fuses blown or missing
Replace fuses.
External power source lacking
Have incoming power lines checked.
Motor inoperative
Repair or replace.
Blower motor runs, but fans do not supply
enough make-up air
Intake filters dirty
Replace or clean.
Obstruction in the intake
• Check dampers for proper operation
• Clear all intake passages of obstructions.
Fan wheel loose on shaft
Reposition and tighten.
Access doors and panels not closed
Close.
Excessive discharge resistance from
• Dirty filters in discharge
• External dampers.
Clean filters and/or re-adjust dampers.
Excessive fan noise
Fan motor bearing
Replace.
Fan wheel loose on shaft
Reposition and re-tighten.
Fan wheel rubbing
• Loosen setscrews.
• Reposition cone and tighten.
Fan wheel dirty
Clean.
Loose duct
Tighten or reinforce.
Foreign article in fan or duct
Remove.