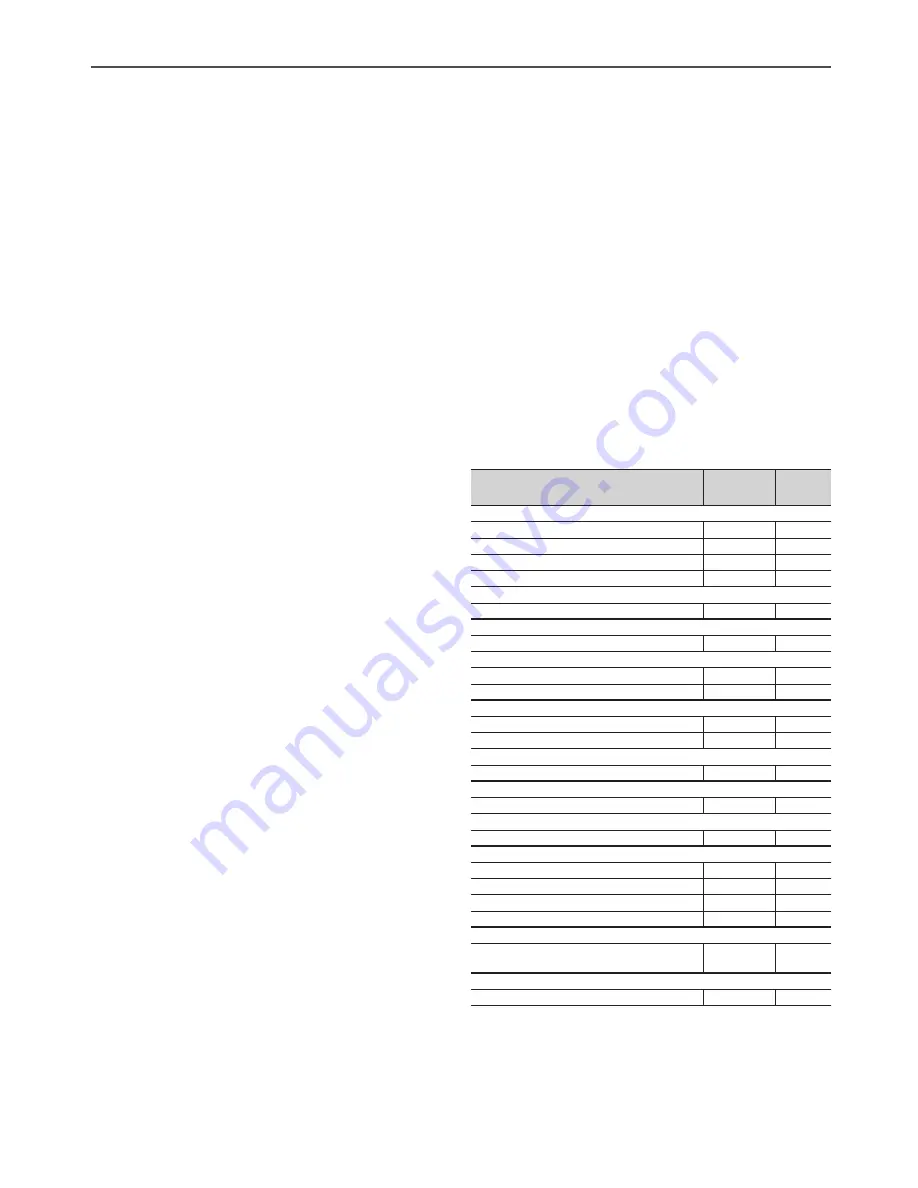
29
13 - STANDARD MAINTENANCE
Air conditioning equipment must be maintained by professional
technicians, whilst routine checks can be carried out locally by
specialised technicians. See the standard EN 378-4.
Simple preventive maintenance will allow you to get the best
performance from your HVAC unit:
-
improved cooling performance
-
reduced power consumption
-
prevention of accidental component failure
-
prevention of major time-consuming and costly interventions
-
protection of the environment
There are five maintenance levels for HVAC units, as defined by
the AFNOR X60-010 standard.
13.1 - Level 1 maintenance
See note below.
Simple procedure can be carried out by the user:
-
Air heat exchanger (condenser) cleaning - see chapter
“Condenser coil - level 1”
-
Check for removed protection devices, and badly closed
doors/covers
-
Check the unit alarm report when the unit does not work (see
report in the 19PV Touch'Pilot Control instruction manual ).
General visual inspection for any signs of deterioration.
13.2 - Level 2 maintenance
See note below.
This level requires specific know-how in the electrical, hydraulic
and mechanical fields. It is possible that these skills are available
locally: existence of a maintenance service, industrial site,
specialised subcontractor.
In these cases, the following maintenance operations are
recommended.
Carry out all level 1 operations, then:
-
At least once a year tighten the power circuit electrical
connections (see tightening torques table).
-
Check and re-tighten all control/command connections, if
required (see tightening torques table).
-
Check the differential switches for correct operation every 6
months.
-
Remove the dust and clean the interior of the control boxes,
if required. Check the filter condition.
-
Check the presence and the condition of the electrical
protection devices.
-
Replace the fuses every 3 years or every 15000 hours (age-
hardening).
-
Replace the control box cooling fans (if used) every five years.
-
Check the water connections.
-
Purge the water circuit (see chapter 7 “Water connections”).
-
Clean the water filter (see chapter 7 “Water connections”).
-
Check the unit operating parameters and compare them with
previous values.
-
Replace compressor capacitors every 10 years (if energized)
or 5 years (if de-energized).
-
Replace compressor soft start fan every 5 years.
-
Keep and maintain a maintenance sheet, attached to each
HVAC unit.
All these operations require strict observation of adequate safety
measures: individual protection garments, compliance with all
industry regulations, compliance with applicable local regulations
and using common sense.
13.3 - Level 3 (or higher) maintenance
See note below.
The maintenance at this level requires specific skills/approval/
tools and know-how and only the manufacturer, his representative
or authorised agent are permitted to carry out these operations.
These maintenance operations concern for example:
-
A major component replacement (compressor, evaporator)
-
Any intervention on the refrigerant circuit (handling refrigerant)
-
Changing of parameters set at the factory (application
change)
-
Removal or dismantling of the HVAC unit
-
Any intervention due to a missed established maintenance
operation
-
Any intervention covered by the warranty
NOTE: Any deviation or non-observation of these maintenance
criteria will render the guarantee conditions for the HVAC unit
nul and void, and the manufacturer, will no longer be held
responsible.
13.4 - Tightening of the electrical connections
13.4.1 - Tightening torques for the main electrical
connections
Component
Designation
in the unit
value
(N·m)
Screw on bus bar and PE, customer connection
M6
L1/L2/L3
9,6
M8
L1/L2/L3
24
M10
L1/L2/L3
49
M12
L1/L2/L3
79,4
Screw on Main supply disconnect switch
QS10*
28
Screw on Control supply disconnect switch
QS10*A
1,7
Screw on Line reactor
Line reactor for TT300 - M8
Z*
24
Line reactor for TT350 - M10
Z*
49
Screw on EMC Filter
PE
ZC*
16 (+/- 1)
Phases
ZC*
15
Screw on Fast acting fuse connection
FU*
38
Screw on TT300 bar connection
L1/L2/L3
25
Screw on PE panels
M8
PE
24
Screw on Compressor connection
TT300 - Cap
L1/L2/L3
31
TT300 - M8
PE
21,7
TT350 - M10
L1/L2/L3
21,7
TT350 - M8
PE
21,7
Control disconnect switch connection
Upstream and downstream screws at terminals
QF10* &
QM10**
2
Power supply 24VDC unit
Upstream and downstream screws at terminals
VC*
0,5
Summary of Contents for 19PV550
Page 33: ...33...