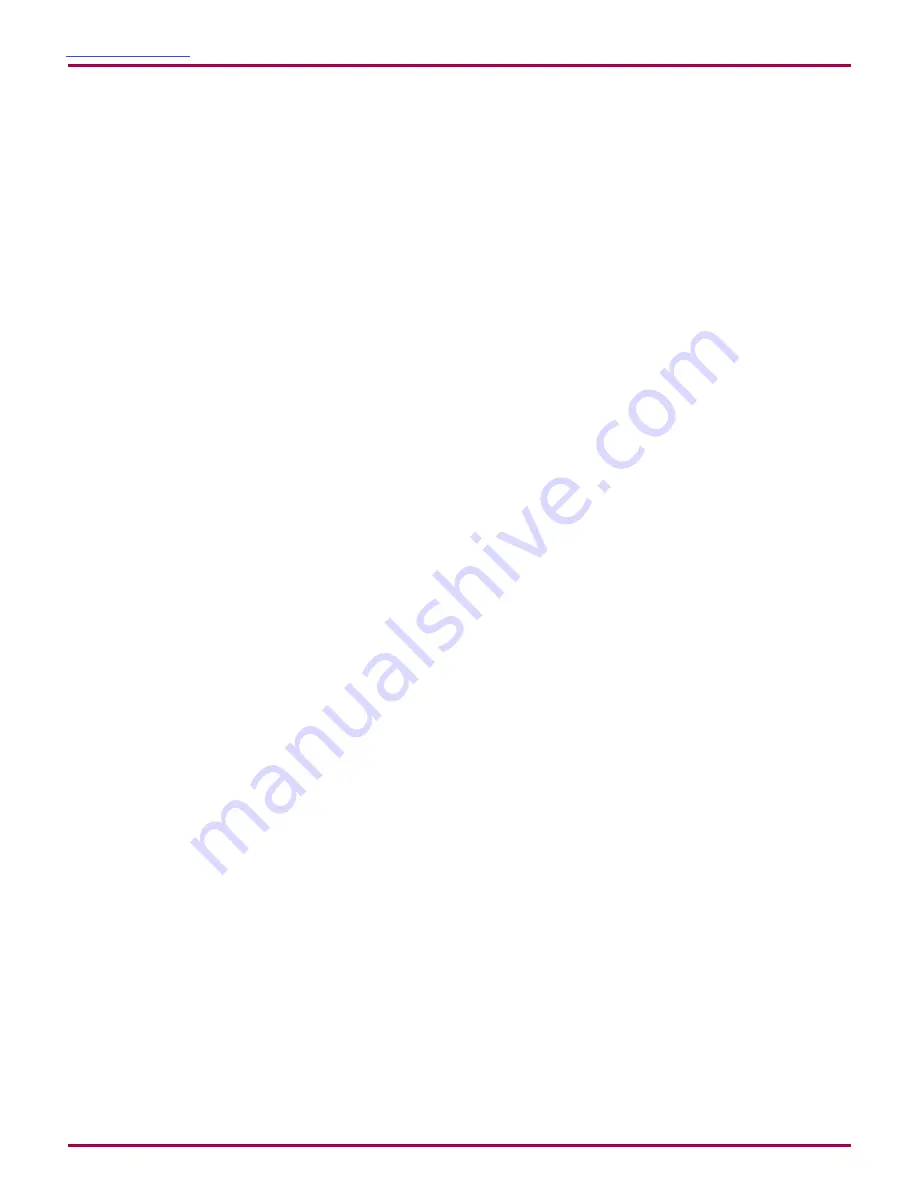
Hardware Configuration
Reference "Addendum A" in the "Appendix" section for board
level hardware settings. For new system installations, all
hardware settings should already be in the correct positions.
However, if replacing any electronic board assembly, verify
that the settings of the new board are identical to those of
the board being replaced. In the event that the replacement
board is a newer revision and does not appear identical,
refer to any documentation that was supplied with the
board, or contact your Ransburg representative or contact
Ransburg service.
Transducers
The transducers convert electrical control signals from
the fluid flow controller to the air pressure signals used to
operate the material regulators. The transducers can be
either current controlled (4-20 ma) or voltage controlled
(0-10 VDC). The transducers can be mounted separately
or collectively depending on the installation requirements.
Make sure that the Channel Module jumper settings match
the type of transducer being used (refer to "Channel Module
Mother Board Jumper Settings Channel 1 I/O and Channel
2 I/O" in the "Appendix" section).
The electrical-to-pneumatic (E/P) transducers are supplied
as separate sub-assemblies or as part of a standard
transducer panel. The transducer panel offers a convenient
way to mount transducers for 2K applications. There are
typically two transducers located in each panel with electrical
terminals and an air supply input.
The transducers may also be mounted individually on any air
drop
outside
of the Class 1, Division 1 hazardous location if:
1. Tubing and cable lengths do not violate the minimum
and maximum lengths specified in the "Installation" section
of this manual under Equipment Locations".
2. The air supply meets the specifications as listed in the
"Introduction" section of this manual under "Pneumatic
Specifications" or those published with the transducer.
A 1:1 volume booster may also be connected directly to the
transducer output when; operating a DR-1
TM
Fluid Regulator,
if pilot line lengths are longer than recommended, or of a
larger tubing diameter is used other than that recommended.
Keep the distance between the transducer to the material
regulator as short as possible, without violating the minimum
lengths specified, to avoid system response delays and to
achieve the optimum fluid flow characteristics for the system.
Material Regulators and Flow Meters
The location and mounting of the material regulators and
flow meters is specific to each installation. The information
presented here is intended as a guideline only. Reference
should be made to the supplied documentation specific to
your installation.
Fluid Supply Requirements
• The fluid supply must be free of pulsation and surges.
• A fluid strainer/filter must be installed immediately before
the material regulators. The elment size of the strainer
should be 100 mesh or per the recommendation of your
Ransburg representative.
• For Two-Component (2K) Systems: Selector valves are
required for calibration or verifying of the flow meters and
should be mounted close to the mixing block. These are
supplied as part of the standard fluid panel. Drawings
created specifically for your system will provide detailed
information about valve type and location. Mount the
calibration valves in an easily accessible area close to
the mixing block. For most applications the flow meter
and material regulator are mounted as an assembly as
close as possible to the mixing block and calibration
valves.
• For systems with fast trigger cycles that utilize weepless
MVR valves, or where dynamic control of fluid flow rates
(different flow rate during a JOB), consider installing
trigger valves (typically color control valves) immediately
upstream of the MVR valves so that the CHANNELs may
be placed in Analog Hold mode without causing the fluid
tubes to pressurize to the material supply pressure while
the GUN is not triggered.
• For systems with fast trigger cycles or where dynamic
control of fluid flow rates (different flow rates during a
JOB), mount the E/P transducer as close to the material
regulator as possible. Remember that the transducers
MUST be mounted outside of the hazardous location
(refer to NFPA-70, NEC). For applications where the
requested fluid flow is for the most part consistent, and
transitional response time of the system is not as critical,
then the E/P transducers may be located in the main
control panel.
• Be sure that stainless steel tubing or piping and stainless
steel fittings are used for all fluid lines and connections
where metal is desired.
• Always mount the flow meter and regulator as close as
feasible to the applicator. This reduces paint line pulsation
due to applicator reciprocators and reduces the possibility
of a paint leak effecting paint delivered to the part.
LN-9400-00-R11 (08/2018)
28 / 96
www.carlisleft.com
INSTALLATION