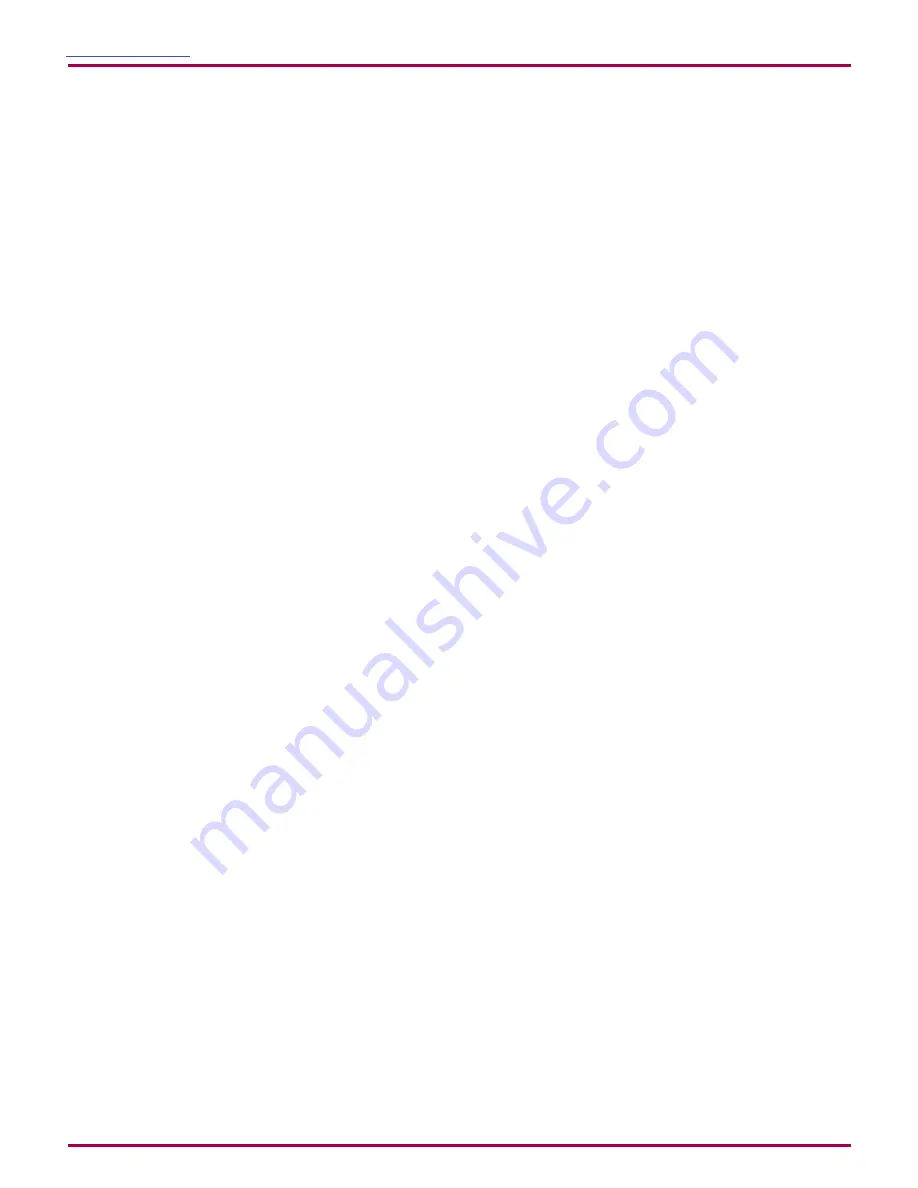
pressure. This is due to the Integral term of the PID control.
If the restriction causing the low flow condition is removed
suddenly while a large control output signal exist, then a
relatively long amount of time is required for the Integral
term of the PID to reduce the control output back to a normal
range since the Integral term is proportional to time and
also due to the inherent response of the system. If fluid flow
response has changed significantly with the same setup
that previously produced good response, then inspect the
system for component failure, blockages, and check the
fluid type and viscosity.
Alternate PID Equation
The normal PID equation is based on the error between the
desired set point and the actual flow rate for the CHANNEL.
If the set point is varied dynamically by a PLC via RIO or by
a robot via Analog Input, it may be desirable to implement
an alternate form of the equation. The alternate form of
the equation uses the set point for the proportional term
of the equation. The Integral and Derivative terms are the
same, but slightly different scale factors are used.
To enable the alternate PID equation, turn on DIP SW1-4
(or SW1-8) on the Channel Module for each CHANNEL
of the GUN.
PID Tuning Methods - Standard PID
1. Select the nominal flow rate for the GUN.
2. Set Kp and Kd parameters to zero. Do this for both
CHANNELS if this is a two-component GUN.
3. Set Ki for the Slave CHANNEL to zero (assuming this
is a two-component GUN).
4. Set Ki for the Master CHANNEL to the default value
shown in "Default Control Parameters" chart and
"Typical Ranges for Control Parameters" chart in this
section.
5. Cycle the GUN from READY to RUN so the new pa-
rameters are sent to the Channel Module(s).
6. Trigger the GUN. If the flow rate does not oscillate, or
the oscillations decrease in amplitude in a few seconds,
increase Ki by 100 and repeat from step 5. If the flow
rate oscillates with increasing amplitude, decrease Ki
by 50 and repeat from step 5. 8If the flow rate oscillates
with a constant amplitude, proceed to step 7.
7. Set Ki to one-half the present value.
8. Set Kp to the default value shown in the "Default Con-
trol Parameters chart" and Typical Ranges for Control
Parameters chart" in this section.
9. Cycle the GUN from READY to RUN so the new pa-
rameters are sent to the Channel Mod-ule(s).
10. Trigger the GUN. If the flow rate does not oscillate, or
the oscillations decrease in amplitude in a few seconds,
increase Kp by 30 and repeat from step 9. If the flow
rate oscillates with increasing amplitude, decrease Kp
by 15 and repeat from step 9. If the flow rate oscillates
with a constant amplitude, proceed to step 11.
11. Set Kp to one-third the present value.
12. Cycle the GUN from READY to RUN so the new pa-
rameters are sent to the Channel Module(s).
13. Trigger the GUN. If the flow rate does not oscillate, pro-
ceed to step 14. If the flow rate is oscillating, reduce Ki
by 50 and/or reduce Kp by 15 and repeat from step 12.
14. At this point, the tuning procedure is completed for
most flow control applications. However, if there is a
great amount of lag time from the point of sensing
the flow rate to where the material volume regulator is
located, the derivative term of the PID equation may
be required. In that case, set Kd to the default value
shown in "Default Control Parameters" chart and
"Typical Ranges for Control Parameters" chart in this
section.
15. Cycle the GUN from READY to RUN so the new pa-
rameters are sent to the Channel Module(s).
LN-9400-00-R11 (08/2018)
56 / 96
www.carlisleft.com
PARTS IDENTIFICATION