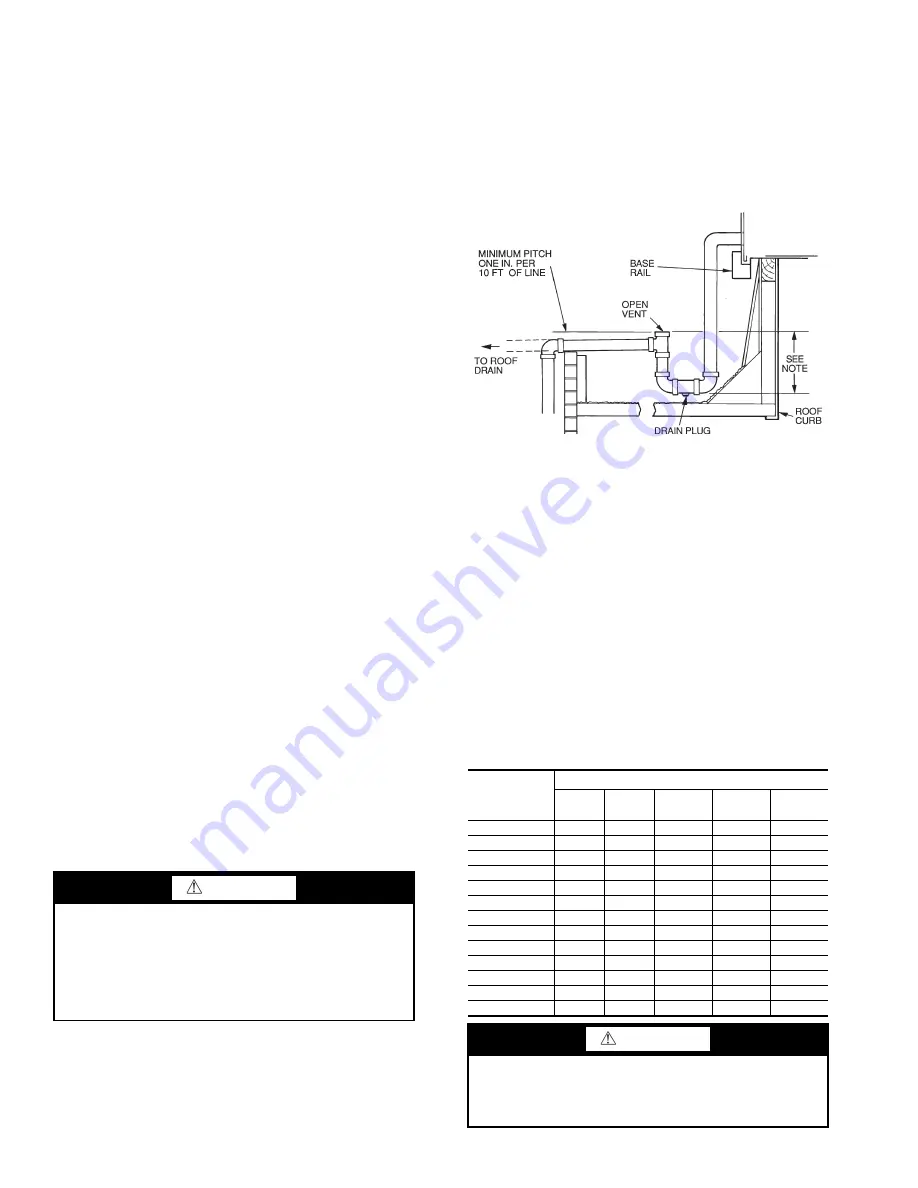
24
NOTE: For weight references, consult the DOAS Builder pro-
gram submittal.
Step 3 — Field Fabricate Ductwork —
On vertical
supply or return units, secure all ducts to roof curb and building
structure.
Do not connect ductwork to unit.
Insulate and weath-
erproof all external ductwork, joints, and roof openings with
counter flashing and mastic in accordance with applicable
codes.
Ducts passing through an unconditioned space must be
insulated and covered with a vapor barrier.
If a plenum return is used on a vertical unit, the return
should be ducted through the roof deck to comply with applica-
ble fire codes.
A minimum clearance is not required around ductwork. The
unit has been selected and ordered to operate at a specific air
volume and external static pressure. This external static pres-
sure is generated by any additional components that are added
to the air stream (ductwork, etc.). Additional static pressure,
beyond the original design, will affect the performance of the
packaged air conditioning unit and reduce the air volume that
can be delivered. Proper engineering methods must be used
when calculating external duct and component static pressure
losses.
Step 4 — Make Unit Duct Connections —
All
62XA, B, C, D, E, F, G, H, T, U, V, W, X, and Y units bring in
100% outdoor air through the outdoor air intake hood and do
not have a return air connection. The 62XA, B, C, D, T, U, and
V units have a vertical supply duct opening in the bottom of the
unit. The 62XE, F, G, H, W, X, and Y units have a horizontal
supply duct opening in the side of the unit.
All 62XJ, K, M, N, P, Q, R, S, Z, 2, 3, 4, 5, and 6 units bring
in 100% outside air through the intake hood and also have a re-
turn duct opening in the bottom of the unit for exhaust. They
will also be equipped with a factory-installed power exhaust
and may be equipped with an energy recovery ventilator
(ERV). and/or an energy conservation wheel. The return air to
these units is not re-circulated or mixed with the incoming out-
door air. The return air may be used to transfer energy to the in-
coming air via the energy recovery ventilator and is then ex-
hausted. The 62XJ, K, M, N, Z, 2, and 3 units have a vertical
supply and return duct opening in the bottom of the unit. The
62XP, Q, R, S, 4, 5, and 6 units have a horizontal supply duct
opening in the side of the unit and a vertical return opening in
the bottom of the unit. To determine the specifics regarding a
particular unit, see the model number nomenclature found in
the product data guide for the 62X unit.
VERTICAL SUPPLY/RETURN CONNECTIONS — For
vertical supply or return connections, ductwork openings are
shown in the DOAS Builder generated submittal. Attach the
ductwork to the roof curb. Do not attach duct directly to the
unit.
HORIZONTAL SUPPLY CONNECTIONS — For horizon-
tal supply connections, ductwork openings are shown in the
DOAS Builder generated submittal. The 62X units do not
have horizontal return connections.
Step 5 — Install External Trap for Condensate
Drain —
The unit’s
3
/
4
-in. condensate drain connection is lo-
cated on the side of the unit. Refer to the DOAS Builder gener-
ated submittal for condensate location.
All units must have an external trap for condensate drain-
age. Install a trap at least 4-in. deep and protect against freeze-
up. If drain line is installed downstream from the external trap,
pitch the line away from the unit at 1 in. per 10 ft of run. Do not
use a pipe size smaller than the unit connection. Refer to the
physical data table for sizes. See Fig. 9.
Step 6 — Install Gas Piping (Gas Heat Units
Only) —
Unit is equipped for use with natural gas. Gas heat
units to come with factory installed cabinet knockout for gas
piping connection. Refer to local building codes, or in the ab-
sence of local codes, to ANSI Z223.1-latest year and adden-
dum Z223.1A-latest year entitled HFGC. In Canada, installa-
tion must be in accordance with the CAN1.B149.1 and
CAN1.B149.2 installation codes for gas burning appliances.
Gas piping length and capacity is shown in Table 5. See
Fig. 10 for typical pipe guide and locations of external manual
gas shutoff valve. Gas supply piping must be supported starting
from connection of the unit. If long stretches of piping are ex-
pected to be used, there must be supports at intervals of every 6
to 8 ft. Metal straps, blocks, or hooks are acceptable to support
the gas piping. The piping should never be strained or bent.
Table 5 — Gas Piping Capacity (cubic ft per hr)
WARNING
For vertical supply and return ductwork, tools or parts
could drop into ductwork and cause an injury. Install a
90-degree turn in the return ductwork between the unit and
the conditioned space. If a 90-degree elbow cannot be
installed, then a grille of sufficient strength and density
should be installed to prevent objects from falling into the
conditioned space.
GAS
PIPE
LENGTH
(FT)
PIPE SIZE (IN.)
3
/
4
1
1
1
/
4
1
1
/
2
2
10
278
520
1050
1600
2700
20
190
350
730
1100
2100
30
152
285
590
890
1650
40
130
245
500
760
1450
50
115
215
440
670
1270
60
105
195
400
610
1105
70
96
180
370
560
1050
90
84
160
320
490
930
100
79
150
305
460
870
125
72
130
275
410
780
150
64
120
250
380
710
175
59
110
225
350
650
200
55
100
210
320
610
WARNING
Do not pressure test gas supply while connected to unit.
Always disconnect union before servicing. High pressures
can cause gas valve damage resulting in a hazardous
condition.
Fig. 9 — Condensate Drain Piping Details
NOTE: Trap should be deep enough to offset maximum unit static
difference. A 4-in. trap is recommended.