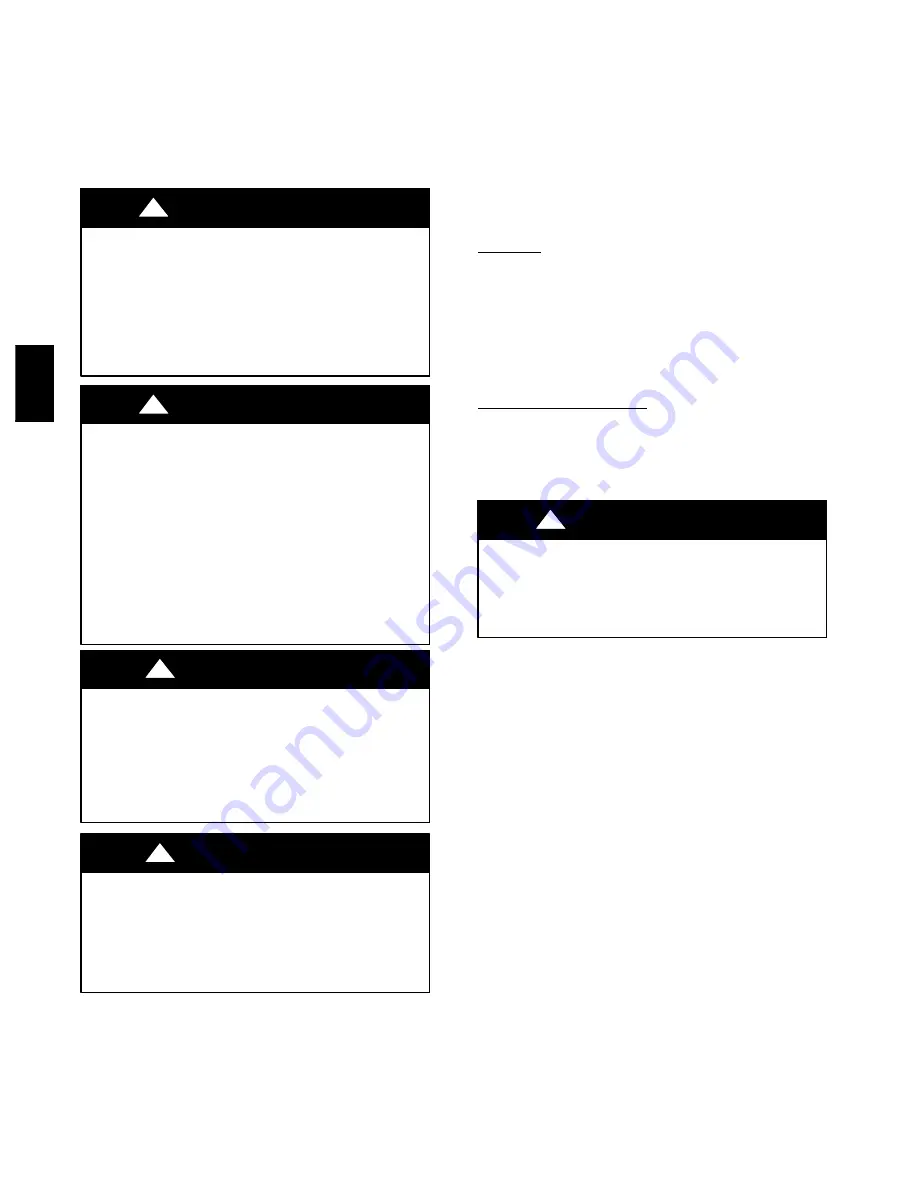
28
MAINTENANCE
To ensure continuing high performance and to minimize the
possibility of premature equipment failure, periodic maintenance
must be performed on this equipment. This combination
heating/cooling unit should be inspected at least once each year by
a qualified service person. To troubleshoot cooling or heating of
units, refer to Tables 10, 11 and 12.
NOTE
: Consult your local dealer about the availability of a
maintenance contract.
PERSONAL INJURY AND UNIT DAMAGE HAZARD
Failure to follow this warning could result in personal injury
or death and unit component damage.
The ability to properly perform maintenance on this
equipment requires certain expertise, mechanical skills, tools
and equipment. If you do not possess these, do not attempt to
perform any maintenance on this equipment, other than those
procedures recommended in the Owner’s Manual.
!
WARNING
ELECTRICAL SHOCK AND EXPLOSION HAZARD
Failure to follow these warnings could result in personal
injury or death:
1. Turn off electrical power to the unit and install a lockout
tag before performing any maintenance or service on this
unit.
2. Use extreme caution when removing panels and parts.
3. Never place anything combustible either on or in contact
with the unit.
4. Should overheating occur or the gas supply fail to shut
off, turn off external main manual gas valve to the unit.
Then shut off electrical supply.
!
WARNING
CUT HAZARD
Failure to follow this caution may result in personal injury.
When removing access panels (see Fig. 19) or performing
maintenance functions inside your unit, be aware of sharp
sheet metal parts and screws. Although special care is taken
to reduce sharp edges to a minimum, be extremely careful
when handling parts or reaching into the unit.
CAUTION
!
UNIT OPERATION HAZARD
Failure to follow this caution may result in improper
operation.
Errors made when reconnecting wires may cause improper
and dangerous operation. Label all wires prior to
disconnecting when servicing.
CAUTION
!
The minimum maintenance requirements for this equipment are as
follows:
1. Inspect air filter(s) each month. Clean or replace when
necessary. Certain geographical locations may require more
frequent inspections.
2. Inspect indoor coil, outdoor coil, drain pan, and condensate
drain each cooling season for cleanliness. Clean when
necessary.
3. Inspect blower motor and wheel for cleanliness at the
beginning of each heating and cooling season. Clean when
necessary. For first heating and cooling season, inspect
blower wheel bi--monthly to determine proper cleaning
frequency.
4. Check electrical connections for tightness and controls for
proper operation each heating and cooling season. Service
when necessary. Ensure electrical wiring is not in contact
with refrigerant tubing or sharp metal edges.
5. Check and inspect heating section before each heating
season. Clean and adjust when necessary.
6. Check flue hood and remove any obstructions, if necessary.
Air Filter
IMPORTANT
: Never operate the unit without a suitable air filter
in the return--air duct system. Always replace the filter with the
same dimensional size and type as originally installed. (See Table 1
for recommended filter sizes.)
Inspect air filter(s) at least once each month and replace
(throwaway--type) or clean (cleanable--type) at least twice during
each heating and cooling season or whenever the filter(s) becomes
clogged with dust and/or lint.
Indoor Blower and Motor
NOTE
: All motors are prelubricated. Do not attempt to lubricate
these motors.
For longer life, operating economy, and continuing efficiency,
clean accumulated dirt and grease from the blower wheel and
motor annually.
ELECTRICAL SHOCK HAZARD
Failure to follow this warning could result in personal injury
or death.
Disconnect and tag electrical power to the unit before cleaning
and lubricating the blower motor and wheel.
!
WARNING
Cleaning the Blower Motor and Wheel
1. Remove and disassemble blower assembly as follows:
a. Remove blower access panel (see Fig. 19).
b. Disconnect 5 pin plug and 4 pin plug from indoor
blower motor. Remove capacitor if required.
c. On all units, remove blower assembly from unit.
Remove screws securing blower to blower partition and
slide assembly out. Be careful not to tear insulation in
blower compartment.
d. Ensure proper reassembly by marking blower wheel and
motor in relation to blower housing before disassembly.
e. Loosen setscrew(s) that secures wheel to motor shaft.
Remove screws that secure motor mount brackets to
housing, and slide motor and motor mount out of
housing.
2. Remove and clean blower wheel as follows:
a. Ensure proper reassembly by marking wheel orientation.
b. Lift wheel from housing. When handling and/or
cleaning blower wheel, be sure not to disturb balance
weights (clips) on blower wheel vanes.
c. Remove caked--on dirt from wheel and housing with a
brush. Remove lint and/or dirt accumulations from
wheel and housing with vacuum cleaner, using soft
brush attachment. Remove grease and oil with mild
solvent.
d. Reassemble wheel into housing.
e. Reassemble motor into housing. Be sure setscrews are
tightened on motor shaft flats and not on round part of
shaft. Reinstall blower into unit. Reinstall capacitor.
48E
Z
--
A
Summary of Contents for 48EZ(N) - A
Page 3: ...3 A09450 Fig 2 48EZ A24 36 Unit Dimensions 48EZ A...
Page 4: ...4 A09451 Fig 3 48EZ A42 60 Unit Dimensions 48EZ A...
Page 25: ...25 A09068 Fig 15 208 230 1 60 Wiring Diagram Unit 48EZ A 48EZ A...
Page 26: ...26 A09209 Fig 16 208 230 3 60 Wiring Diagram Unit 48EZ A 48EZ A...
Page 27: ...27 A08019 Fig 17 Cooling Charging Table Subcooling 48EZ A...